Embracing Efficiency
Hygienic improvements with conveyors have allowed the packaging process to become even more streamlined.
By Bobby Douglas
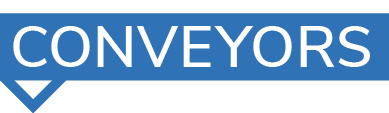
As the packaging process becomes increasingly automated, a key area of focus for suppliers has been conveyors. Suitable for nearly every packaging sector, conveyors have become more popular due to their versatility and general ease of use. Perhaps one challenge when it comes to fully implementing conveyors, though, is hygiene, as maintaining sanitary conditions is a difficult and often time-consuming process. That being said, several companies are taking steps to mitigate this issue.
- Key Technology’s new conveying systems for robotic pick-and-place packaging are highly automated, which limits the need for hand-packing, which can often be unsanitary.
- Rotzinger Group’s hygienic conveyor features a unique design that limits the amount of residue left on the belt, thus allowing for easier cleaning processes.
- Cablevey developed a “smart cart” that makes the cleaning of tubular drag conveyors much more efficient.
- And finally, Dorner and Garvey developed the AquaGard GT, a conveyor system that is primarily made of stainless steel and FDA-approved plastics.
Read more about all these innovations in conveyors below.
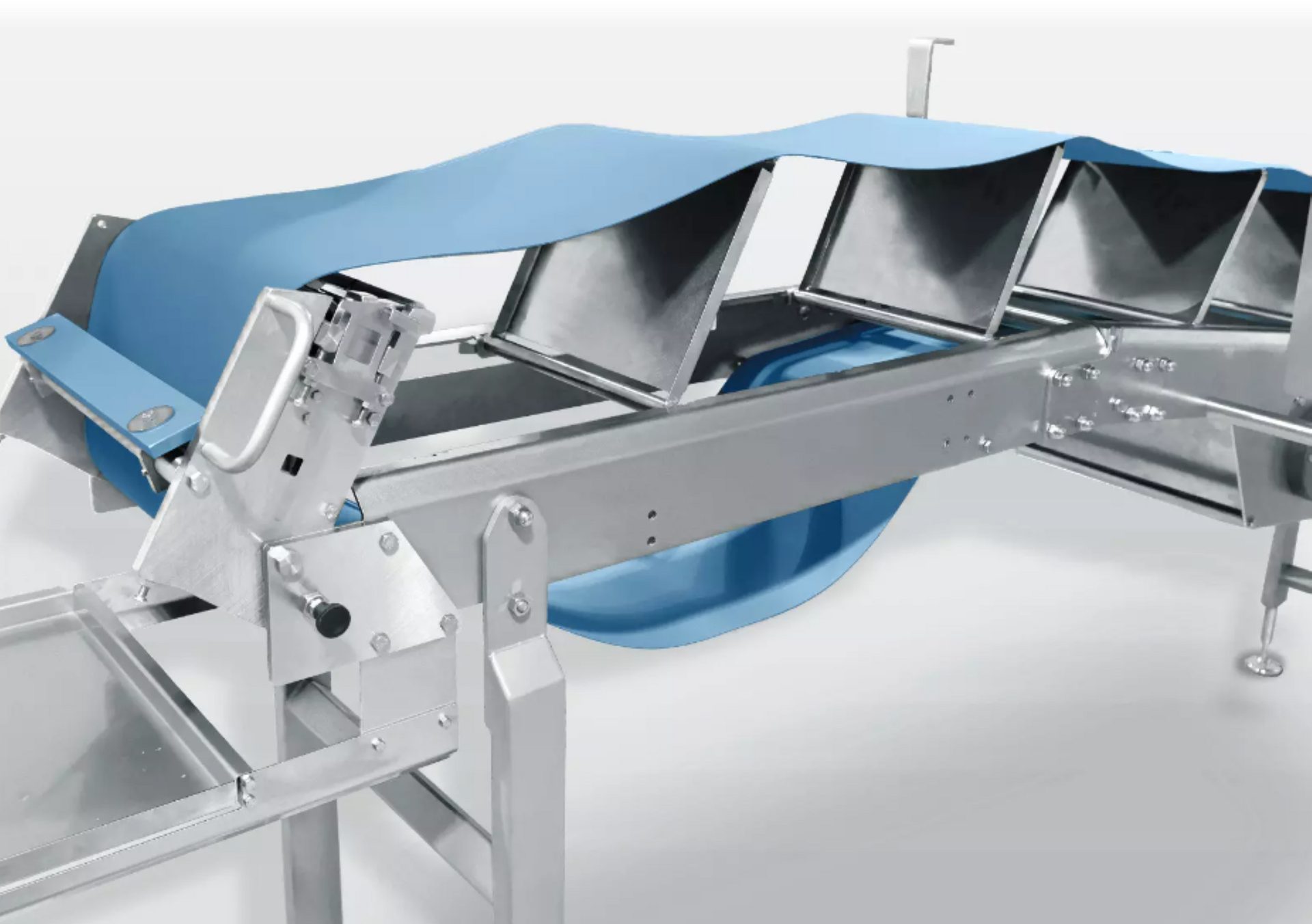
Rotzinger’s hygienic conveyor allows for easy cleaning.
