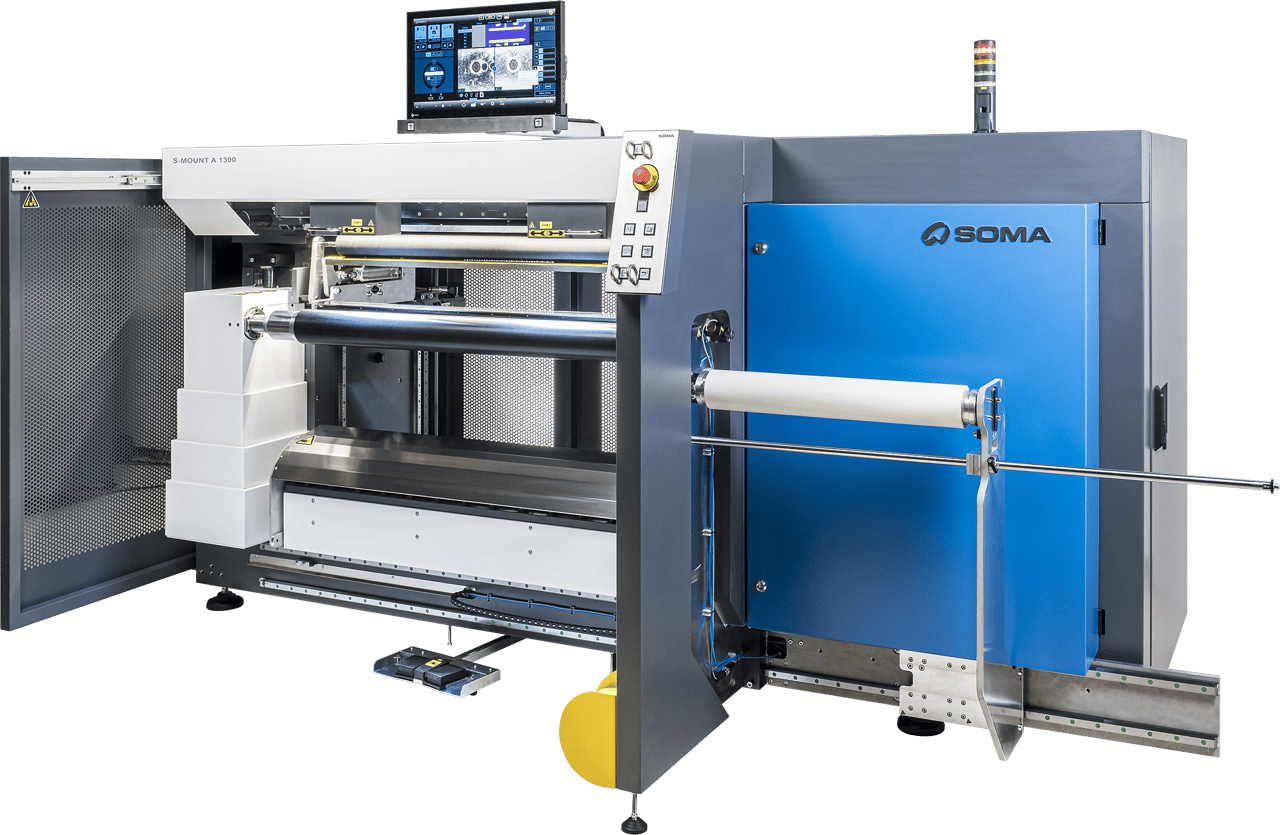

To Print Flexibles, You have to be Flexible
Industry 4.0 is being applied within flexo print facilities — and equipment manufacturers are playing an important role. Recent quality gains have made flexo presses much more viable for long and short runs, in turn making flexible packaging cost-effective and worthwhile.
By Garrett Taylor
Flexo printers/converters are always under pressure to limit costs. This comes not only from brands who are always interested in reducing packaging costs, but also competitive pressures from other printers.
But how do you stay competitive when there are more, shorter press runs? The answer isn’t always digital, as flexo workflows and presses have become more efficient. One of the best ways to save costs — both material and labor — is to be flexible and reduce makeready time. There are more and more quick changes and makereadies in flexo, offered by throughput automation. The faster a printer can change plates — and perhaps inks — and get a job running in registration, the more work a printer can complete with greater capacity and with less waste. Shorter makereadies deliver the ability to run more jobs per day and to profitably print short-run jobs. There are many ways innovative flexo presses can help.
