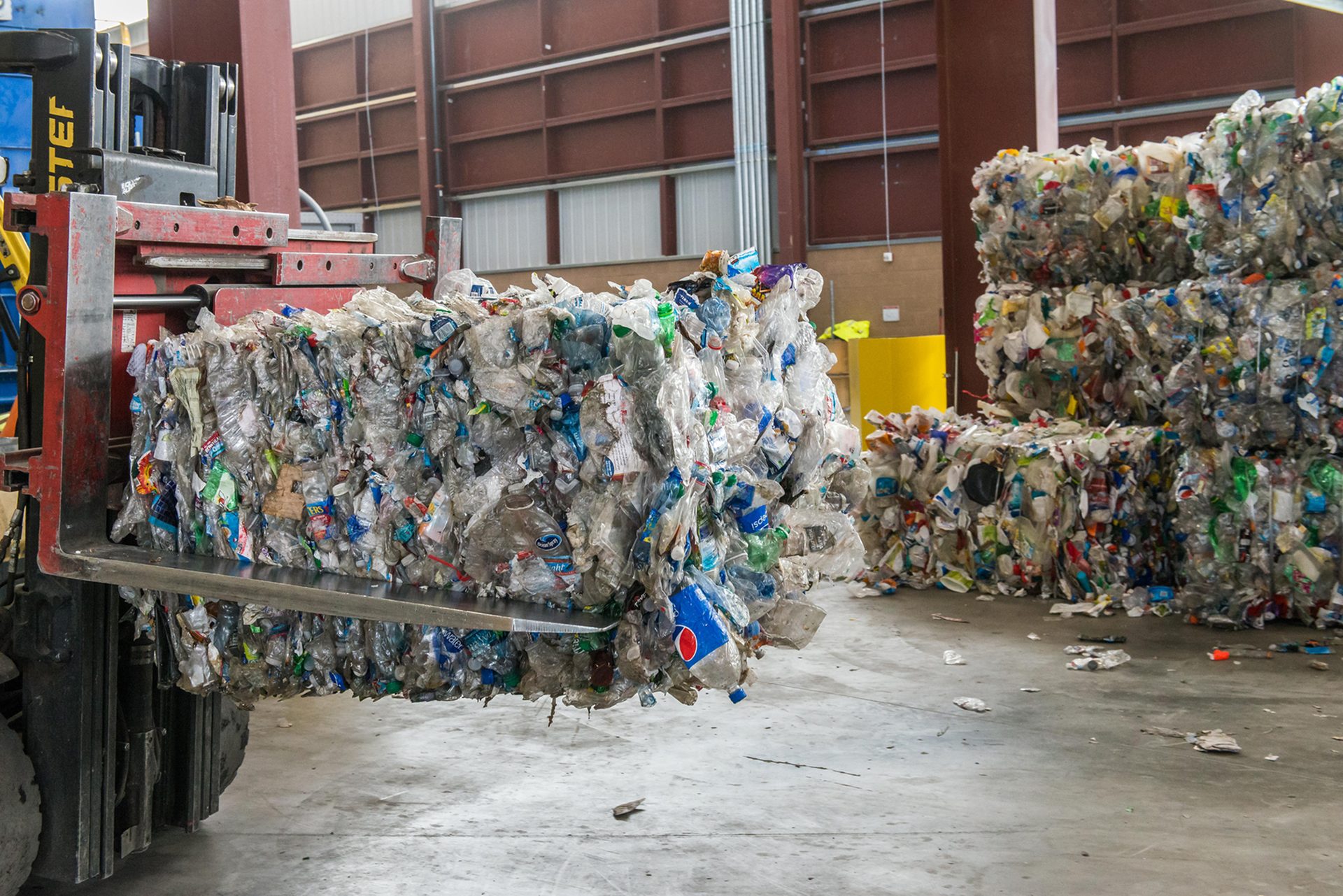
RECYCLING THEMES
Recycled Content is King for Brands and Takes Center Stage in 2022
Large and small consumer brands are partnering with many different stakeholders in the flexible packaging ecosystem with the express goal of finding supply chains of recycled content for the near future. The themes that appear to be emerging for 2022 are strategies for scale for mechanical recyclers, upstart advanced recycling companies and advanced sorting technologies to meet future demand.
By Grant Gerke
The last three years have seen many advancements in packaging waste recycling — down cycling and more efficient sorting at material recycling facilities — but global brands in 2022 are seeking and looking to cement dependable supply chains of post-consumer recycled (PCR) content to meet 2025 goals. Market action for recycled content in Europe is accelerating and advanced recycling developments are ramping up in the U.S., so what’s in store for 2022 in the packaging segment?
A recent development with sizable ramifications for consumer packaged goods (CPG) companies is the announcement by Republic Services, and its new plans to open a Polymer Center facility in 2023 and its integrated approach. The Polymer Center will manage the plastics stream through an integrated process from curbside collection of recycled material to production, and delivery of high-quality recycled content for consumer packaging.
