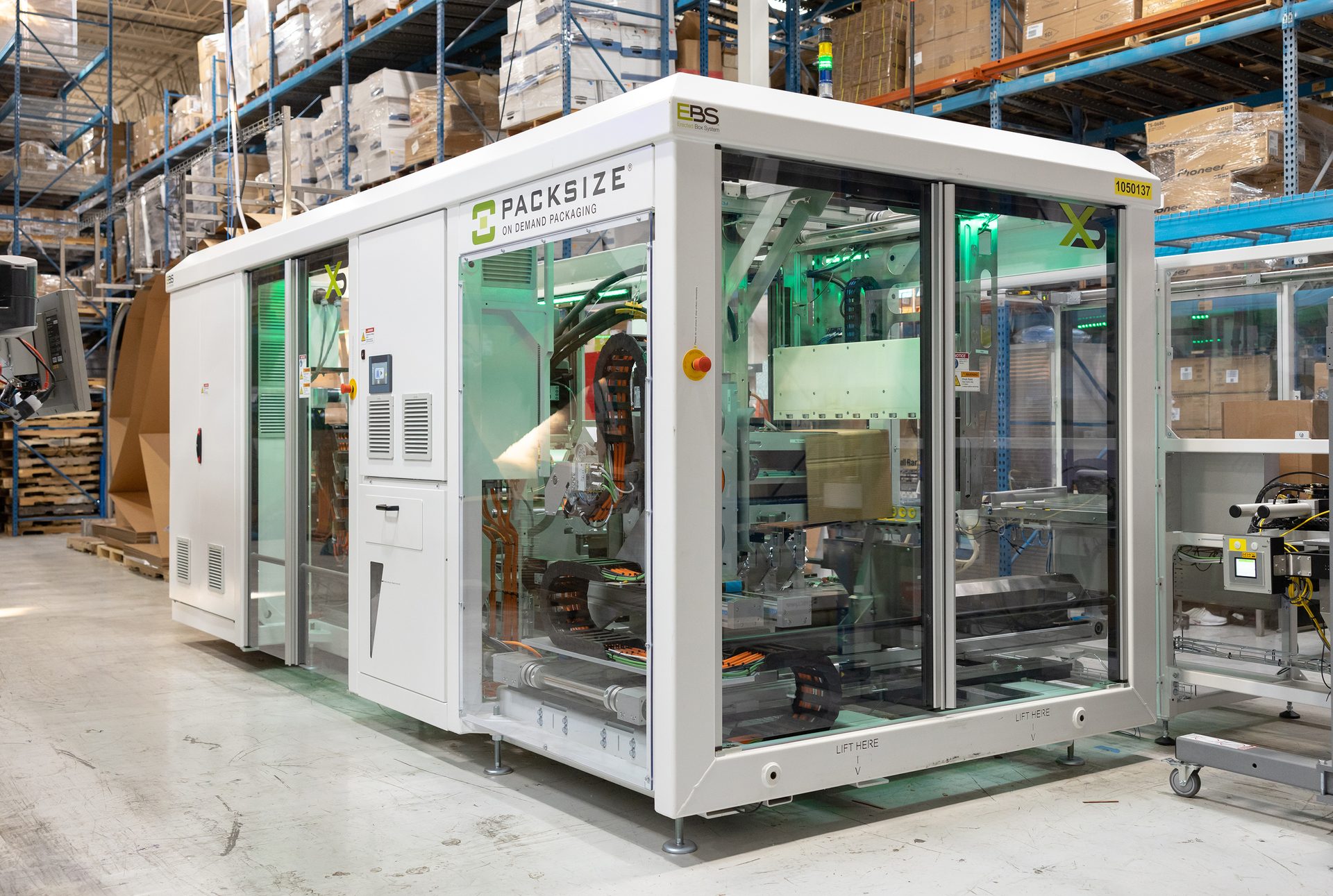

Small Footprints, High Speeds
These companies made headlines in 2023 for offering equipment with faster run rates and greater efficiency while taking up less floor space.
