
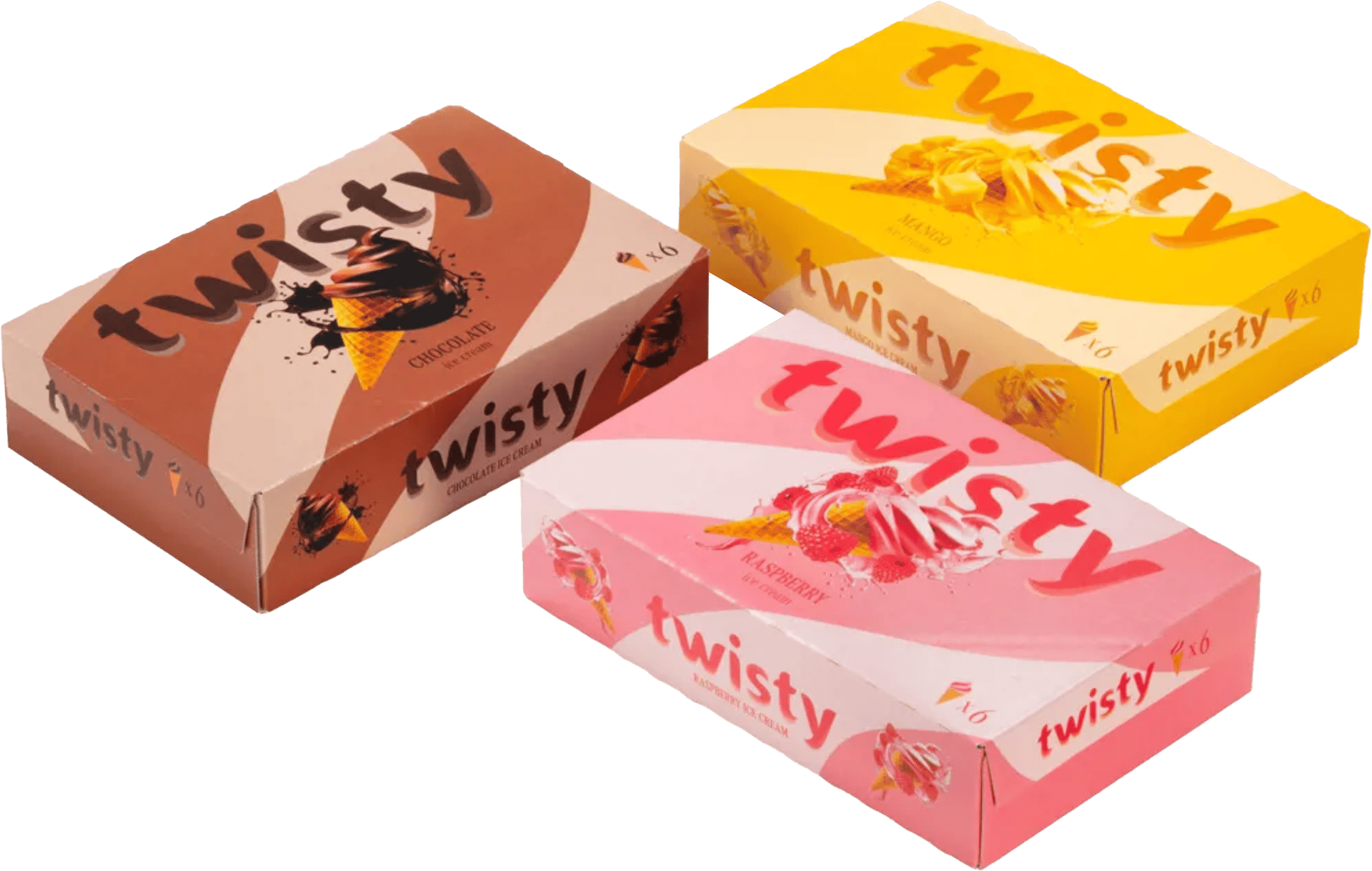
Advancements in Paperboard and Corrugated Packaging
Paperboard, corrugated, and carton packaging has continued to see growth when it comes to improved technology and sustainability.
By Bobby Douglas
As the packaging industry continues to see drastic improvements when it comes to sustainability and technology, paperboard, corrugated and carton solutions have been a key area of focus for manufacturers due to their dependability and ease of use. This focus has resulted in key innovations when it comes to environmental responsibility and design investments.
DS Smith’s box plant in South Carolina recently reduced its CO2 emissions thanks to a new steam recycling system.