ADVERTISEMENT
The facility will enable Republic to produce 100% post-consumer polyethylene terephthalate (PET) flakes for food applications, and also a higher-quality propylene and HDPE. The recycling company also cites high-density polyethylene (HDPE) and polypropylene (PP) recycling operations, such as detergent jugs that can be collected in a multicolored bundle and will be separated by plastic type and color. This also includes the objective of recycling orange juice jugs and converting into another orange jug.
"Packaged goods manufacturers have set ambitious targets to use more post-consumer content in their products, but the current supply of recycled plastics falls short,” says Jon Vander Ark, president and CEO, Republic Services. “Polymer Center will help meet the increasing demand for a reliable, high-quality supply of recycled plastics, assisting brands in achieving their sustainability goals.”
Republic Service plans to produce 100 pounds per year of post-consumer PET flake to bottle-to-bottle circularity, and is focusing on the western U.S. now. The company believes increased packaging waste demand from state legislation — California and Washington — should provide ample supply to meet this initial supply target.
John Standish, technical director at the Association of Plastic Recyclers, on a recent Material ConneXion webinar also cited legislation as a positive for more recycled content via single-use plastic containers. “We're going to coalesce around those three plastics for recycling — PET, HDPE and polypropylene (PP), and then we have a technology called near infrared (NIR) optical sorting that can detect those three plastics.”
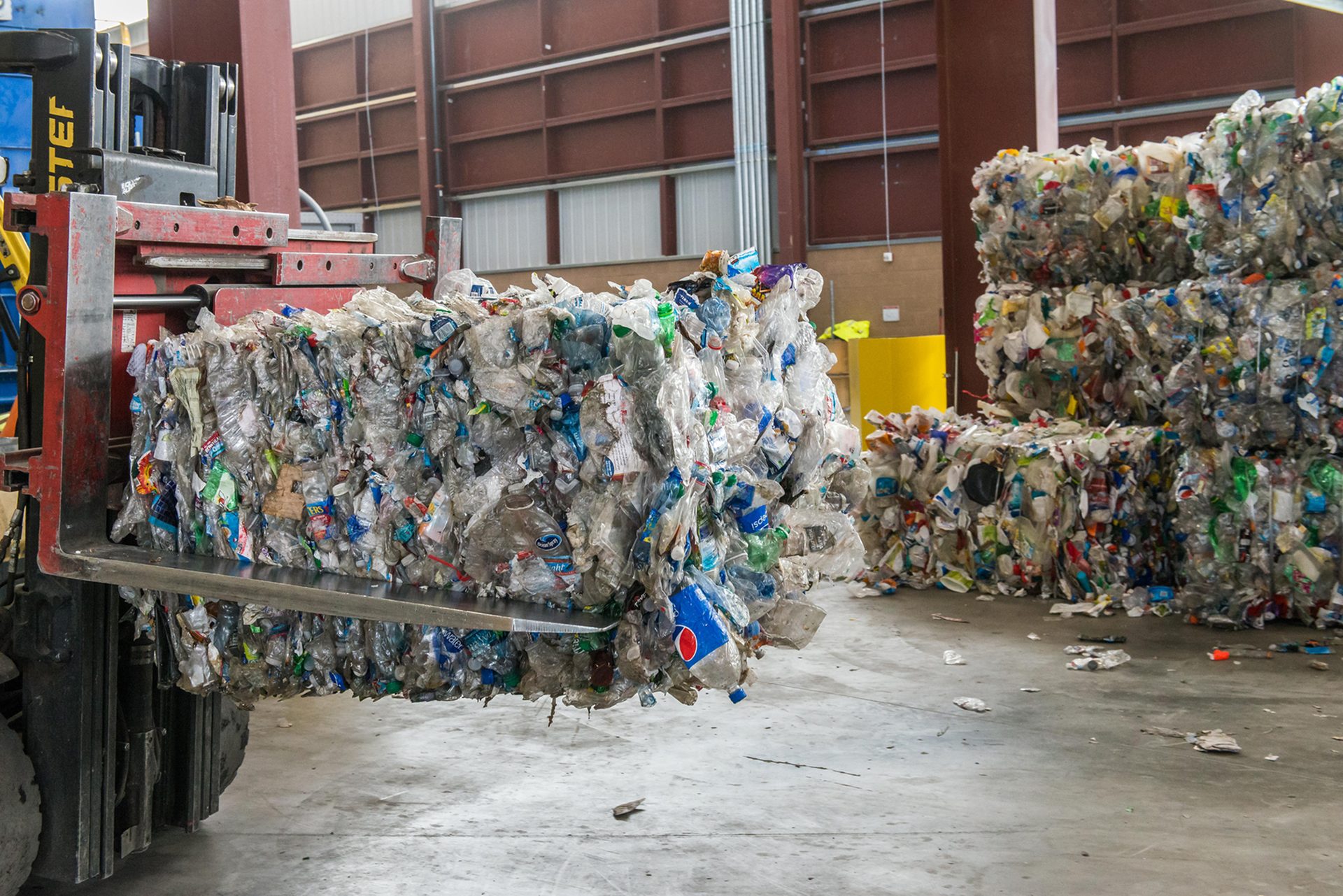
The Polymer Center, which will be built in Las Vegas, will manage the plastics stream through an integrated process from curbside collection of recycled material to production, and delivery of high-quality recycled content for consumer packaging.