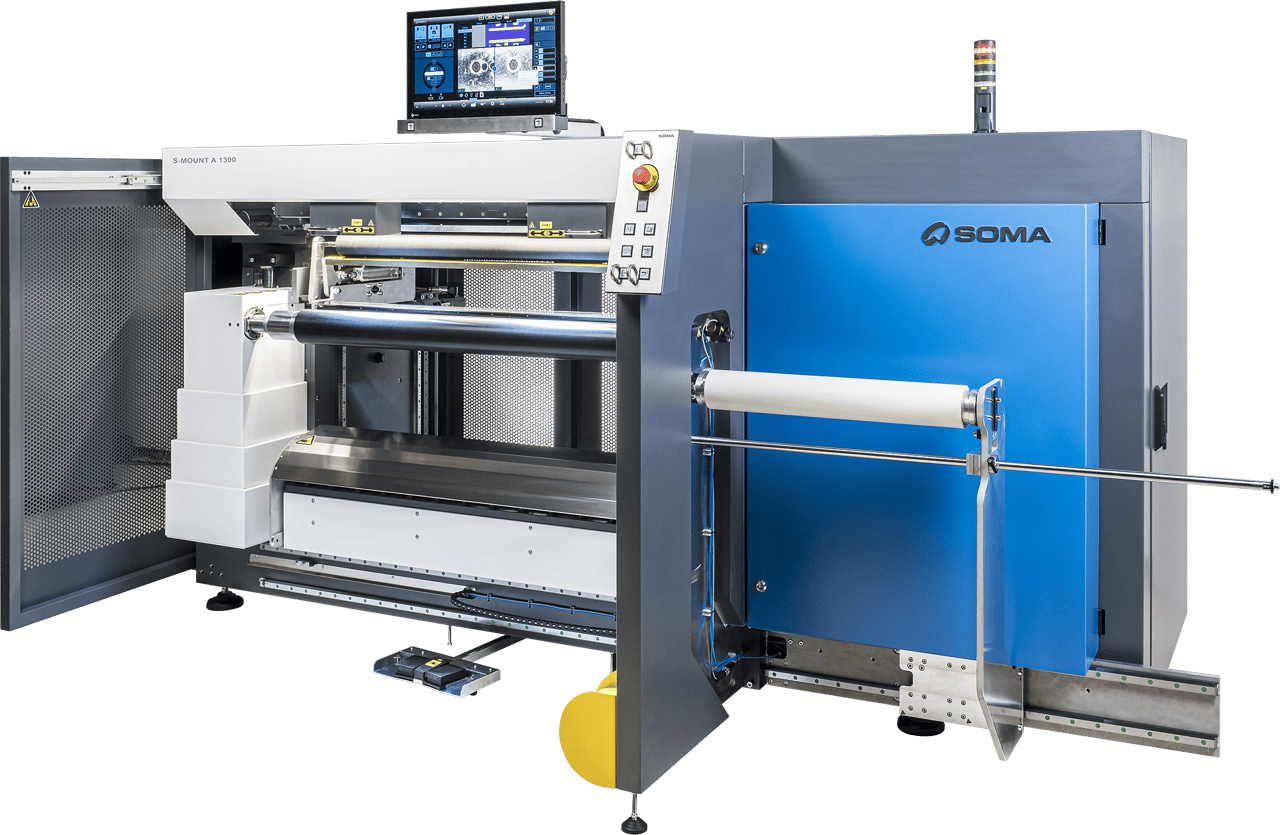
SOMA plate mounter, S-Mount.
Eliminating a Mounting Problem
For starters, there’s an opportunity to advance accuracy and efficiency upstream from the press. One of the most impactful areas that determines flexo printing success is plate mounting, and the subsequent job changeovers on the press. The best jobs for automatic mounting are short runs, those requiring tight registration, and those that utilize expanded gamut printing. Printing with additional process colors is not even possible without exceptional registration. An automatic plate mounter helps to assure that a job is in perfect registration, every time sleeves go to press.
Automatic plate mounting can reduce the time needed to mount plates, as the machine puts the plate in the final position and applies it to the sleeve — and the process each time is repeatable. There is also virtually no press downtime caused by proper mounting of the printing plate. So, the overall press efficiency increases.
When that repeatable process is used in conjunction with an offline registration and impression settings system, there is no longer a manual burden on the press operator to set the press. During the plate mounting process, the position of the plate on the sleeve is determined, along with the topography of the plate to set the impression. The data is stored in an RFID chip that is embedded in a slightly modified sleeve. When the sleeve is placed onto the press, the data is read and the registration and impression pressure are set automatically, without manual intervention. This reduces makeready time, delivering added capacity and faster completion of jobs — along with almost zero-meter set-up waste.