Meanwhile, Metsä Board developed more sustainable fiber-based packaging for ice cream cones, in addition to minimizing ink usage.
TetraPak and Lactogal collaborated to create an eco-friendly aseptic milk carton made from 90% renewable materials.
And finally, Pacificolor made a significant investment with the help of Reproflex3 to bolster its corrugated graphics capabilities.
Learn more about these developments below.
Metsä Board’s new packaging for ice cream cones.
Courtesy of Metsä Board
DS Smith Box Plant Shrinks CO2 Emissions with Steam System
DS Smith, a leading provider of sustainable, fiber-based packaging worldwide, recently completed the installation of new steam recycling technology that will reduce energy consumption by 20% in its Columbia, South Carolina, corrugated packaging facility. This investment is part of DS Smith’s ambitious sustainability commitments to its North American customers.
The new multi-million-dollar Baviera Steam Systems technology installed at the specialty coated box manufacturing plant efficiently recovers condensate typically lost in the corrugation process. Energy savings created through condensate recovery reduces DS Smith’s carbon footprint in Columbia, and the new technology also increases productivity by reducing maintenance downtime at the plant.
“Our South Carolina facility makes water-resistant, fully recyclable Greencoat® boxes for fresh poultry and produce providers – agribusinesses that recognize decarbonization as a key factor to their continued success,” said Steven Rose, Managing Director, Packaging, for DS Smith North America Packaging and Paper (NAPP). “With this investment, we are decreasing the amount of natural gas consumed at the facility by 20%, substantially reducing CO2 emissions while also enabling faster throughput.”
READ MORE
Reducing natural gas usage at the DS Smith NAPP Columbia box plant will yield an estimated 740-ton decrease in annual CO2 emissions. Decarbonization at this scale is one of several initiatives in North America and Europe driven by DS Smith’s Now and Next sustainability strategy, which aims to reduce emissions by 46% in absolute terms by 2030, compared with 2019 levels, and achieve net zero emissions by 2050.
The company, which is a member of the United Nations-led Race to Zero campaign, also participates in the Science Based Targets initiative (SBTi) and has set a 1.5°C target in line with the goals of the Paris Agreement.
Greater manufacturing flexibility and productivity
The new installation at the Columbia box plant includes Baviera Steam Systems’ Condensate Recovery Unit along with Digital Steam Pumps from Baviera capable of managing the pressure required for corrugation using lightweight and heavyweight papers. Continuous heat transfer control solutions installed with the steam system help to ensure greater consistency, improving control room management and eliminating the need for operator tweaks that can impact long-term performance.
The new technologies also reduce downtime needed to adjust steam pressure when changing paper weights or fluting settings, boosting overall volume capacity at the plant by up to 5%. Faster, simplified changes between board grades with the upgrade will also reduce manufacturing waste.
Driving circularity with coated boxes
The Columbia box plant produces corrugated shipping containers made from DS Smith’s propriety Greencoat material: a 100% recyclable coated and food contact safe alternative to non-recyclable wax-coated boxes. Industrial businesses in the fresh poultry, produce and seafood industries rely on this sustainable wax alternative product for safe and leak-proof shipping of their products across the U.S. and worldwide.
Greencoat boxes cost less than wax-coated boxes, and users do not have to pay fees charged for wax-coated box disposal. Instead, industrial food processors can sell their used Greencoat boxes to recycling facilities.
DS Smith NAPP’s Columbia plant also uses Greencoat to produce GreenTote™ boxes, a 100% recyclable alternative to plastic grocery bags used in supermarkets, and GreenChute™, a 100% recyclable yard waste bag filler. Greencoat products are examples of how DS Smith is continuing to deliver on its purpose of Redefining Packaging for a Changing World, supporting the transition to a circular economy and eliminating waste and pollution by design.
The Baviera Steam Systems technology helps DS Smith reduce energy consumption.