By Brad Addington
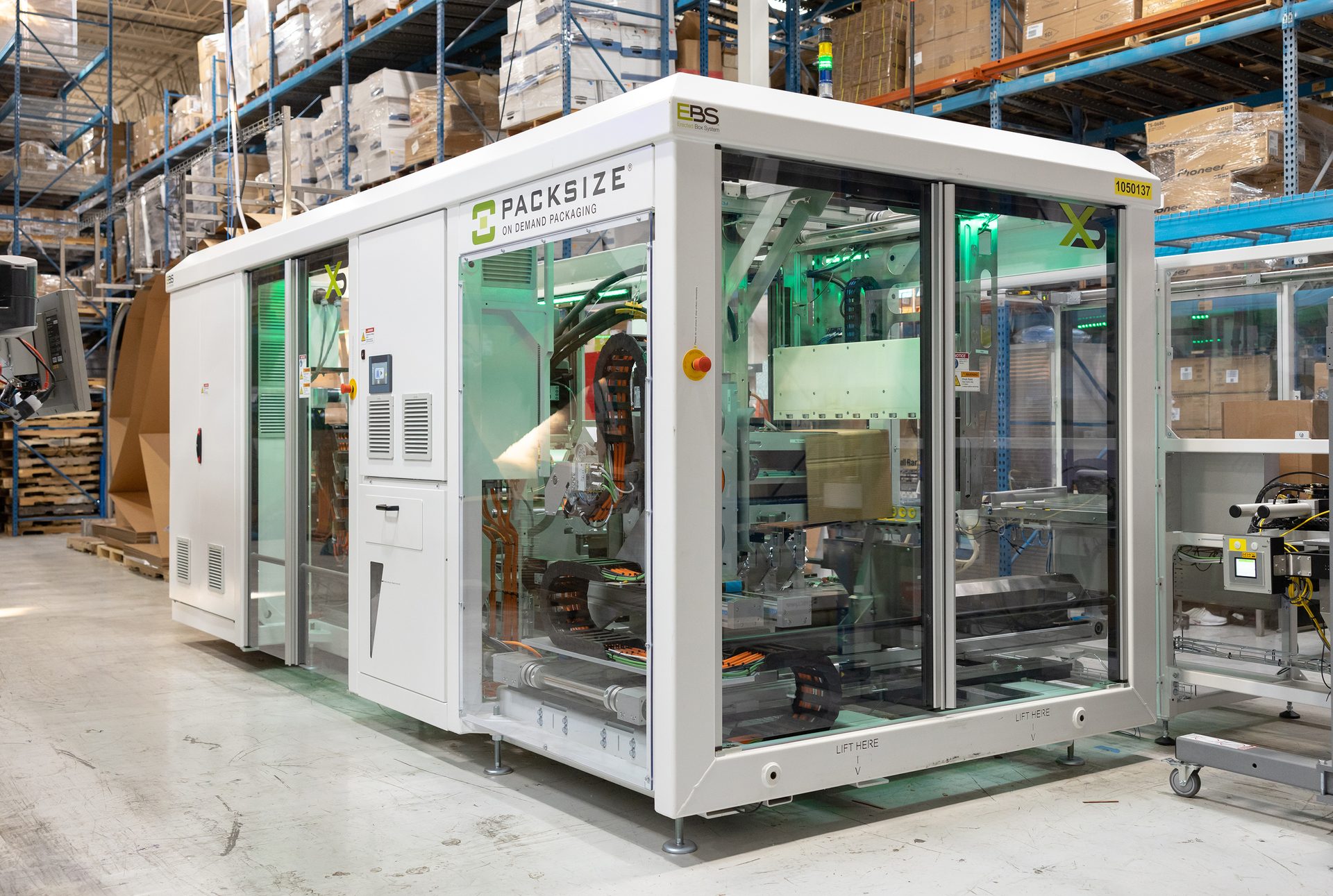
The Packsize X5, the world’s first fully-automated erected box system.
Courtesy of Packsize
Packaging equipment witnessed a plethora of innovations in 2023, and this definitely applies to case forming, packing and sealing.