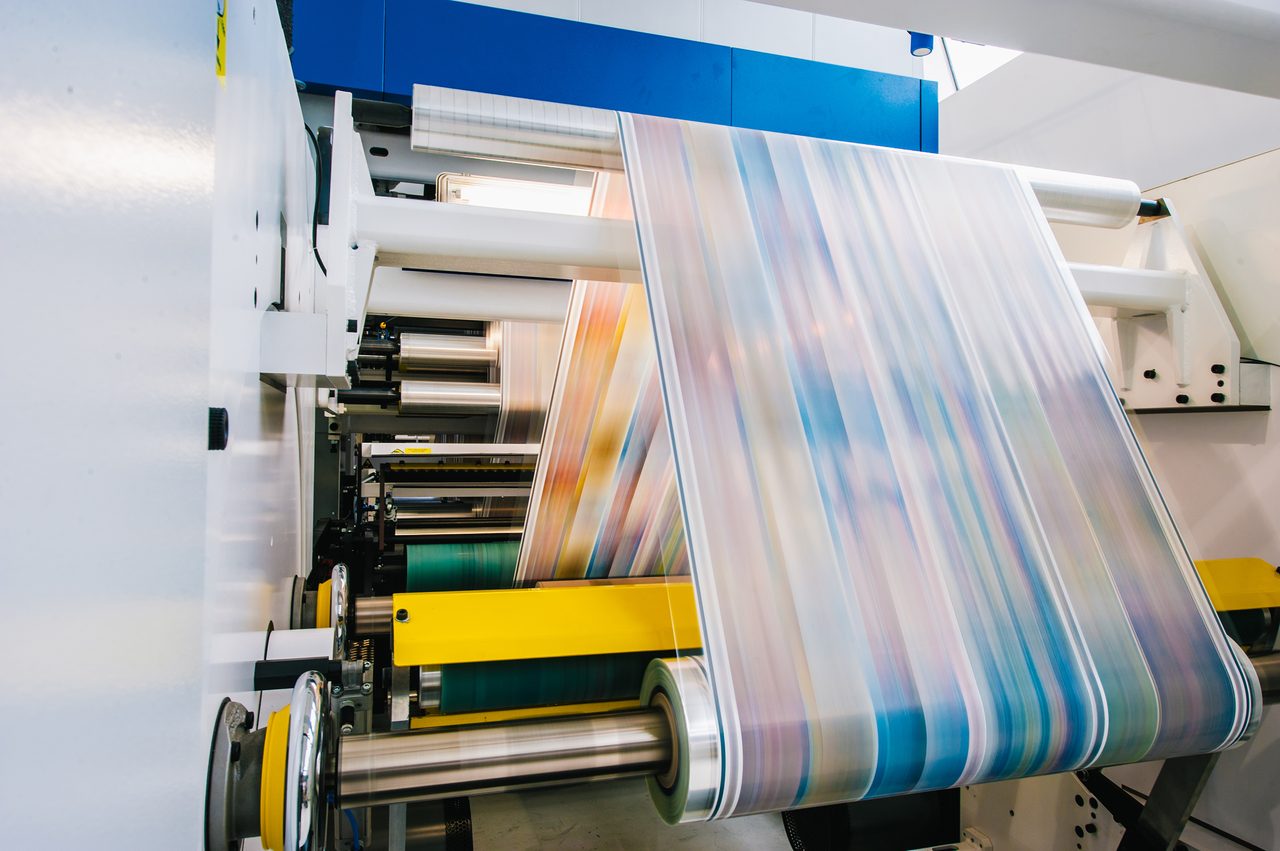
Drives can be automatically tuned to minimize the bouncing effect for each particular design while keeping perfect registration.
Ready For a Tune-Up
Controlling bounce on a flexo press is critical because it retains job consistency — particularly when using high definition plates — at very fast speeds during the press run. It can also assure that the press can hold stable highlight dots with exceptional registration. This opens the door for new print process ideas, such as expanded gamut printing, which as we know, limits the need for washouts between jobs.
Flexo press drive mechanisms already analyze performance. During job setup — and taking less than one minute — we can automatically tune the drives with specially designed algorithms that can minimize the bouncing effect for each particular design while keeping perfect registration. This lets each specific piece of artwork achieve its ideal drive setting on the press.
The Wider, the More Efficient
A wider press can be optimized to run label stock paper and film packaging materials, bridging the gap between narrow and wide web printing for products such as in-mold and wraparound labels, larger shrink sleeves and stand-up pouches. And, for quicker runs, imposed step & repeat layouts result in greater multiple-up printing and faster runs.
In the past, one of the biggest fears was the expertise required to operate these larger presses. With the sophistication discussed here, mid-web presses can be efficiently run by as few as one and a half people, optimized for short runs, high quality printing and maximum customization.
Save Ink — and Time
A good auto washup system removes residual ink from the complete inking system, including doctor blade chambers, anilox sleeves, connecting hoses, pumping hoses and filter cage. Some flexo presses have ink cartridge systems that reduce ink costs where expensive LED, spot color, special effect and metallic formulations are required. Reducing ink volumes (as little as one liter of ink in the inking loop with short hoses) results in minimal ink residual waste during wash-up, letting printers maintain profit margins on each job.