Courtesy of DS Smith
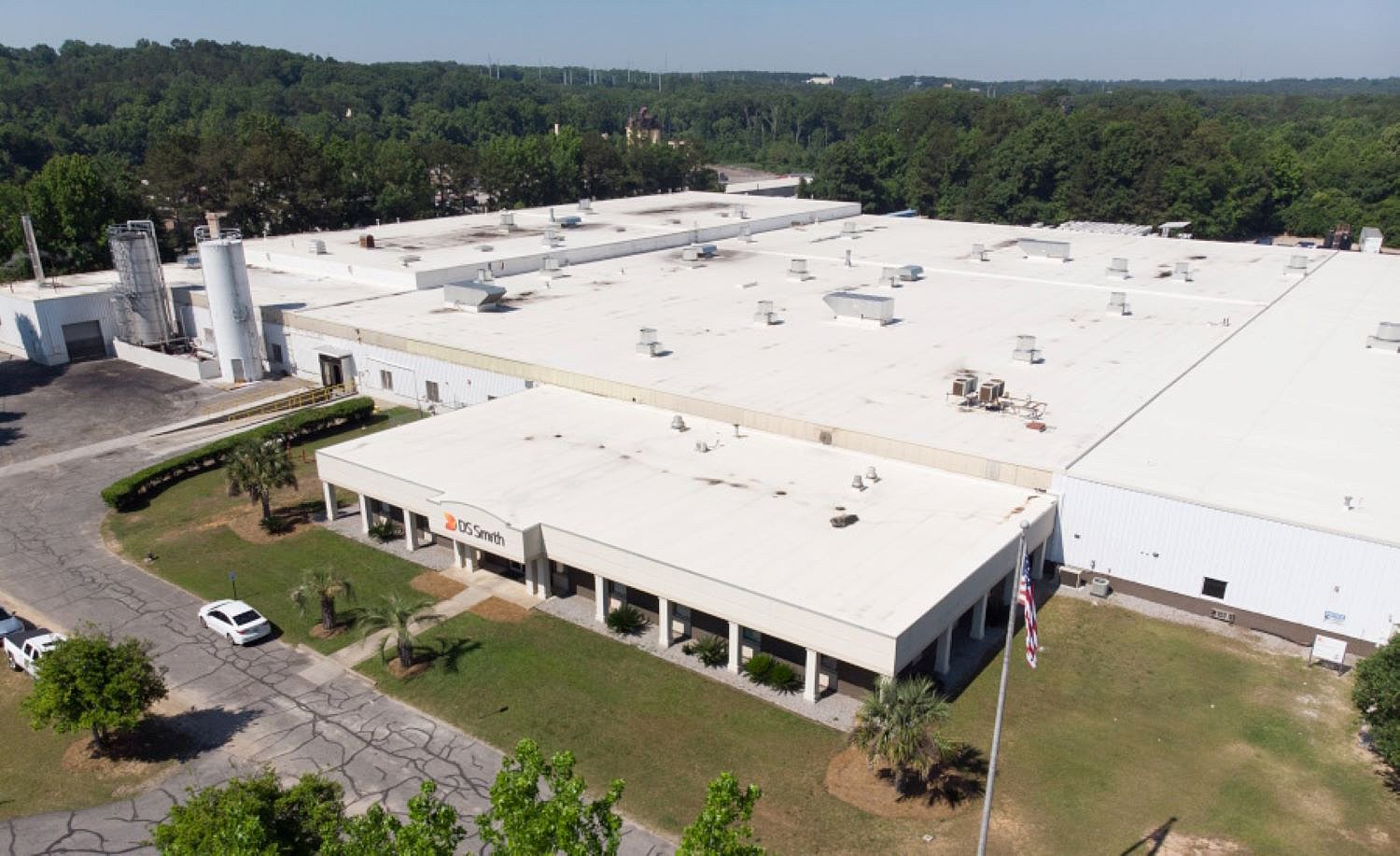
COLLAPSE ARTICLE ABOVE
Metsä Board Partners with Industry Leaders to Develop Sustainable Ice Cream Cone Packaging
Metsä Board collaborated with industry leaders to re-design a favorite of the frozen food aisle: ice cream cone packaging. The team looked into different stages of the value chain, ranging from material production, to ink usage and logistics. The result is a packaging with a significantly lower climate impact.
The team of design, printing and converting experts first analyzed frozen food packaging to identify areas of improvement. These solutions traditionally rely on recycled fibers and spot color printing. With this project, the team wanted to showcase new possibilities using carefully selected lightweight fresh fiber materials and flexographic printing methods to achieve excellent usability and unparalleled halftone graphics with less impact on the climate.
Metsä Board’s double coated white-top kraftliner (MetsäBoard Prime WKL, 125 g/m2) was selected as the top liner for its lightweight and smooth surface that enables excellent reproduction of detailed visuals. The inside liner and fluting were made from uncoated kraftliner (MetsäBoard Natural WKL Bright 90 g/m2) which is ideal for small and lightweight packaging requiring high strength. Both materials are made from pure and traceable fresh wood fiber making the packaging easily recyclable or compostable and safe for food packaging. Having two layers from same material also simplified production without compromising quality.