Some of the innovations were award-winning. Packsize was nominated for – and was the recipient of – several awards for its X5® solution, which it touts as “the world’s first fully-automated erected box system” and “the most advanced, flexible, efficient and sustainable platform available for the e-commerce industry.”
In May, MGS announced the release of its new Matrix TL top-loading case packer. Ideal for packaging facilities with low-to-medium production rate requirements and diverse packaging requirements, the Matrix TL offers a complete form, fill and seal case packing solution with a small footprint, competitive rate of speed and quick changeovers.
Not to be outdone, Ishida Europe announced in September the launch of a new version of its ACP-700 series automatic case packing system (ACP) for snacks and other dry product packs, offering a fast, flexible and highly compact solution for a wide range of bag and case sizes and pack patterns.
The ACP-722 RRP offers one of the smallest footprints currently available, being up to 50% smaller than equivalent casepacker models.
Read more about these game-changing innovations!
Packsize's X5 Erected Box System Named Finalist for 2023 MHI Innovation Award
Packsize®, the market leader in sustainable, right-sized, on-demand packaging, announced in March that its new X5® solution is a finalist for the 2023 MHI Innovation Award for Best New Innovation. The X5 is the world’s first fully-automated erected box system and the most advanced, flexible, efficient and sustainable platform available for the e-commerce industry.
While the X5 ultimately was not chosen as the MHI winner, it was selected as a Materials Handling News 2023 Readers' Choice Product of the Year, and it was named 2023 Top Software & Tech by Food Logistics and Supply & Demand Chain Executive.
READ MORE
MHI is an international trade association representing the material handling, logistics and supply chain industries since 1945. The association sponsors the ProMat expo to showcase its member companies' products and services and educate manufacturing and supply chain professionals. The MHI Innovation Award highlights the latest manufacturing and supply chain products and services.
“We are truly honored to be recognized by MHI for our newly launched X5 solution,” said Rod Gallaway, CEO of Packsize. “Our innovations with the X5 enable manufacturers to navigate various challenges concerning packaging, labor and customer demand, and environmental impact mitigate while providing increased throughput by automating previously time-consuming processes. We are thankful for the opportunity to share these benefits with our industry colleagues at ProMat. We strive to support them in achieving their sustainability goals and business objectives with our efficient, industry-leading, right-sized packaging solution.”
The Packsize X5 solution produces ready-to-pack, right-sized erected boxes at an industry-leading speed of up to 600 boxes per hour. The new X5 machine significantly enhances e-commerce providers’ and manufacturers’ ability to meet customer demand, while addressing labor shortages, associated costs, and waste concerns. Like all Packsize solutions, the X5 reduces packaging waste caused by boxes that are, on average, 40 percent oversized. Right-sizing boxes also eliminates the need for void fillers like plastic air pillows, reduces shipping emissions, and improves the end-consumer's overall experience by providing a perfectly sized box, every time. In addition, companies can minimize their costs and environmental impact associated with extraneous and unneeded corrugated boxes and filler, while improving parcel logistics, fitting 66% more boxes on freight and delivery carrier vehicles.
On March 20, finalists will present their unique solutions to a panel of independent judges at ProMat 2023 in Chicago. MHI will announce the winners on March 22.
To learn more about Packsize, please visit packsize.com.
The Packsize X5 solution produces ready-to-pack, right-sized erected boxes at an industry-leading speed of up to 600 boxes per hour.
