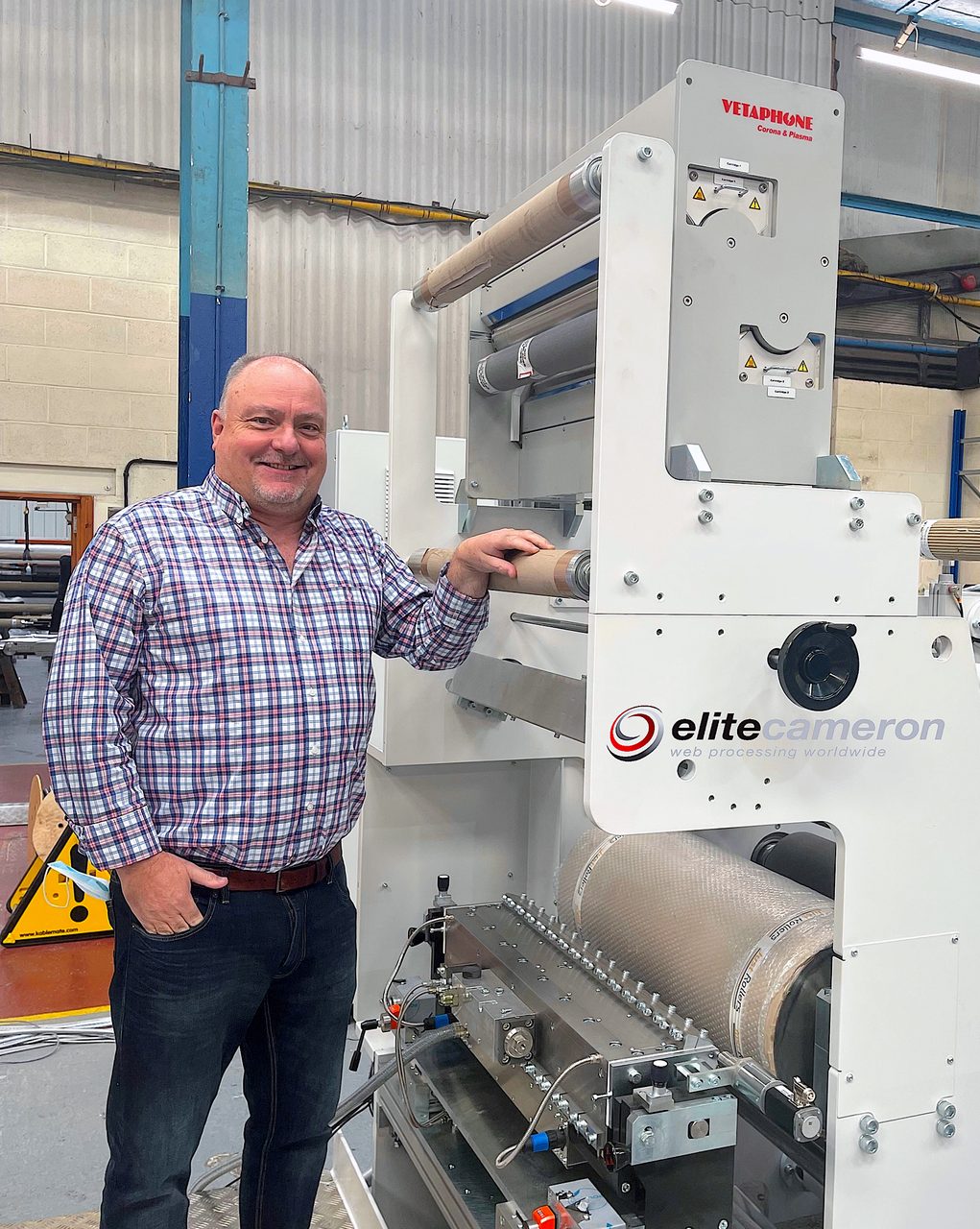
INDUSTRY TRENDS
Innovative Consulting Services for Printers and Converters Solve Workforce Issues
Many converters and printers made software investments before the pandemic, and now third-party solutions are aiding companies as they try to meet increased demand.
By Grant Gerke
The push for increased throughputs by converters, printers and co-packers has been a theme for the last two years as the pandemic and supply chain challenges have pushed companies to their production limits. Demand for operators and experienced personnel is at an all-time high and training new workers is challenging, so many companies are looking at flexible packaging consultants or integrators to do some heavy lifting.
ADVERTISEMENT
One example of this is Anderson and Vreeland (A&V) in Fairfield, N.J., and its inventory management solutions for Bison Bag Company in Lockport, N.Y. Bison is a flexible packaging converting company with a 95,000-sq-ft plant that has many different departments, including ink rooms, equipment areas and a large warehouse. Inventory includes mounting tapes, end seals, doctor blades and other consumable flexible packaging supplies.