READ MORE
Metsä Board’s Sustainability Services did detailed calculations of the paperboard materials comparing them to traditional white lined chipboards used in the European market. Due to the 8 percent lighter weight and use of fossil free energy that is generated as a by-product of Metsä’s chemical pulp production, the new packaging was found to have up to 36 percent lower climate impact (Cradle-to-Gate + End-of-Life).*
Packaging designers at Futupack paid special attention to the user experience by creating an easy-to-open design, eliminating the need for plastic parts or special tools for opening. Attention was also paid to minimizing ink usage, while keeping each variety recognizable. Process printing was selected as the printing method to eliminate the use of spot colors and enhance efficiency and flexibility.
Packaging manufacturer Adara Pakkaus, proposed 64 lpcm expanded color gamut (ECG) co-printing as a suitable method for the corrugated board. The flexo printing plates were supplied by Marvaco. By using the carefully selected kraftliner materials, the team was able to eliminate the ‘wash board effect’ common in corrugated boards.
”This high-resolution quality is unusual in such solutions; corrugated post print typically achieves lower accuracy,” says ECG printing specialist, Dr Kai Lankinen, who consulted on the project. “ECG benefits co-printing, consolidating designs, reducing waste, plates, energy, and press return inks.”
Adara’s Head of Printing Lari Seppälä noted the eco-efficiency of the project which included reviewing the entire process for selecting options to lower the environmental impacts. “With our new 7-color press and ECG tools we were able to reduce ink usage, simplify logistics and make the entire process flexible as well as cost-efficient.”
“This ice cream packaging project showcased again the power of seamless teamwork,” concludes Metsä Board’s Packaging Services Director, Ilkka Harju. “With the careful selection of materials, and pushing traditional boundaries of printing, we were able to combine excellent functionality and resource efficiency. Collaboration was crucial for understanding the requirements and capabilities in the different stages of the supply chain.”
The lightweight material and minimized ink usage makes these packages much more sustainable.
Courtesy of Metsä Board
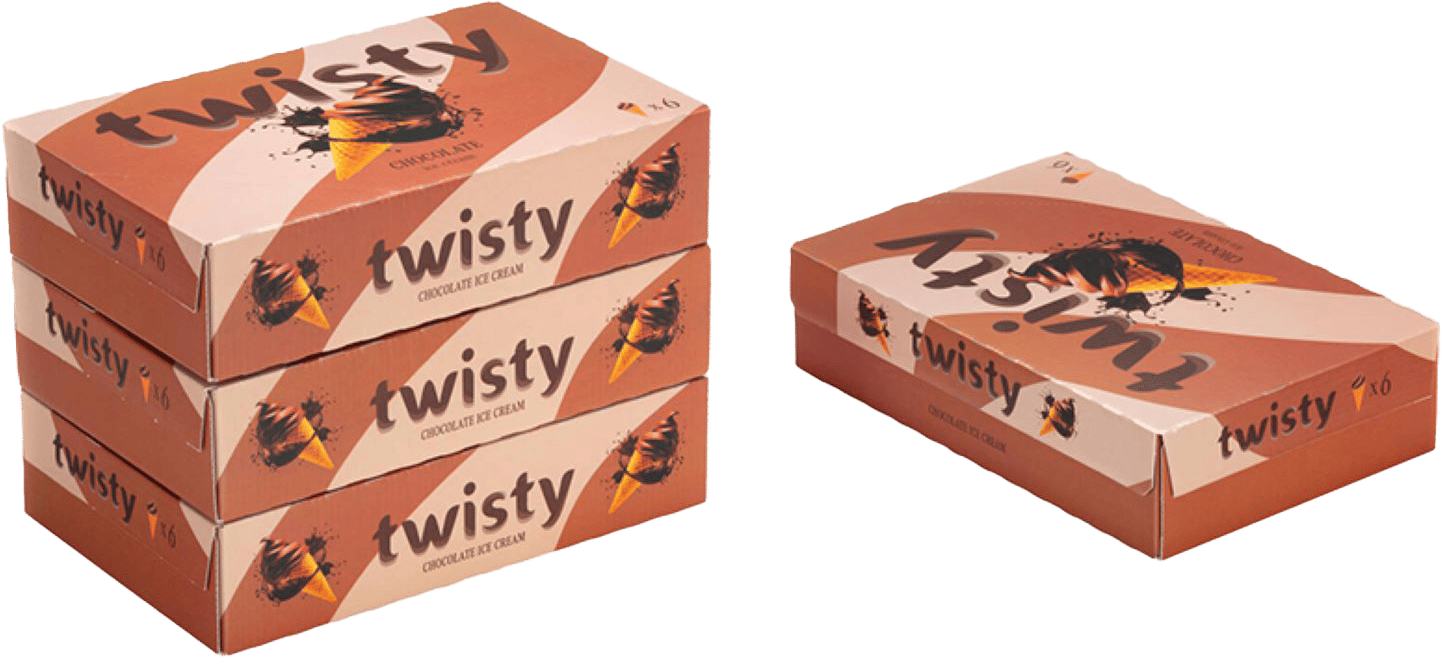
COLLAPSE ARTICLE ABOVE
Tetra Pak and Lactogal Reduce Carbon Footprint of Aseptic Milk Cartons
Following successful commercial consumer testing in 2022, Tetra Pak and Lactogal have now launched an aseptic beverage carton featuring a paper-based barrier.