Courtesy of Packsize
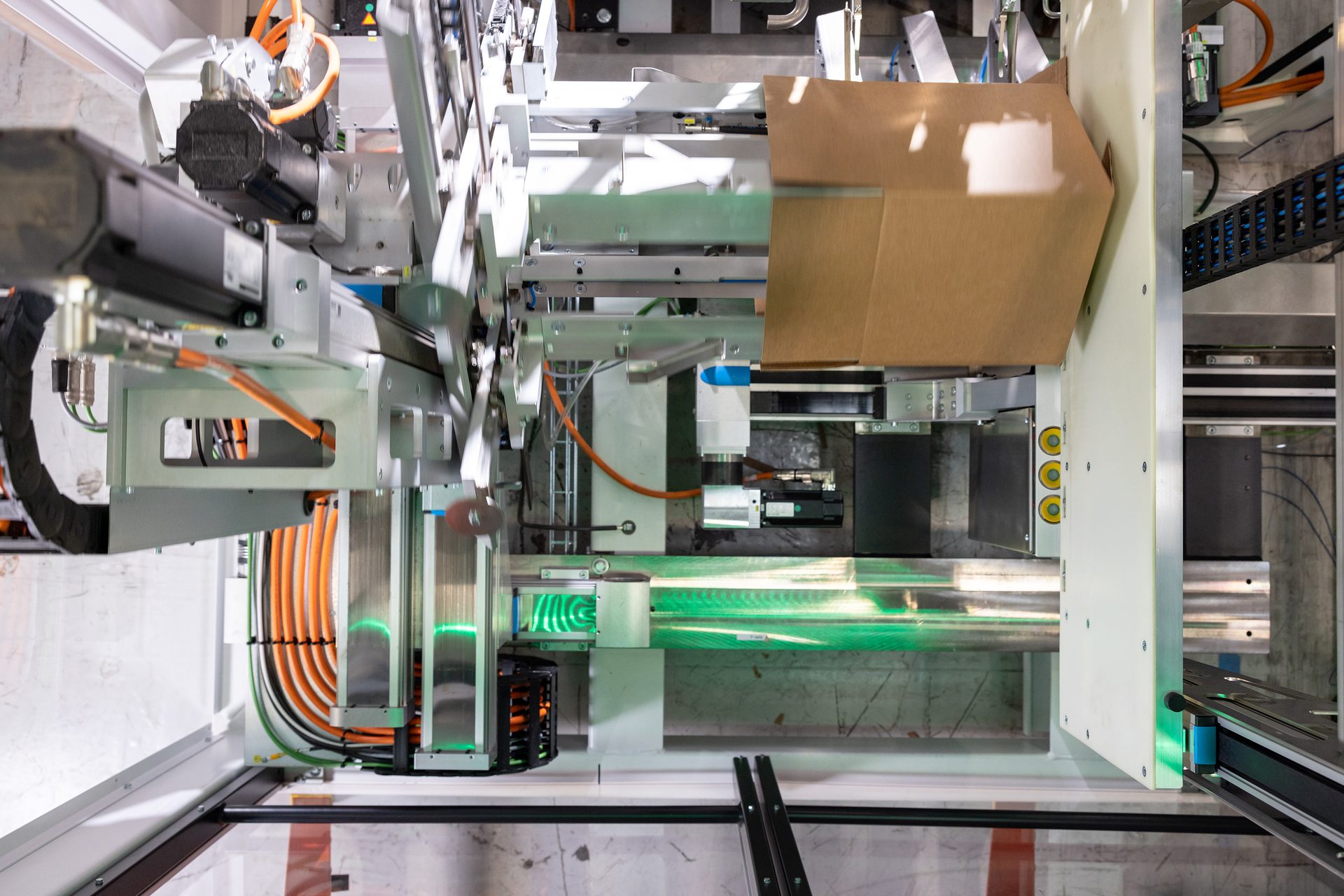
COLLAPSE ARTICLE ABOVE
MGS introduces compact top load case packer for diverse packaging requirements
MGS, a global leader in packaging automation solutions, announced in May the release of its new Matrix TL top-loading case packer. For packaging facilities with low-to-medium production rate requirements and diverse packaging requirements, the Matrix TL offers a complete form, fill and seal case packing solution with a small footprint, competitive rate of speed and quick changeovers.
Market demand for variety and more sustainable formats is challenging manufacturers, with the proliferation of stock keeping units (SKUs), product types and packaging configurations – from specialty and seasonal packaging to different case sizes and formats for wholesalers or convenience stores. Satisfying such a wide array of consumer and retailer demands means frequent equipment changeovers to accommodate different packaging runs and having a large quantity of products and materials at hand, which take up valuable facility space.
The Matrix TL case packer easily handles the unique specifications of diverse packaging runs with speed and efficiency. It offers an effective solution for a large range of applications and product types, including Home Care, Personal Care, Pharma and Med Device, and works as a secondary packaging solution for Food and Beverage products like bottled or canned foods and drinks.