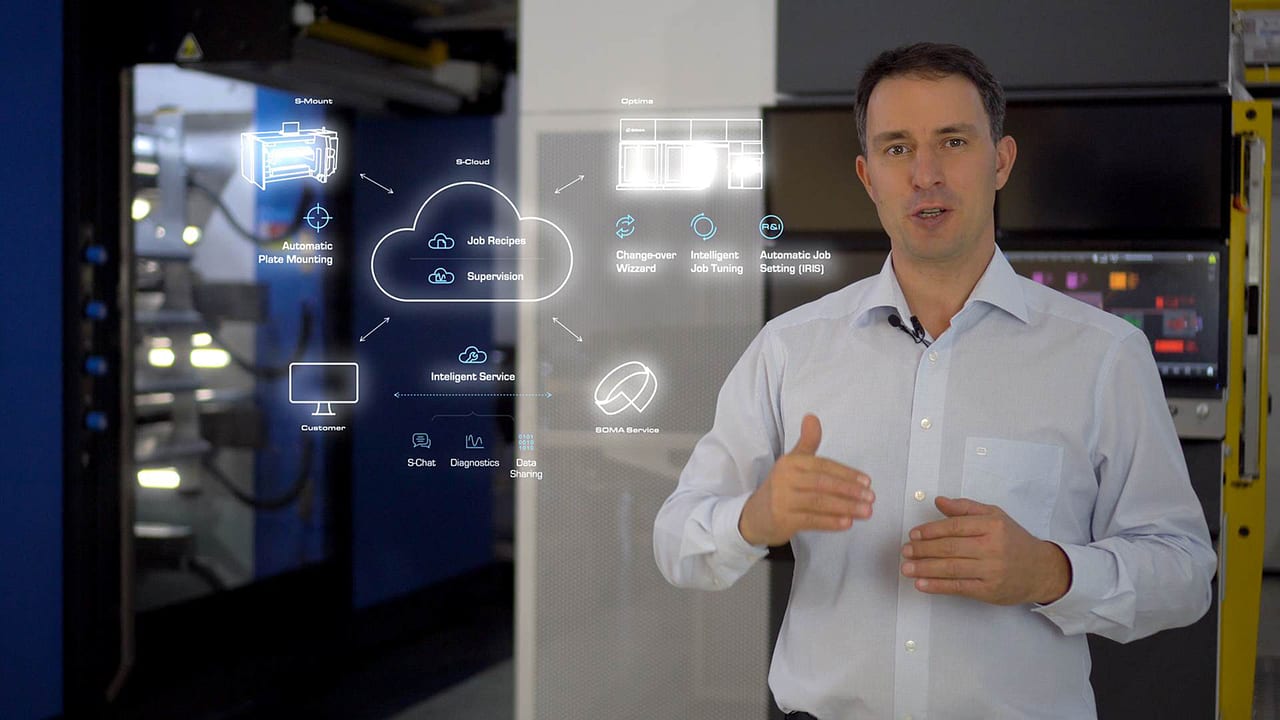
SOMA's Intelligent Automation is a typical example of Industry 4.0 solution.
We Can Be More Intelligent
Industry 4.0 is being applied within flexo print facilities — and equipment manufacturers are playing an important role. Data is now tied to the press. By connecting software and equipment to the Cloud, we can develop and utilize intelligent functions that boost efficiency and minimize operator errors. By making presses smarter, we are making print quality better and press operation much more efficient.
There is a lot of data that can be shared between software and hardware systems, moving job and registration data from step and repeat prepress systems to mounters and, ultimately, to the press. Every job has uniquely specific data. Key parameters, such as specific job information affecting changeovers, press status and press energy consumption are just some of the information being shared. They can be entered on a press control panel, from any Cloud-connected device, and/or data from the customer’s MIS/ERP systems. The easy transfer of job recipe data — communicating all job details — offers further intelligent functions. Thus, the press knows exactly the parameter settings for each job to be printed.
With this knowledge, flexo presses are being introduced with changeover ‘wizards’ that guide less-skilled press operators flawlessly during the changeover process. It automates many steps, minimizing the number of manual tasks and reduces operator error.
Flexo presses have become much more viable for long and short runs. While flexo presses and prepress systems have made extraordinary quality gains in the recent past, the focus on speed and efficiency is really contributing to a very cost-effective system. By being flexible, these presses make flexible packaging extremely cost-effective, even for short runs. Don’t rule them out.
Garrett Taylor, SOMA U.S. and Canada sales director, has 25 years of experience in the printing and packaging industry, specifically with flexographic printing.
Photos courtesy of SOMA.
October 2021 // flexpackmag.com