In September 2021, Anderson and Vreeland added an RFID-based, automated inventory management system for Bison, called VMI or Vendor Managed Inventory system. “We used to have to do inventory management manually by printing lists of all the items that we get, checking everything weekly and emailing A&V with a list of what we lack,” says Stephen Mead, printing supervisor at Bison Bag.
The VMI or Vendor Managed Inventory system comes in many shapes and sizes, but for Bison it tracks inventory needs based on the data collected through the RFID tags. And then a RFID reporting module shows real-time inventory status for Bison employees.
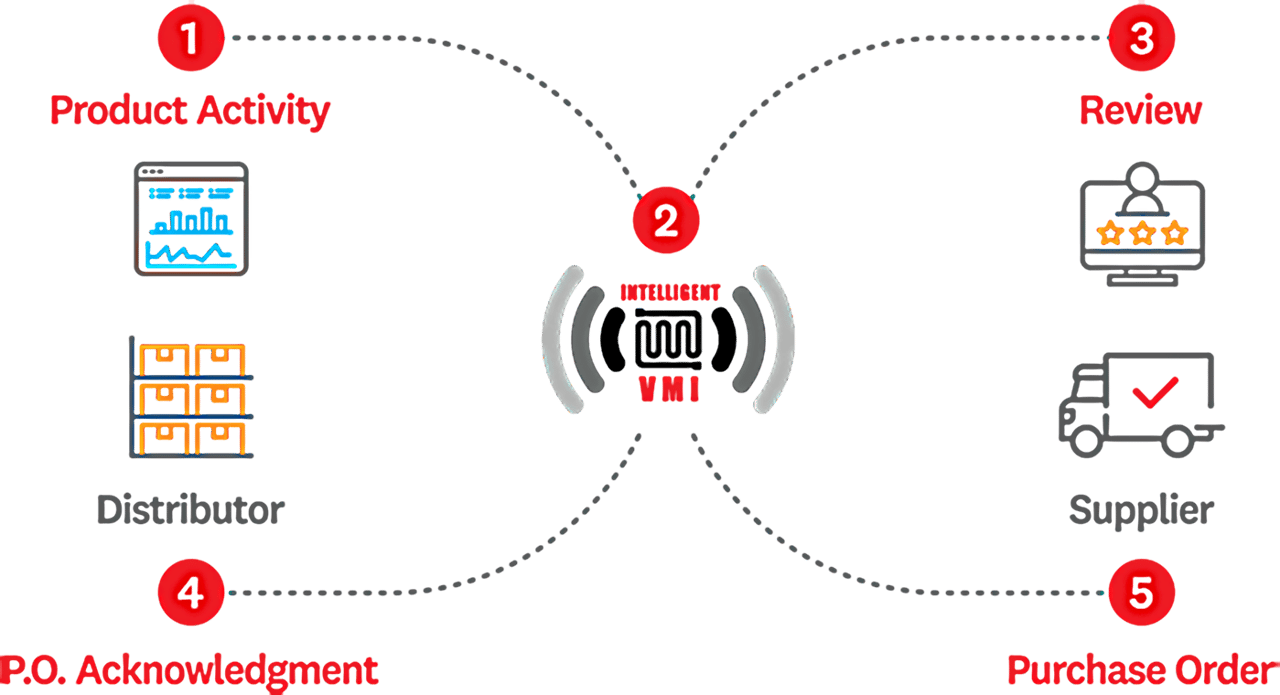
The software reads the RFID tags continuously to provide real-time inventory analysis.
Image courtesy of Anderson & Vreeland
Anderson & Vreeland helps Bison manage the VMI RFID by providing account managers, customer and warehouse teams. “With the RFID solution, Anderson and Vreeland automatically run a report and see what I need based on how much inventory we have on hand,” says Mead.
The VMI system uses a supply cabinet outfitted with RFID sensors that communicate with an inventory system, continually monitoring the amount of supplies available. The software reads the tags several times per day, adding the data to a history file. This lets you track usage of the consumables in the cabinet on a daily, weekly and monthly basis. Users are able to see and adjust the minimum and maximum quantities of each item, letting the company and Anderson & Vreeland know when items need replenishing.
Lab Research and Development
Tim Self, president of TS Converting Equipment in the UK, has been offering converting knowledge to his customers for more than 30 years and a range of Elite Cameron slitter rewinder, coating and laminating machines. TS employs 35 full-time staff and subcontractors, and generates approximately £10 million in sales for a business that specializes in the design and manufacturing of bespoke converting system solutions.
