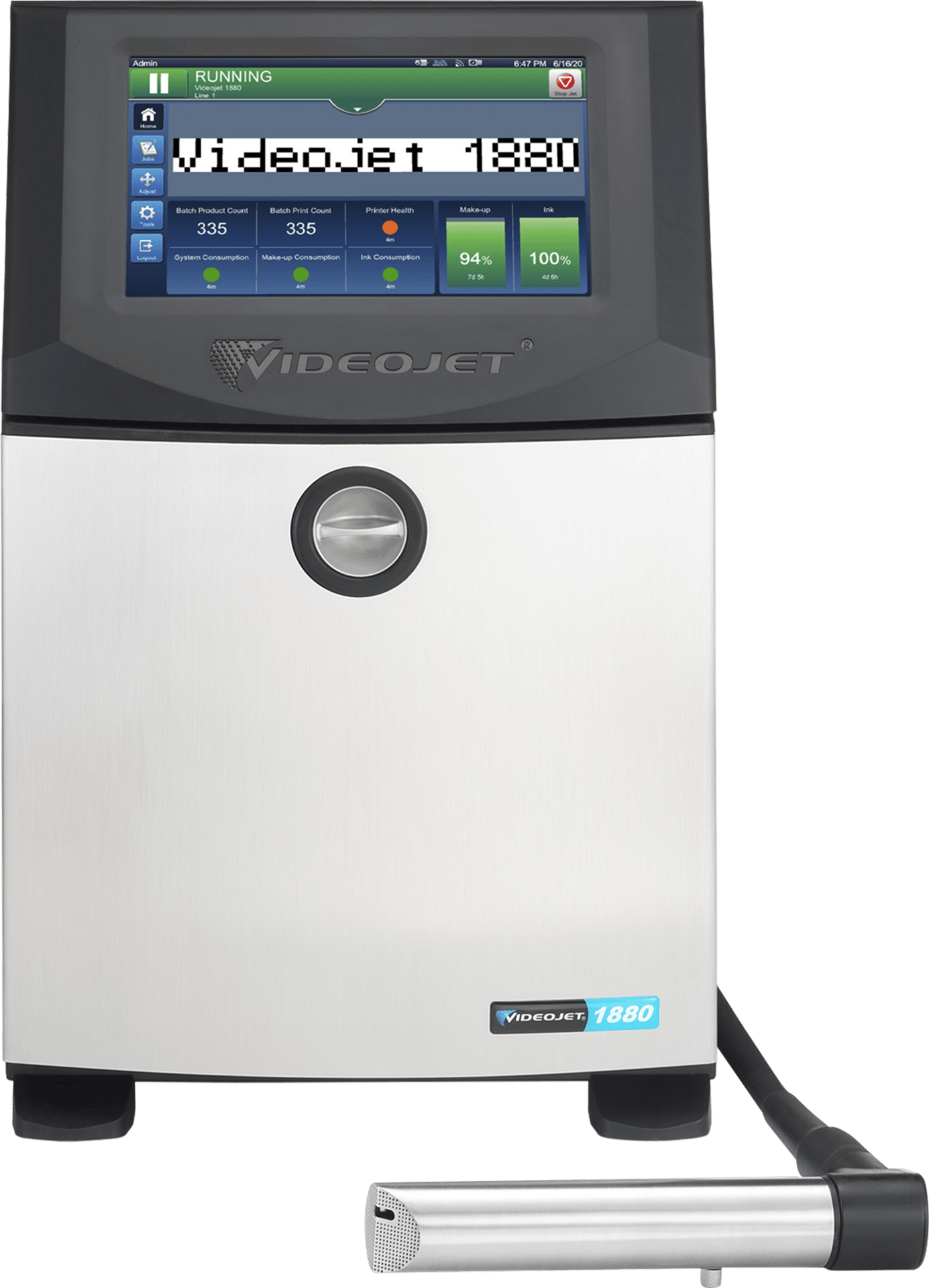
Continuous inkjet (CIJ) printers are commonly used to print dates and codes on frozen goods because of their versatility on the packaging line. However, the low temperatures typical of these processing facilities can lead to printing issues, making it critical to carefully select specialized inks and CIJ printers that can provide reliable performance and achieve high print quality and proper code adhesion throughout a product’s lifecycle.
Cold Temperatures: CIJ inks are engineered to perform well over a specific range of temperatures. Among the coldest common operating environments, the temperatures in frozen foods production environments are often below the typical temperature specifications of many inks. Only certain inks are specifically formulated to achieve the best adhesion, durability and printer performance in colder environments down to 0°C.
Condensation: Products and packaging may be exposed to temperature changes throughout the supply chain. For example, a warm package may be filled with a cold product or a grocer’s freezer door may be left open. These changes in temperature, combined with humidity in the air, can cause condensation on products before and after coding. The wrong ink and printer selection may result in codes that smudge or transfer.
Ink Selection: Small changes to your production environment, like a change in temperature, can significantly influence the type of ink that will work best. If a product has condensation on it during the printing process, certain penetrating ink formulations can be used to print codes that adhere to the packaging and resist transferring onto adjacent products or production line conveyance systems.
In addition, cold and moisture-promoting environments throughout the product’s lifecycle, like a grocer’s or consumer’s freezer, may result in smudged codes. To combat this, solvent-based, transfer-resistant inks with excellent adhesion are often selected. Of course, your application may require an ink with multiple properties. An experienced ink manufacturer or supplier can help identify the ideal ink to meet the unique requirements for your substrate and application.
Production Processes: It may be possible to alter your production processes for better ink performance. For example, a printer may be moved to a location on the line where condensation is less likely to form on the packaging before print is applied, therefore not requiring an ink that must penetrate condensation. In extreme environments, the printer may be contained in an environmental cabinet to control temperature and humidity.
Printer Selection: In a frozen foods operation, the ink must be matched with a printer designed to perform in extreme cold. Certain printers are adept at solving some of the ink issues associated with this environment. For example, CIJ printers that continuously calibrate and adjust ink viscosity can produce reliable, clear and consistent codes, even at the end of long production runs in conditions down to 0°C/32°F. Additionally, some printers contain a heater built into the printhead to help maintain a stable and suitable temperature.
Your operation may require features such as an adjustable 90° printhead or unique mounting options to provide closer proximity to the product. Other features, like sensors that alert the operator to potential print quality issues, are ideal for low-temperature conditions where ink can build up quickly in a printhead.
Choose an Experienced Frozen Foods Package Printing Partner: Choose a vendor that has knowledge of cold printing needs, specialty ink formulations, and printers that have been engineered for your operating environment. Provide samples of the materials you will be printing on and have your vendor test different inks to help select the best one for your application. Lean on an experienced partner who can help you determine the best fit for your frozen foods operation.
Mark Breunig is the regional product manager at Videojet Technologies.