Courtesy of Rotzinger Group
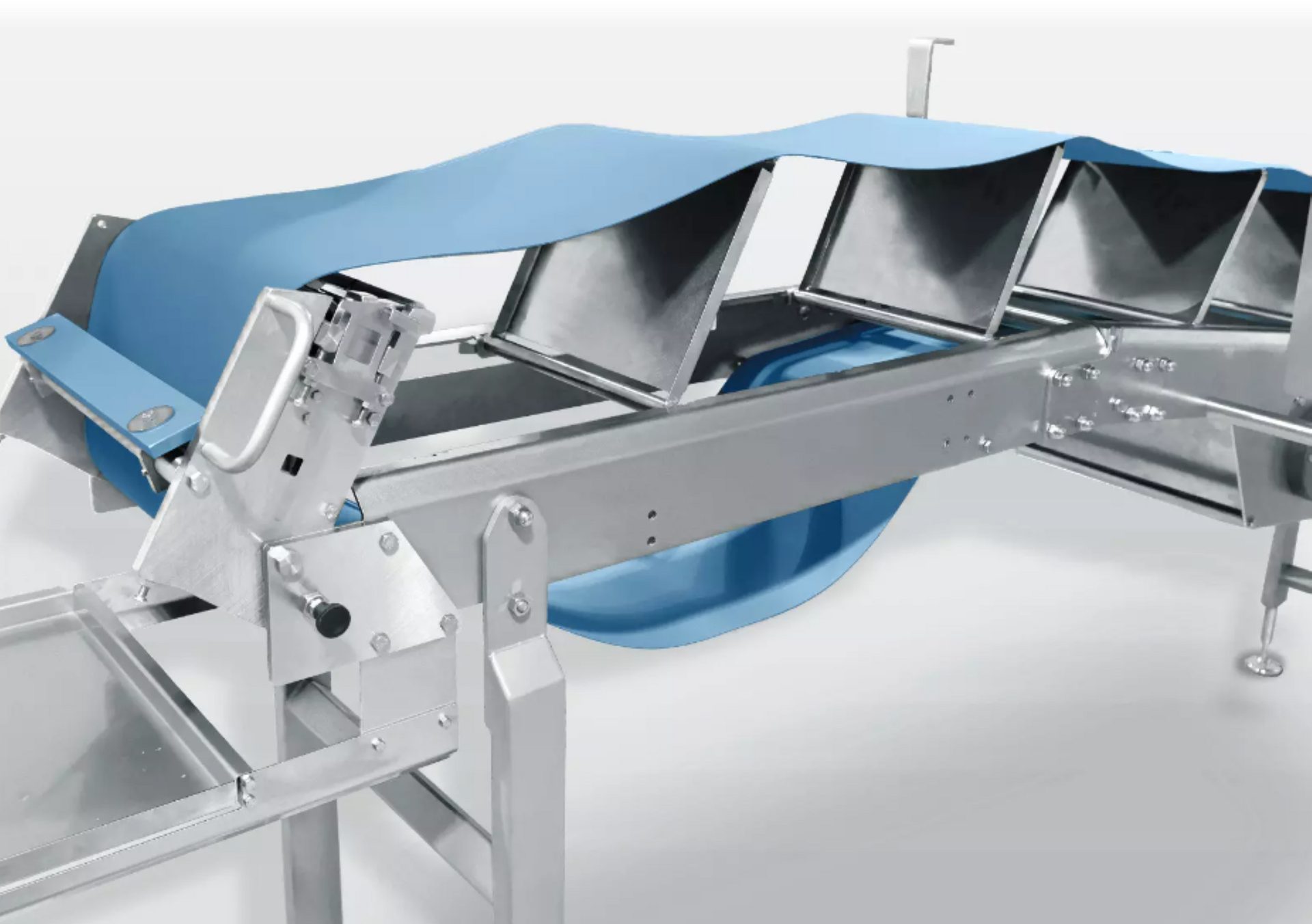
Rotzinger’s hygienic conveyor allows for easy cleaning.