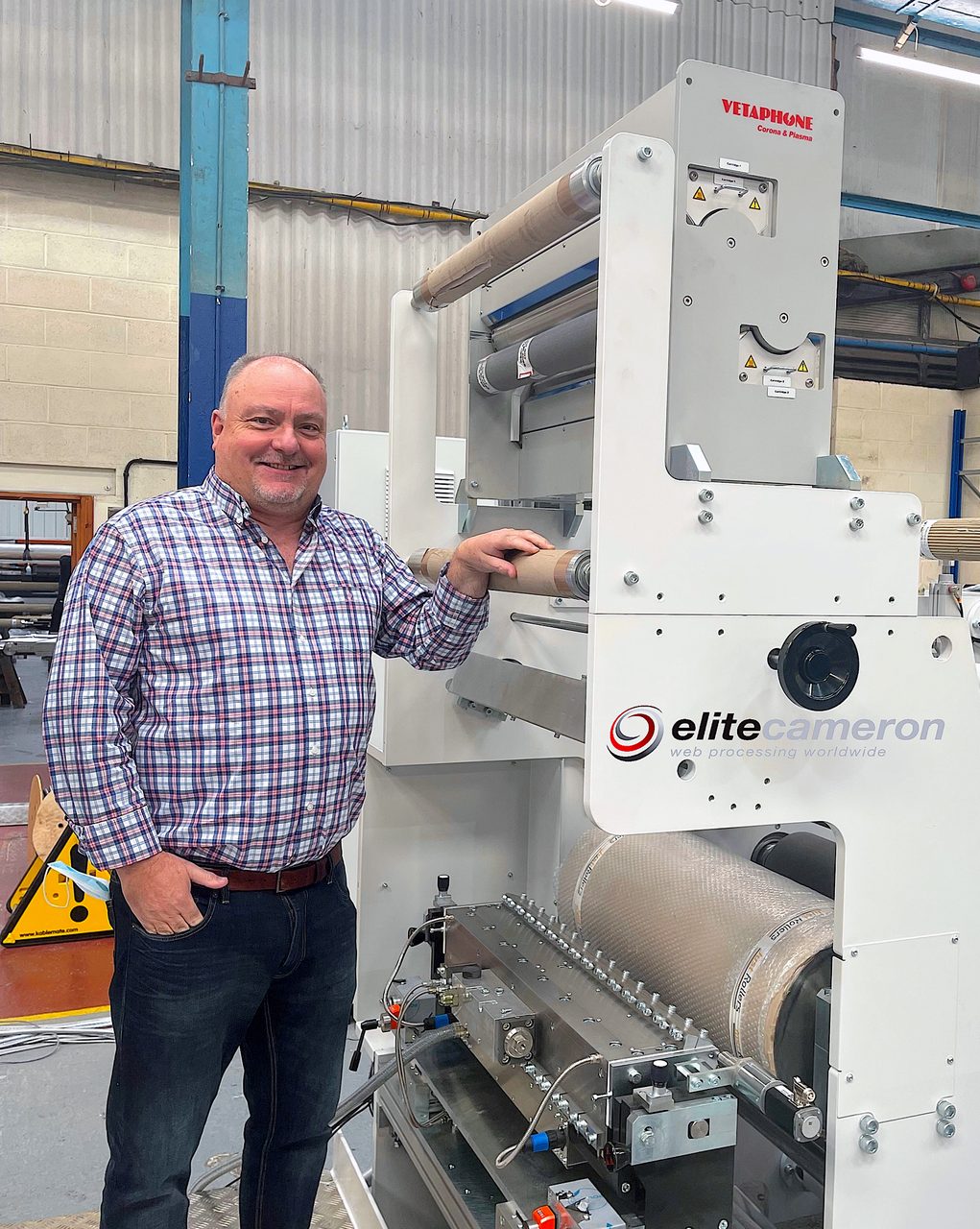
Tim Self with an Elite Cameron HM750 Hot Melt Coater fitted with a Vetaphone double-sided corona treater.
Image courtesy of TS Converting
Unlike the narrow web sector, where corona units are sold in volume and of similar specification, much of TS Converting’s business is wide web and niche. TS Converting has predominantly used Vetaphone corona technology on its hotmelt coating and laminating machines and has established a strong working bond with Vetaphone.
TS Converting recently turned to Vetaphone and its test lab facility in Denmark for research on unwind and rewind modules that needed highly accurate web tension control. Via the advanced PLC software in Vetaphone’s lab, TS Converting was able to view results at specific speeds and change settings “on-the-fly.”
TS Converting predicts that the company’s sales of coating and laminating technology will overtake that of slitter rewinders for the first time in 2021, and sees the growth in demand for UV hotmelt with high-performance adhesives as an important trend.
January 2022 // flexpackmag.com