This is part of a large-scale technology validation, involving around 25 million packages and currently ongoing in Portugal.
Made of approximately 80% paperboard, the package increases the renewable content to 90%, reduces its carbon footprint by one third (33%) and has been certified as Carbon Neutral by the Carbon Trust™.
READ MORE
Greenhouse gas emissions, food waste and plastic littering are cited as the top three environmental sustainability concerns facing food and beverage (F&B) businesses today, and this is expected to remain the case over the next five years. Packaging solutions like these — which expand the amount of paper and lower the carbon footprint, while ensuring food safety — can help the industry overcome these challenges.
In 2015, Tetra Pak was the first in the industry to introduce a package made fully from plant-based renewable materials — paperboard and sugarcane-based plastic. The Tetra Rex® Plant-based package, suitable for cold chain distribution, is fully renewable, and the company has delivered approximately 6.5 billion of these packages to customers around the world to date.
The launch of the Tetra Brik® Aseptic 200 Slim Leaf carton with paper-based barrier, together with Lactogal, provides a package that can be distributed under ambient conditions, while hitting the 90% renewable content mark. This brings Tetra Pak one step closer to its ambition of a beverage carton made solely from responsibly sourced renewable or recycled materials, fully recyclable and carbon neutral. The company is aiming for industrial scale production of the solution by 2025.
José Capela, President of Lactogal, comments: “Our collaboration with Tetra Pak centers on a shared belief that a more sustainable future is possible. Innovating together is a big part of that. We are both focused on an ambitious sustainability transformation, and this new carton’s 33% reduction in greenhouse gas emissions, together with its Carbon Neutral certification by the Carbon Trust™, is a significant achievement towards this goal.”
Ola Elmqvist, Executive Vice President Packaging Solutions, Tetra Pak, adds: “The development represents a critical marker in our longstanding work to design beverage cartons for recycling – something that is continuing to set the pace for the paperization of packaging. By joining forces with Lactogal, we’re now demonstrating that it’s possible to progress the sustainability of aseptic beverage cartons while securing food safety and enhancing food access.”
In 2022, together with its industry partners in the Alliance for Beverage Cartons and the Environment (ACE), Tetra Pak jointly adopted Design for Recyclability guidelines for beverage cartons, which provide technical guidance for optimized recycling of this type of packaging.
More recently, the 4evergreen alliance added beverage packaging design guidance to its fiber-based circularity toolset. 4evergreen is a cross-industry platform that aims to boost the contribution of fiber-based packaging in a circular and sustainable economy, with Tetra Pak among its founding members.