Courtesy of Rotzinger Group
ADVERTISEMENT
Key Technology Introduces New Conveying Systems for Robotic Pick-and-Place Packaging
Key Technology, a member of the Duravant family of operating companies, has introduced their new vibratory conveying systems designed to feed pick-and-place robots on packaging lines. Each series of integrated conveyors meters, separates, singulates and/or aligns product, depending on the application, to provide the optimal product separation, speed and orientation for ideal presentation to the robotic system for pick-up. By minimizing hand packing, these new systems help increase production efficiency, reduce labor and improve sanitation.
READ MORE
“As a food processor grows, they come to a point when hand packing has to be minimized or is no longer feasible. Manually packaging, especially 24/7 with several workers at a time, is expensive, inconsistent and can be unsanitary, plus these jobs are physically grueling with high turnover. It’s a huge pain point for many of our customers — automation makes sense,” said Jack Lee, Duravant Group President — Food Sorting and Handling Solutions. “The challenge is that lining up products for presentation to a pick-and-place robot requires a degree of precision that’s unusual in conveying. Drawing on our team’s deep expertise, we work closely with each processor to design the perfect solution for their specific application.”
Key designs, builds and then tests every integrated conveying system to identify the optimal speed, stroke, lane widths and step sizes to consistently present the processor’s products to the robot’s end of arm tooling. Suitable for primary or secondary packaging, these systems can handle frozen foods such as potato products, meat, poultry and seafood as well as dry products such as cookies, pet treats, confectionaries and snacks.
The integrated conveying system often begins with an optional shaker or belt conveyor to meter product, if needed. Then, a separating shaker evenly spreads product, followed by a singulating shaker that directs product into single-file lanes. The next shaker aligns the product in the correct direction, if required, and achieves the optimal speed to feed one or more pick-and-place robots, which are installed on one or both sides of the conveyor. Products that are not picked up by the robots can either be collected in a hopper or recirculated to the beginning of this system.
Key’s robust vibratory conveyors are designed for superior sanitation with stainless-steel bed surfaces, open designs and oil-free drives. When a processor automates primary packaging, sanitation is further enhanced by eliminating the manual handling of unpackaged products in the packing process while reducing the chance of accidental foreign material contamination by a worker.
Key manufactures conveyors and other equipment in both the U.S. and Europe, supports customers worldwide through its extensive sales and SupportPro service network and offers integration services, from pre-engineering to line start-up. Key’s conveyor beds and structural components are backed by their industry-leading, five-year warranty.
For more information, visit key.net.
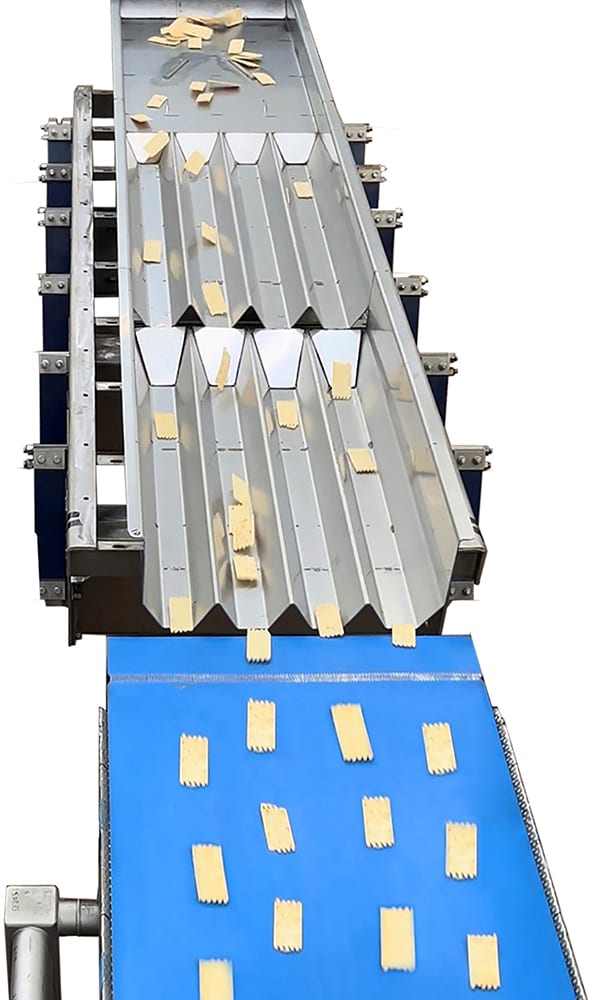
The vibratory conveying systems allow for the minimization of manual packaging.