READ MORE
“There are already small case packers that produce 10 cases per minute or fewer and big packers that can churn out 25 cases or more that are more suitable for high-volume, low-cost Consumer Goods,” says AJ Lee, Sales Director, Pharmaceutical and Medical Device Automation, MGS. “The Matrix TL hits that sweet spot in between, delivering strong production rates of 15-20 cases per minute in a small footprint — the base machine is just over 4 meters long.”
In addition to competitive run speeds for these kinds of applications, the Matrix TL also efficiently transitions between package types and formats. Changeovers can be accomplished in as little as 15 minutes through features such as:
- Drop-in tooling for easy format changes
- Customized pick head tooling that is simply swapped out for product changes
- Precise packing recipe selections
As its name indicates, the Matrix TL is a top-loading machine, which makes it especially valuable for today’s packaging operations looking to accommodate sustainability and variability. Top loading is an increasingly popular solution for packers because it allows for easier arrangement within the case, particularly for packages like flexible pouches that can be complex to load.
This handling and loading flexibility enables the Matrix TL to accommodate various product packing orientations for presentation purposes and allows for sustainable materials like paper trays to be placed in the case. The top load configuration can also help production lines reduce the amount of packaging used, such as loading bottles directly into cases without first putting them in a separate carton.
MGS is part of Coesia, a global group of companies offering solutions to automate a broad range of packaging operations across a variety of industries. The Matrix TL can be integrated with upstream equipment from other Coesia companies as part of comprehensive automated packaging solutions. Users of the Matrix TL can also use Coesia Digital software tools such as OptiMate, a human machine interface (HMI) with connectivity and smart functionalities to optimize equipment quality and performance, and PerforMate, an integrated internet of things (IoT) platform for real-time monitoring of individual machines and total systems.
MGS announced in May the release of its new Matrix TL top-loading case packer.
Courtesy of Packsize
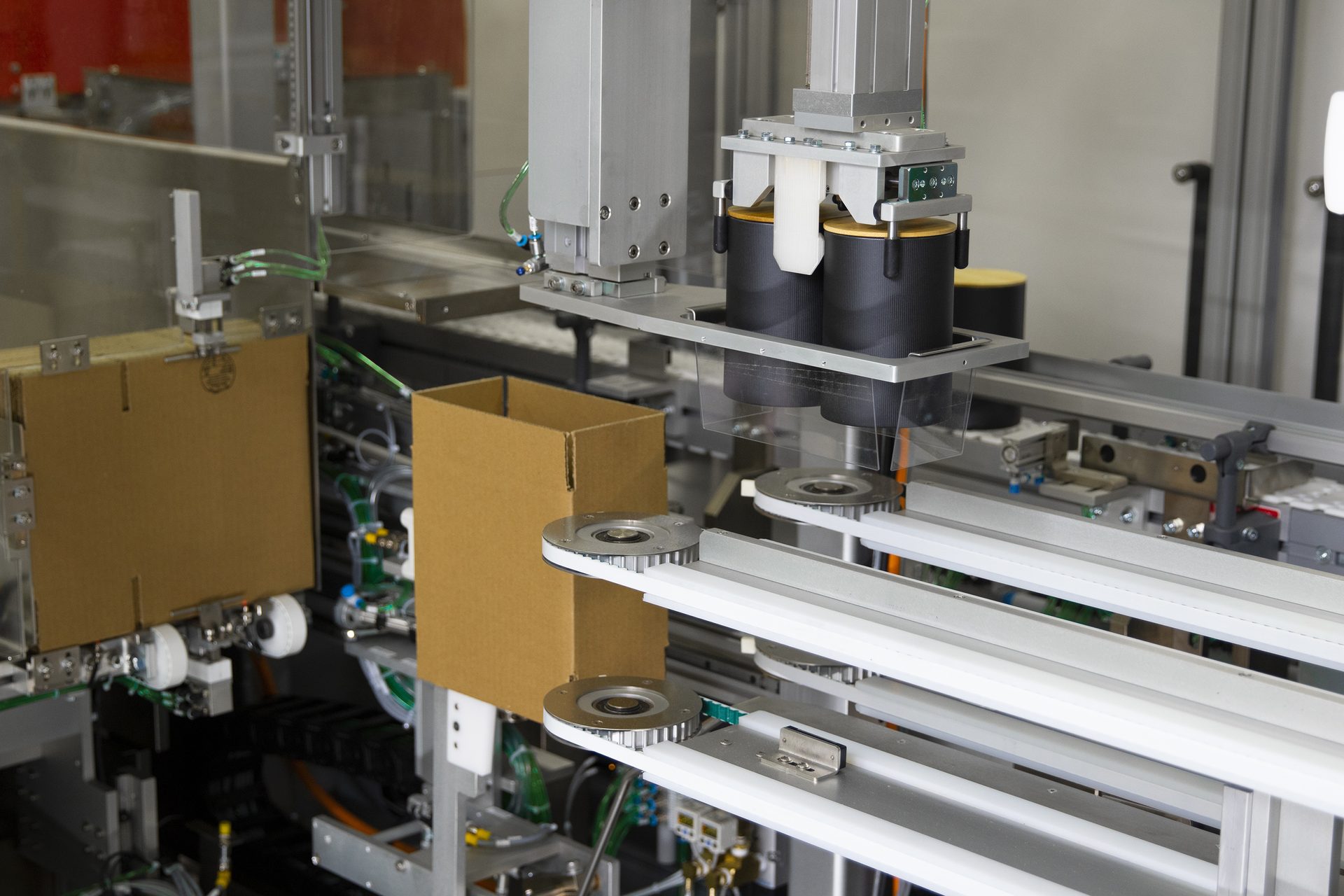
COLLAPSE ARTICLE ABOVE
Ishida Europe Releases New Version of Automatic Case Packing System