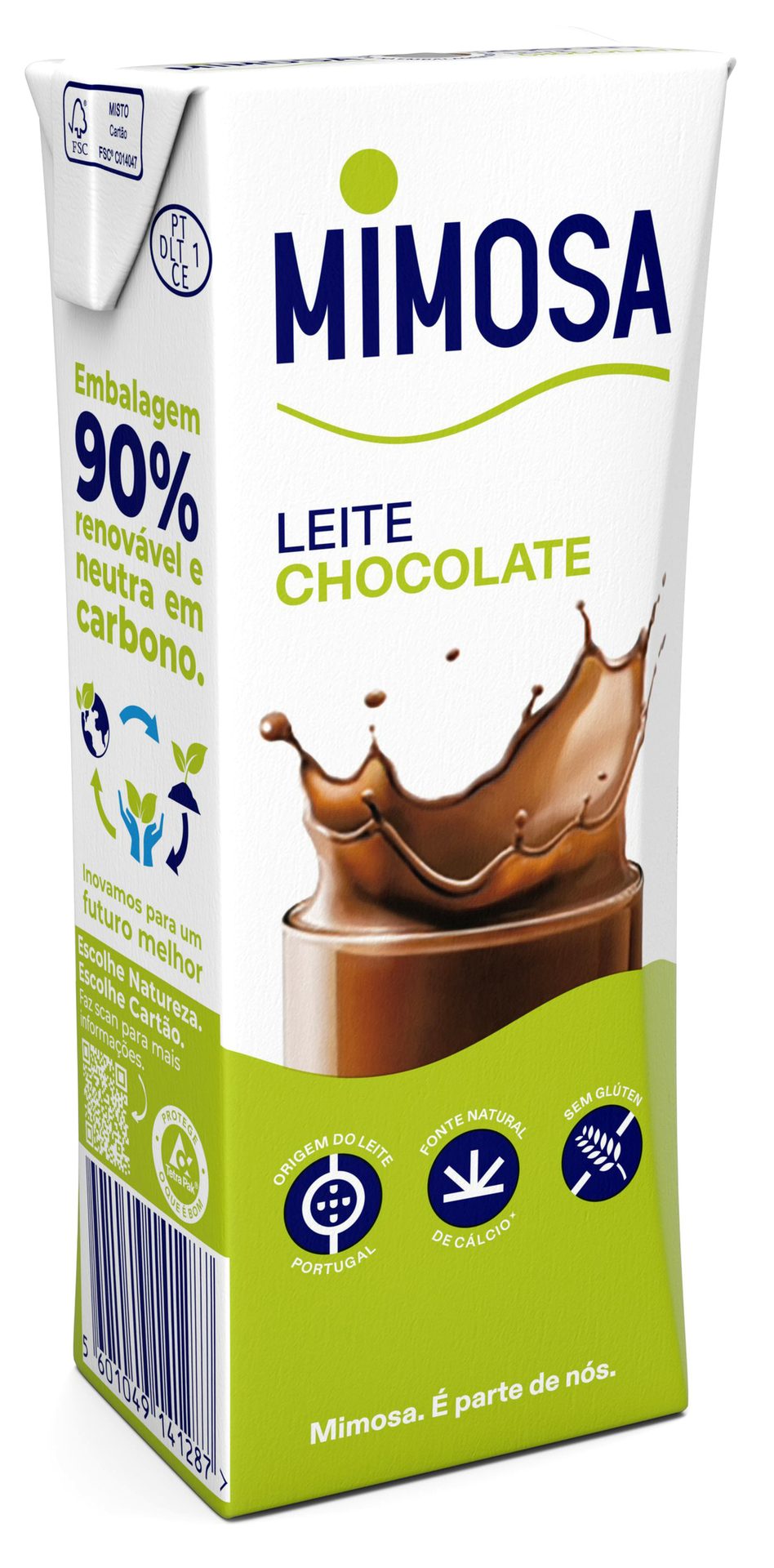
The new cartons resulted in a carbon footprint reduction of around 33%.
Courtesy of Tetra Pak
The new cartons resulted in a carbon footprint reduction of around 33%.