Courtesy of Key Technology
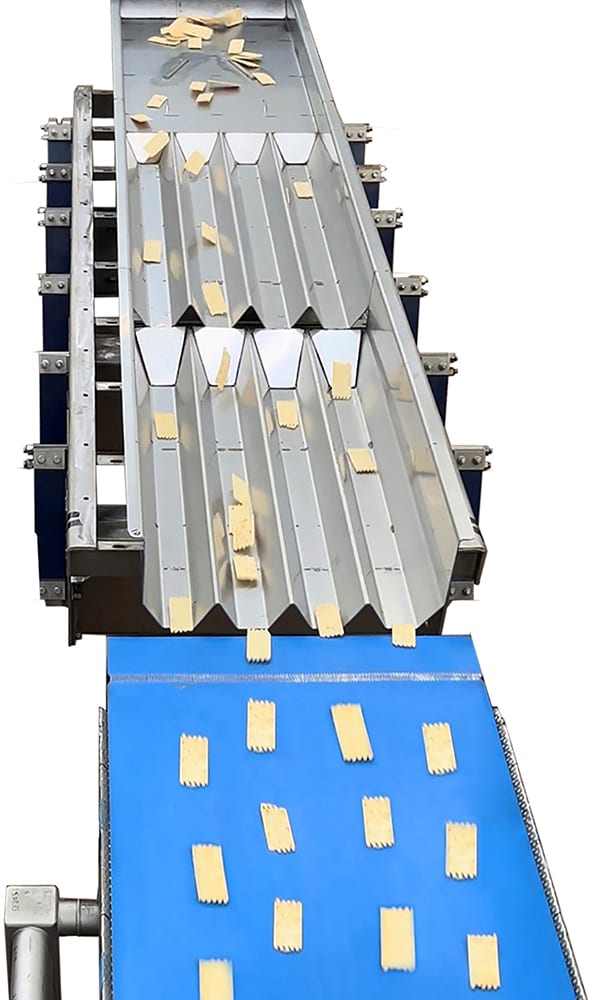
The vibratory conveying systems allow for the minimization of manual packaging.
Courtesy of Key Technology
COLLAPSE ARTICLE ABOVE
Rotzinger Group Unveils a Robot with an Integrated Buffer and Hygienic Conveyor at PACK EXPO Las Vegas
Rotzinger Group, a leading provider of automation solutions, recently launched its highly advanced Robot with an Integrated Buffer and its Hygienic Conveyor for dry cleaning. The groundbreaking technologies were showcased at PACK EXPO Las Vegas in September. Leveraging decades of expertise in pick and place delta robots, buffering and conveying, the new integrated solution from Rotzinger combines flexibility, compactness, and ease of operation to boost uptime and reduce the total cost of ownership. Designed for confectionery and bakery products, the hygienic conveyor is optimized for dry cleaning, ensuring compliance with stringent food safety regulations in US manufacturing.
“Our Robot with an Integrated Buffer and Hygienic Conveyor have been specifically designed to tackle the escalating concerns regarding labor shortages, space limitations and heightened sanitary requirements in food production,” said Nicolas Garcia, Vice President & General Manager, Rotzinger Group, North America. “With intuitive controls and a streamlined design, these solutions enhance productivity and optimize operations.”
READ MORE
The integrated solution combines delta robots, buffers and conveyors in one cell.
Courtesy of Rotzinger Group
With its modular design and flexibility, this integrated solution combines delta robots, buffers and conveyors in one cell with a reduced footprint, enabling greater efficiency, productivity and cost-effectiveness. The use of a single controller and a unified setup philosophy enables hassle-free maintenance and straightforward operation, eliminating the need for complex programming or extensive training. The Robot with an Integrated Buffer can be operated by a sole operator, offering simple changeovers facilitated by recipe selection, which automatically adjusts the necessary parameters with just a few clicks.