Courtesy of Republic Services
Besides PP, PET and HDPE, The Materials Recovery for the Future (MRFF) consortium has been running a recycling pilot program for flexible packaging that also relies on an integrated approach. Created in 2015, this pilot focuses on flexible packaging waste, curbside collection and advanced NIR sorting technology. The pilot program upgraded the TotalRecylce materials recovery facility (MRF) with a flexible plastic packaging (FPP) recovery system using current optical sorters and peripheral equipment to optimize automated sorting.
Resource Recycling Systems, an independent contractor, provided a report on the pilot program in 2020 and five sortation performance goals. The goals included capturing at least 90% of the FPP in the incoming feedstock, minimizing paper, reducing fiber QC staff and adding new control systems at the facility — inexpensive automation technology gaining traction at MRFs.
Via the report, four of the five metrics have been met, with only the capture rate missing its targets. The pilot is looking for a 90% capture rate for the FPP in the feedstock (bales) and in 2020 the rate stood at a 74% capture; additional equipment tuning and minor upgrade was needed and being added to the process in 2020. Flexible Packaging magazine reached out to the main sponsor of the project in late 2021, the American Chemistry Council, but no new updates were ready at this time.
The pilot program upgraded the TotalRecylce materials recovery facility (MRF) with a flexible plastic packaging (FPP) recovery system, and is trying to meet five different sortation goals, see progress above.
Courtesy of American Chemistry Council
Prevailing Winds: European Recycling and Advanced Recycling
Many industry analysts are pointing to Europe as an indicator for U.S. recycling developments, as Europe is currently carving out certain policies that will increase recycling rates to 70-90% in Europe in the next two to three years. “European legislation says PET bottles will have 25% recycled content by 2025 and 30% recycled content by 2030, so there's wide use of extended producer responsibility (EPR) programs and taxes in some countries,” says Standish.
Standish adds that a crystal ball isn’t needed to see what will happen with recycling legislation in the U.S. and Extended Producer Responsibility legislation in Europe includes eco-modulation fees. The legislation says a producer is responsible for using the correct recycled label — truth-in-labeling — for a product, while using the wrong recycling label for the product the producer will pay a higher fee to recycle that package.
“Eco-modulation is a big driver and we can see all of these in Europe today and all the discussions taking place in the U.S. and Canada at the state level or province level,” adds Standish.
With these prevailing winds in Europe, global brands are also adding new technology and applications. Procter and Gamble’s (P&G) European Lenor brand recently transitioned away from opaque bottles to shrink-sleeved transparent material and then integrated digital watermarking technology to help the sorting and recycling process in Germany, Switzerland and Austria.
The Lenor brand is looking to the Holygrail 2.0 initiative in Europe which enables digital watermarking technology to more efficiently sort plastic scrap for recycling facilities. The initiative is driven by AIM, which represents the European Brands Association, and it has recently demonstrated a “successful validation of the prototype detection for digital watermarks.” The initiative and results claim that the technology can achieve more granular sorting and overcome limitations of current near-infrared (NIR) sorting technologies.
“European legislation says PET bottles will have 25% recycled content by 2025 and 30% recycled content by 2030, so there's wide use of extended producer responsibility (EPR) programs and taxes in some countries.”
John Standish, technical director at the Association of Plastic Recyclers
The HolyGrail 2.0 initiative includes machine vendor Pellenc ST and Digimarc, and is now ready for industrial-scale pilots to start later this year.
“These results emphatically prove that Digimarc digital watermarks can transform recycling,” says Digimarc CEO Riley McCormack. “What’s more, Digimarc Recycle, powered by Digimarc digital watermarks, provides the industry additional business value in addition to this core, critical enablement of a circular economy.”
Not to be outdone in the recycling department, advanced recycling made more news last month as PureCycle Technologies broke ground on its second U.S. plastics waste purification facility, where the company will take polypropylene waste — #5 waste — and convert the material into ultra-pure resin. This chemical recycling process is based on years-long research by Procter & Gamble and then licensed to PureCycle Technologies.
PureCycle's new Augusta, Georgia location will be able to support up to eight purification lines, which collectively are designed to produce approximately one billion pounds of like-new recycled plastic annually. The technology revolves around removing solid waste from PP waste batches — pigments, pieces of wood and metal — and activates a pressurized process that produces atmospheres.
After years of development, the proprietary technology is now a continuous process and can achieve scale. "Our second facility, when completed, will transform No. 5 plastic waste — one of the most commonly used and least recycled plastics in the world — into an ultra-pure material that can be used to make consumer products,” says Mike Otworth, CEO, PureCycle Technologies.
Polypropylene is P&G’s leading plastic material in terms of volume and, if displaced, could aid in reaching the company’s goal of reducing 50% of its virgin plastic from its products by 2030.
PureCycle expects the first two Augusta purification lines to be completed in the fourth quarter of 2023, with an ultimate capacity to produce 260 million pounds of like-new recycling resin annually.
Video by Constantinis / Creatas Video via Getty Images
May 2022 // flexpackmag.com