Courtesy of Tetra Pak
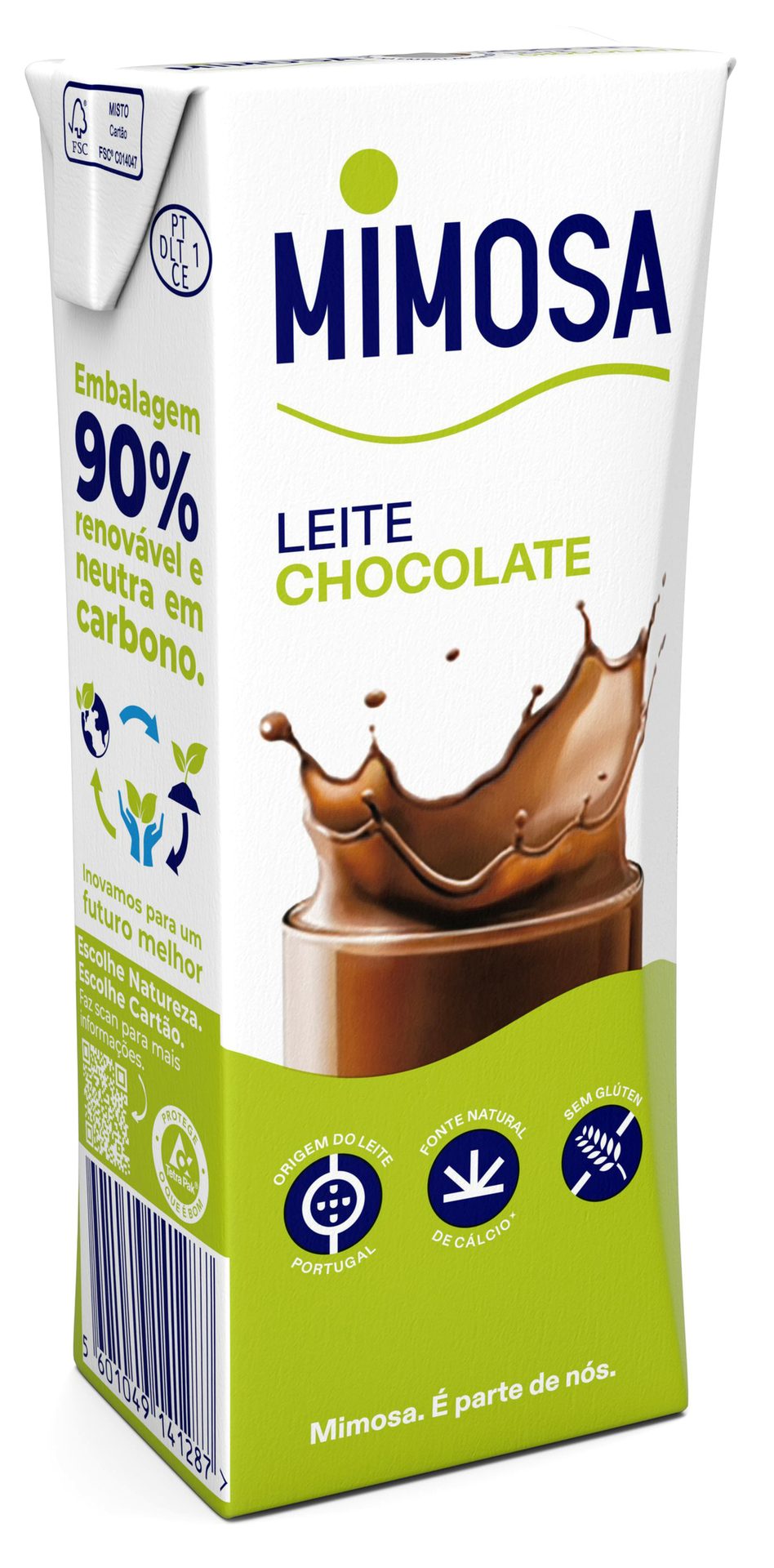
COLLAPSE ARTICLE ABOVE
Pacificolor Clients Stand to Gain from Company’s New Corrugated Graphics Equipment
Pacificolor LLC, a leading name in the corrugated packaging industry in North America, has announced a significant investment of more than $200,000 in state-of-the-art equipment to enhance its production of high-quality corrugated graphics.
The investment includes the acquisition of an AV Flexologic Corrugated Flat Mounting Machine and the integration of Reproflex3's high-definition Vortex™ screening technology.
Vortex seamlessly integrates within existing print set-ups to optimize processes and deliver fast, efficient, precision printing. The technology has been created for ink on paper, corrugated board and film. It uses a unique set of tools to stabilize the flexographic print process to create superior print consistently and cost effectively.
READ MORE
This latest strategic investment allows Pacificolor to expand its capabilities in corrugated plate making, offering greater sizes, faster throughput, and accelerated turnarounds for clients.
The new equipment not only enhances the company's production efficiency but also brings about several advancements in corrugated workflow.
The AV Flexologic Corrugated Flat Mounting Machine introduces improved soft proofing capabilities and seamless integration with Pacificolor's digital front-end architecture. This, in turn, opens the door to innovative services designed to simplify the lives of Pacificolor clients.
The investment is poised to set a new standard in the industry by delivering cutting-edge solutions tailored to meet the exacting needs of converters and brand owners.
Nick Brunk, chief revenue officer at Pacificolor, expressed enthusiasm about the partnership with AV Flexologic, stating: "Our collaboration with AV Flexologic has been a cornerstone of our success. The synergy between our companies is set to go beyond the current scope, offering a range of new solutions for corrugated professionals in the box making and POP industries.”