Equipped with vision-guided high-speed robots, this innovative machine accurately identifies incoming products on the conveyor belt and precisely places them in the feeding process. It utilizes optimal counterflow or co-flow techniques, providing versatile solutions to meet diverse production requirements. By consolidating these capabilities within a single solution, manufacturers can optimize their production lines and achieve early production start-up. The integrated buffering capabilities increase line efficiency and eliminate the need for additional linking conveyors, resulting in cost savings and an optimized layout.
The Hygienic Conveyor was developed for dry cleaning specifically designed to address food safety concerns and adhere to the highest hygienic standards. This innovative conveyor incorporates an intelligent cleaning design, featuring a foldable belt and beveled or rounded horizontal surfaces that prevent the accumulation of dirt particles and crumbs. Additionally, it offers easy accessibility for efficient cleaning and maintenance. The conveyor's stainless-steel construction ensures durability and long-lasting performance.
Furthermore, the Hygienic Conveyor provides flexibility in size range, accommodating a wide range of requirements. It offers width options ranging from 5.9 to 70 inches and length options from 15 to 1377 inches, allowing it to meet the most challenging layout requirements with ease.
To learn more, please visit rotzingergroup.com.
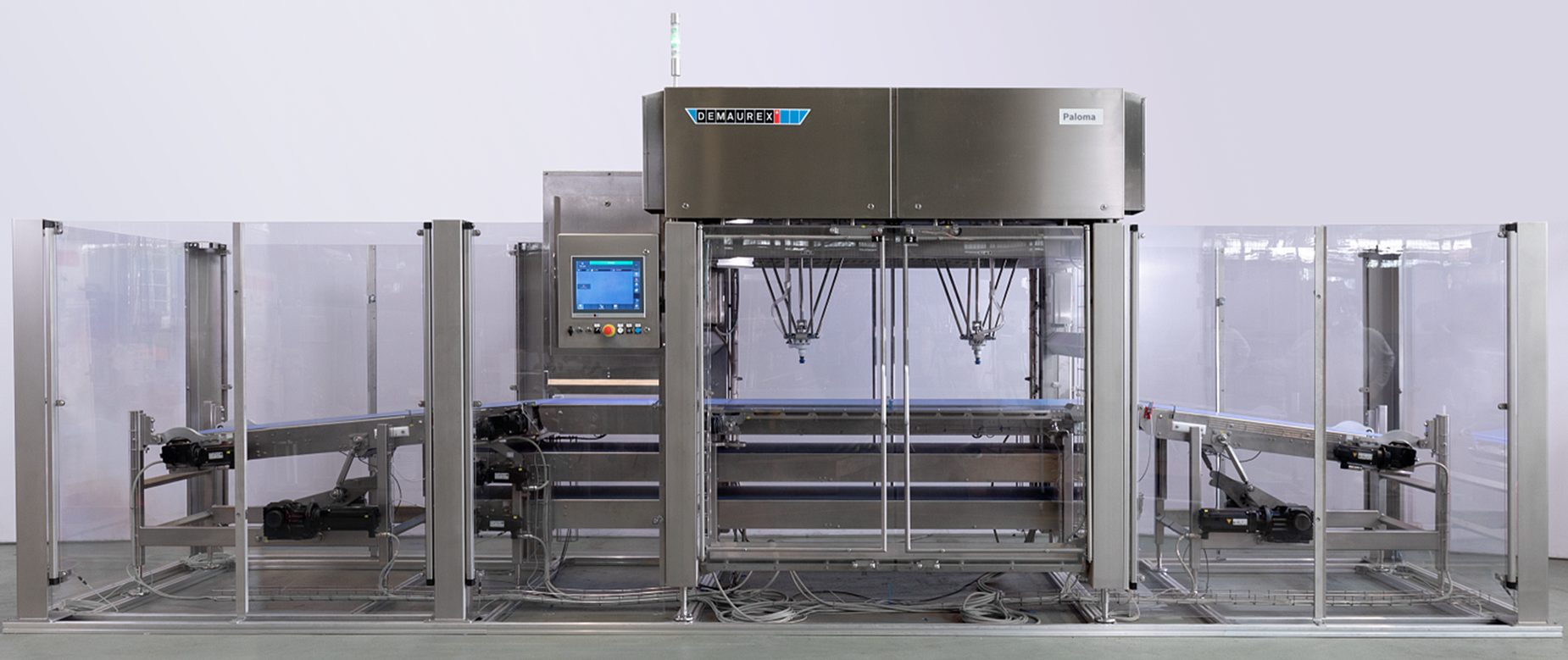
COLLAPSE ARTICLE ABOVE
Cablevey Develops “Smart Cart” to Make CIP Practices Easier for Tubular Drag Conveyors
To promote food safety and sanitary compliance, food packagers are increasingly seeking the ability to Clean-in-Place (CIP), an automated method of cleaning the interior surfaces of tubular drag conveyors without disassembly. Now, with the advent of mobile tools like an innovative “smart cart” that quick-connects to any tubular conveyor and enables simple, customizable “single button cleaning recipes,” CIP is becoming easier, faster, less labor-intensive, more repeatable, and almost fully automated.