Ishida Europe announced in September the launch of a new version of its ACP-700 series automatic case packing system (ACP) for snacks and other dry product packs, offering a fast, flexible and highly compact solution for a wide range of bag and case sizes and pack patterns.
The ACP-722 RRP offers one of the smallest footprints currently available, being up to 50% smaller than equivalent casepacker models. As well as saving valuable factory space, this also allows quick and easy installation and seamless integration into existing production lines. The single directional flow design produces a lean and compact line layout which can also easily accommodate twin lines. Top speed is 20 cases per minute.
Key to the machine’s small size is the combination of case infeed and alignment, bag sorting and packing as well as case closing and sealing in one single compact unit, removing the need for additional conveyors. This also means that all functions can be controlled from one HMI touch screen. Product changeover is initiated at the touch of a button. This process is completely automatic and performed in under three minutes, without requiring a skilled technician.
READ MORE
The advanced HMI touch screen displays easy-to-use intuitive menus for machine set-up and monitoring. It allows the storing of up to 500 pre-sets, including photos of each pack format to minimize operator errors and can also alert operators to potential upstream issues, enabling them to take immediate action to minimize waste and unscheduled downtime.
The ACP-722 RRP can form part of a fully integrated snacks packing line, manufactured by Ishida, comprising of a multihead weigher, bagmaker, seal tester, checkweigher, X-ray inspection system and casepacker. Utilizing Ishida’s ITPS 2 software, set up and adjustment for the entire line can take place anywhere on the line from a single HMI screen.
As part of the integrated line, the ACP-722 RRP receives upstream pack air-fill data from the Ishida seal tester, enabling immediate adjustments to be made to ensure continuous and reliable high-speed packing, regardless of the operator skill set level.
In-line monitoring counts packs to ensure the correct number is delivered into every case.
The ACP-700 series of case packers is capable of handling bags between 108 and 330mm in width and up to 375mm in length with many different bag types including pillow, side gusset, flat bottom and HEM. These can be packed into various configurations and orientations, including retail ready display cases, without the need to change machine parts. In addition to tape sealing, side lock and push lock case closing options are also available.