“The combination of the AV Flexo mounter with Vortex, the multi-award-winning print technology created by our global technical partner Reproflex3, will revolutionize sustainable printing solutions for corrugated packaging, delivering numerous advantages to cater to the evolving needs of converters and brand owners alike."
This significant investment reflects Pacificolor's commitment to staying at the forefront of technological advancements in the corrugated packaging industry. The company anticipates that the integration of AV Flexologic and Reproflex3 technologies will not only elevate its own production capabilities but also contribute to advancing the industry as a whole.
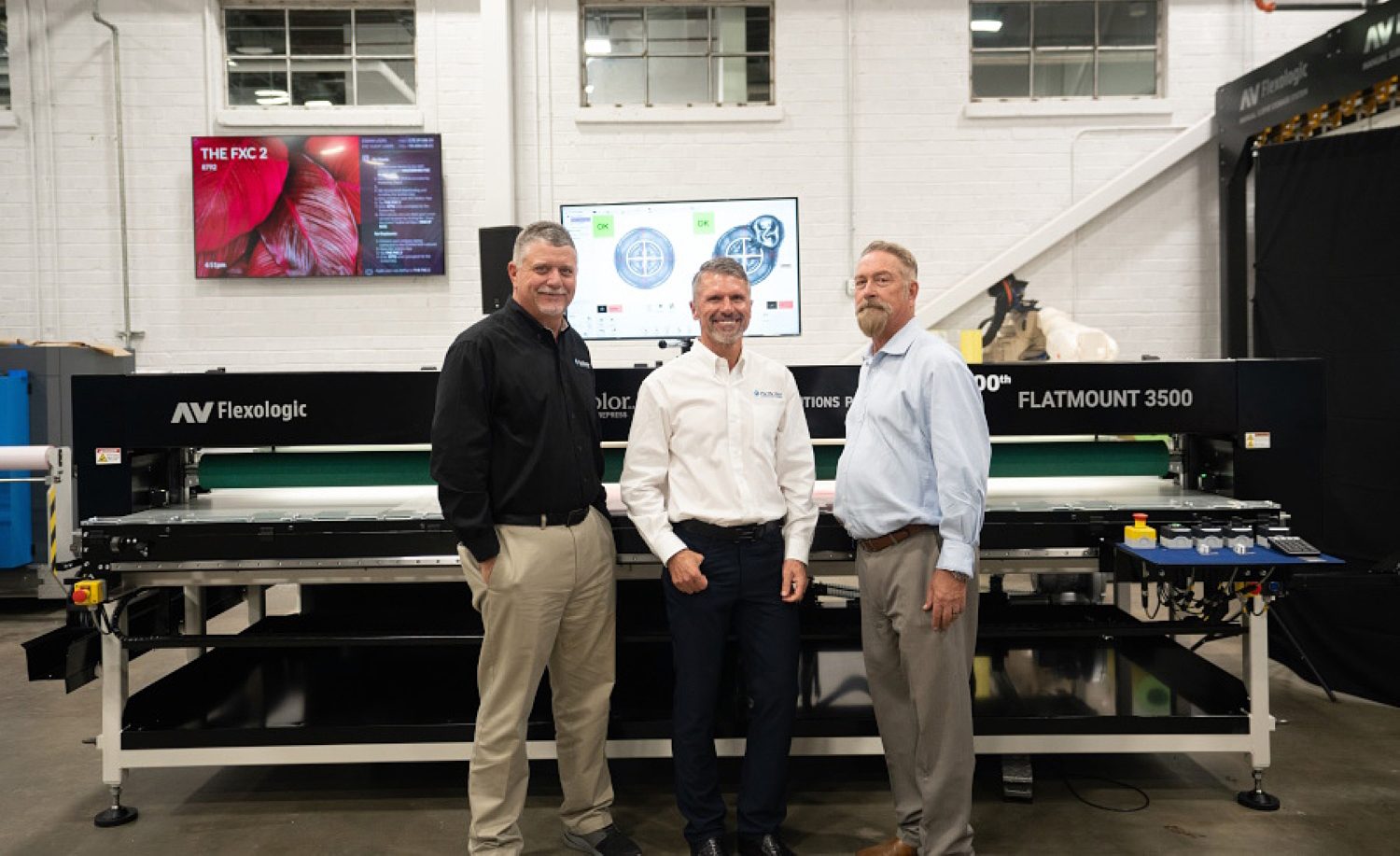