Tubular drag conveyor systems gently move product through a sealed, enclosed tube using a drag cable and circular discs pulled through on a loop, so they are ideal for delicate items. In a wet CIP process, the system is flooded with water, flushed, rinsed, cleansed, and thoroughly sanitized. The process thoroughly flushes out any potential allergens like nuts or gluten from conveying equipment and can be used with a variety of food types such as nuts, grains, cereals, powdered soups, and frozen fruits and vegetables.
Although the CIP process is very effective, streamlining its automation and simplifying the process for all of a facility’s tubular drag conveyors has been a priority for leading innovators in the industry.
READ MORE
“The standard system required port hookups to water lines and installing piping. The processor also had to make decisions such as which water temperatures to utilize, or whether to use a cleaning solvent — and the correct amount to add manually,” says John Adair, Engineering and Quality Director for Cablevey Conveyors, an Oskaloosa, Iowa-based conveyor manufacturer that has designed, engineered, and serviced enclosed cable and disc tube conveyors for 50 years, and is in more than 65 countries.
To simplify the wet cleaning process, Adair and his engineering team at Cablevey have developed a small, mobile “smart cart” with integrated water line hookups that a single technician can easily take to any tubular drag conveyor in a facility. The cart is specifically designed to be a fraction of the size of similar carts on the market to facilitate mobility. When the cart is in position and connected to water lines, the CIP process is automated and controlled by a programmable logic controller (PLC) that reduces the need for manual labor and virtually eliminates the risk of improper cleaning.
The smart cart is designed to store and utilize pre-programmed CIP recipes to flush various residual materials from the tubular drag cable conveyors in a facility before new production runs. The cleaning recipes enable even those with very little training to use the cart. This is helpful in today’s tight labor market and allows the technician to move on to other tasks once the cleaning process begins.
The use of easily executable recipes ensures a superior, repeatable clean that essentially “error proofs” the process. This is particularly important when the technician may be new or less familiar with the production equipment.
“Depending on the product being conveyed, sometimes all you need is a wet rinse, or sometimes you need a specific cleaning solvent. All that information is saved, so after the first cleaning, it can be automatically repeated. Just push a button to start the appropriate recipe, whether you have one conveyor running multiple products, or dozens of conveyors running various products,” says Adair.
To facilitate food safety compliance, the smart cart also documents all critical CIP information such as water volume and temperature, chemicals used, and cleaning time by date in an easily retrievable data log.
While the food packaging industry is aware of the benefits of automated CIP, barriers to implementation have slowed adoption. Utilizing a mobile smart cart with integrated water hookups will help packagers to easily implement CIP in tubular drag conveyors throughout their facilities; expediting conveyor cleaning, production changeover, and sanitary compliance.
To learn more, please visit cablevey.com.