“The snacks market remains highly competitive, and companies therefore need to maximize efficiencies in every part of their operations,” said Jim McGregor, Applications Engineer at Ishida Europe. “The ACP-722 RRP has been designed to ensure fast throughput without compromising on pack quality and presentation, delivering maximum return from a minimum footprint.”
To learn more about Ishida Europe, please visit ishida.com.
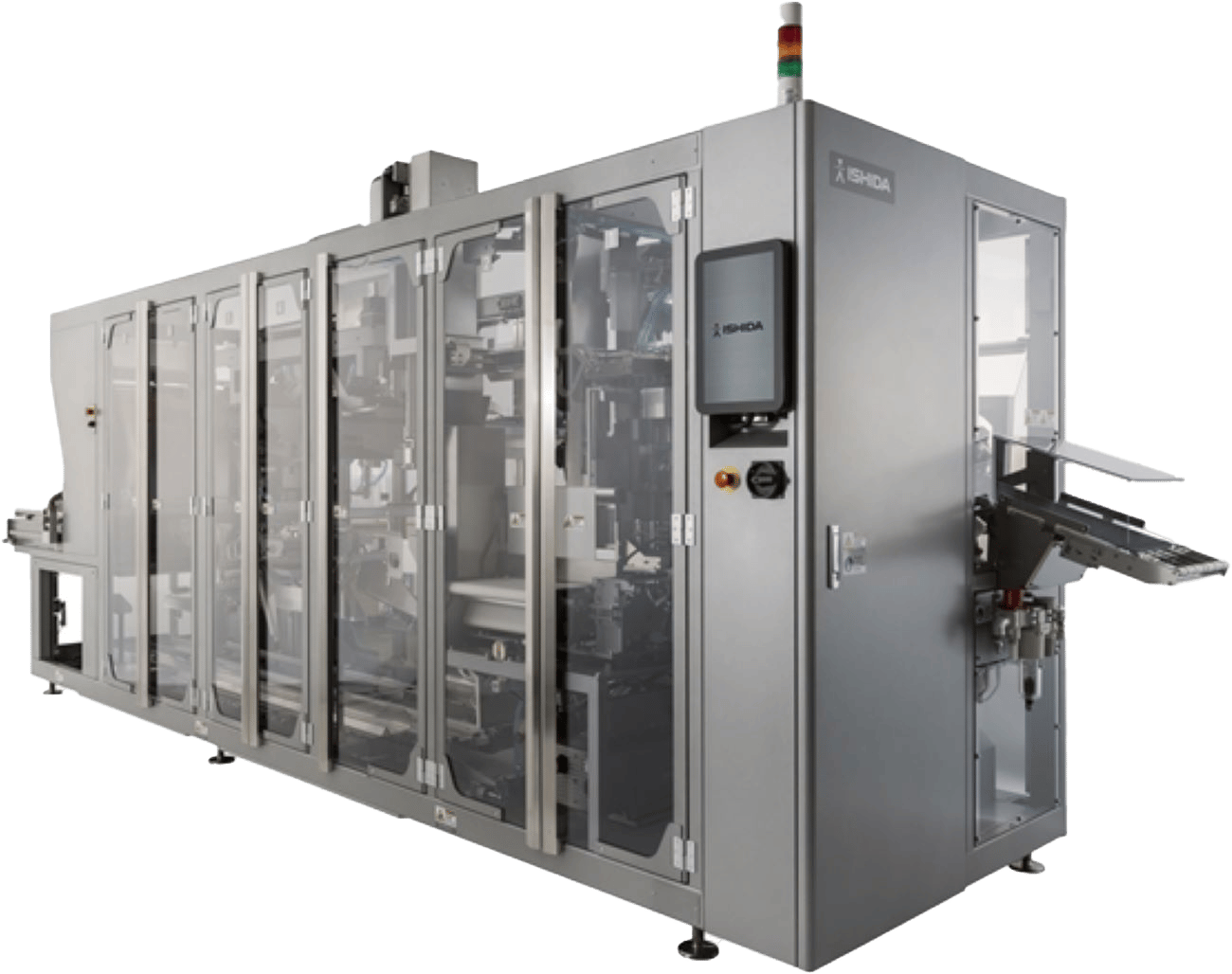