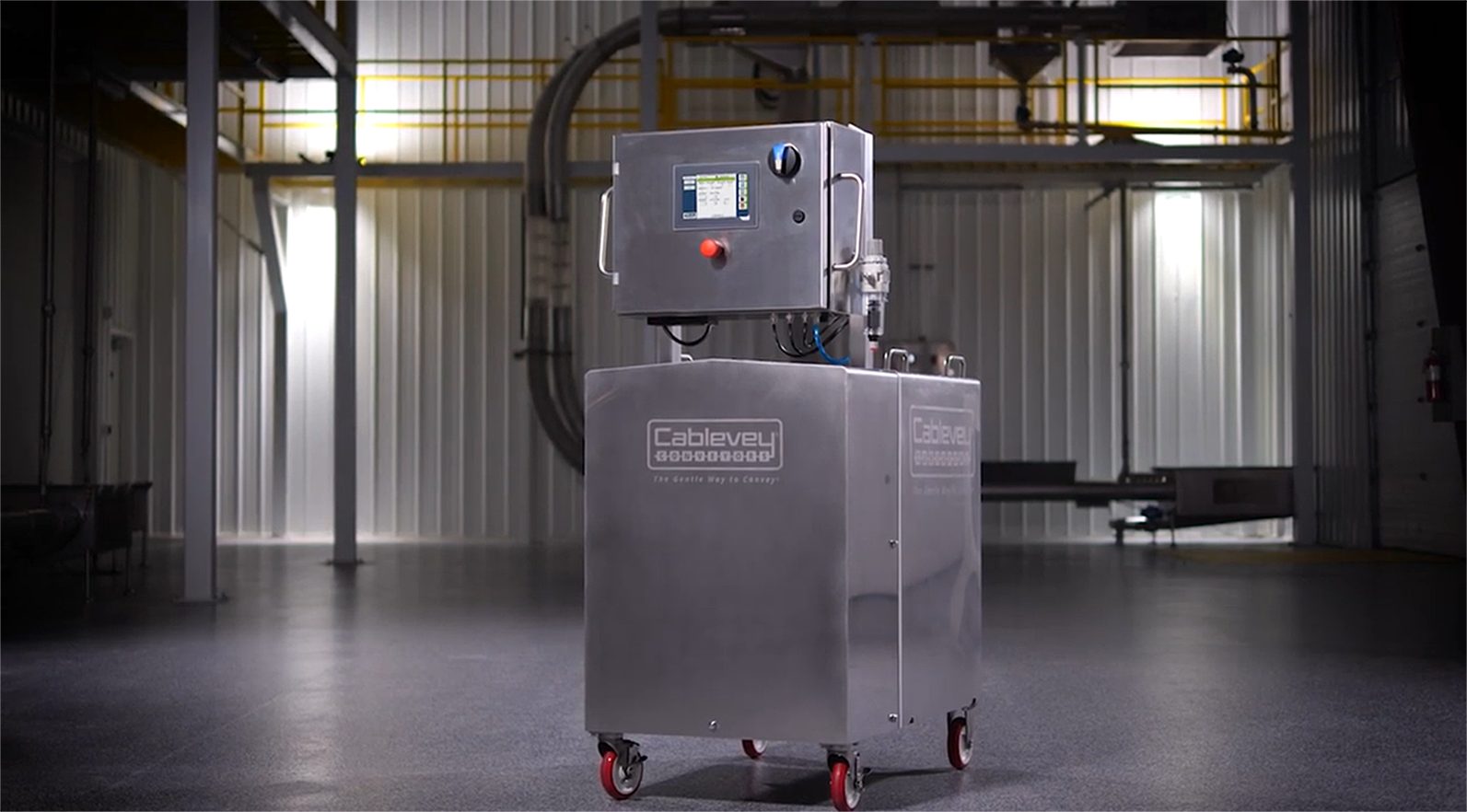
The “smart cart” allows for the cleaning of tubular drag conveyors to become almost entirely automated.
Courtesy of Cablevey
COLLAPSE ARTICLE ABOVE
Dorner and Garvey Showcase the AquaGard GT Conveyor at PACK EXPO Las Vegas
Dorner and Garvey, both Columbus McKinnon brands, recently showcased the AquaGard GT Conveyor at PACK EXPO Las Vegas. Their inaugural joint venture, the AquaGard GT is a conveyor system that has been meticulously designed and crafted to address the needs of accumulation-type applications, thereby preventing bottlenecks in various industries such as packaging, bottling, dry food processing, and part handling. The AquaGard GT plays a crucial role in maintaining smooth and efficient workflow in these industries.
READ MORE
Key Features
- Materials and Hygiene: The AquaGard GT is constructed using premium materials. All components, except for the motors, are crafted from either stainless steel or FDA-approved plastics. This choice of materials is particularly suitable for environments that require regular wipe-downs or occasional washdowns of the conveyor. This ensures both longevity and hygiene compliance.
- Accumulation Prevention: The conveyor’s design focuses on preventing accumulation-related issues, which can lead to production slowdowns. By facilitating continuous movement, the AquaGard GT effectively eliminates bottlenecks and enhances overall efficiency in production processes.
- Integration and Efficiency: The AquaGard GT comes equipped with several innovative features that distinguish it from in-house machine-built conveyors. Notable among these are powered transfer units, flush side tails, and pre-engineered transfer modules. These features are carefully engineered to enhance the conveyor’s efficiency and optimize its performance.
- Competitive Pricing and Quick Delivery: Despite its advanced features and capabilities, the AquaGard GT remains competitively priced. Moreover, its short 10-day lead time ensures that businesses can integrate this conveyor system into their operations swiftly, minimizing downtime and maximizing productivity gains.
The AquaGard GT serves as the critical infeed and outfeed component for the loop, connecting to both the Infinity™ and Bi-Flow™ accumulation tables from Garvey. These tables offer distinct advantages in managing product flow.
To learn more, please visit dornerconveyors.com.
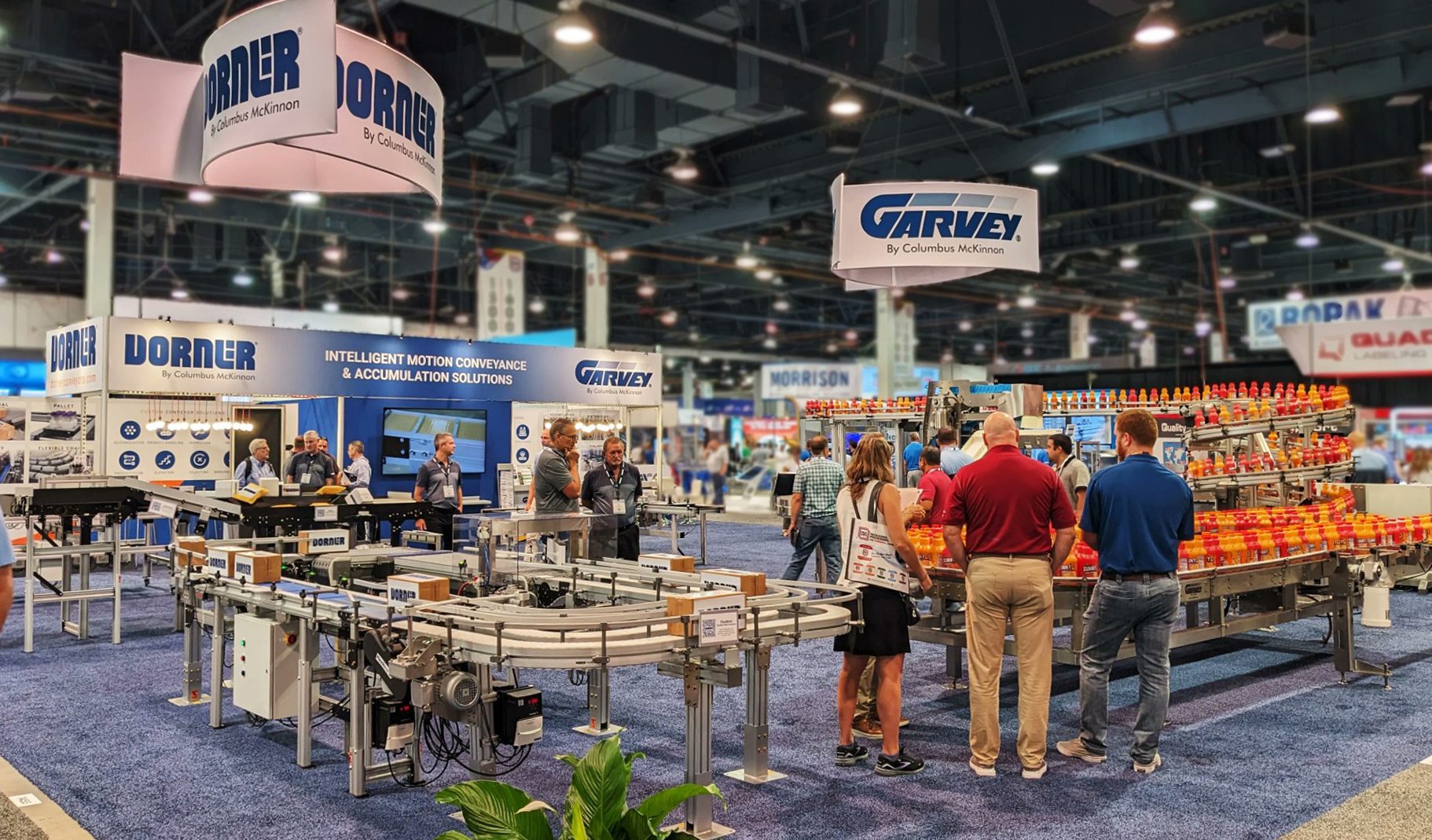