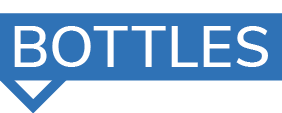
Goodbye to Single-Use Plastic
From bamboo to Dry Molded Fiber to paper, companies are turning to sustainable alternatives to plastic when it comes to bottle production.
By Brad Addington
2023 was abundant with packaging innovations, including when it comes to one of the most ubiquitous packaging options of all: bottles.
One key initiative has been to reduce the use of single-use plastic bottles in food, drink, consumer health and Fast-Moving Consumer Goods (FMCG) industries. To accomplish this, PulPac has teamed up with PA Consulting Group to launch The Bottle Collective, which will use PulPac’s patented Dry Molded Fiber as an alternative to plastic bottle packaging.
Meanwhile, CelluComp and RyPax have teamed up to offer their own fiber-based bottling solutions. One involves a novel pulp fiber made of a proprietary cellulose product (Curran®), bamboo and bagasse. The material can be applied as a thin, impermeable coating to the bottle’s interior, eliminating the need for a plastic liner.
Not to be outdone, Paboco (The Paper Bottle Company), plans to produce a fully recyclable paper bottle at a new state-of-the-art manufacturing site in Denmark starting in late 2024.
Read more about these companies at the forefront of developing sustainable alternatives to plastic bottles.
ADVERTISEMENT
PulPac and PA Consulting Partner to Launch The Bottle Collective
PulPac, a leading developer and provider of groundbreaking manufacturing technology for low-cost, high-performance fiber-based packaging and single-use products, has partnered with PA Consulting Group to launch a new initiative that will help minimize the use of single-use plastic bottles in food, drink, consumer health, and FMCG industries.
READ MORE
Using PulPac’s patented Dry Molded Fiber, The Bottle Collective will create a fiber-based alternative to plastic bottle packaging that will help contribute to the circular economy. The manufacturing process uses less CO2 than plastic and conventional wet molding options, and almost no water is used in manufacturing, which creates a highly versatile container mold for consumer companies.
“Plastic bottles are the holy grail of plastic replacement,” said Sanna Fager, Chief Commercial Officer at PulPac. “They have an estimated annual production volume of up to 500 billion pieces and are a significant source of plastic pollution worldwide. We are proud to share some of our patent-protected advances with PA Consulting, combining Dry Molded Fibers’ forming versatility, broad barrier applicability, and high production efficiency. Backed by strong partnerships across the value chain, we can bring competitive unit cost into the fiber-bottle space, enabling the shift away from today’s single-use plastic. We encourage all brands and relevant industry actors to join this force for sustainable change.”
PA Consulting’s mechanical engineering, design, automation, and material sciences teams, along with PulPac, have developed the first functioning prototypes, and multiple leading brand partners have already joined the Bottle Collective to continue developing and scaling fiber bottles by 2025.
“We are thrilled to announce the Bottle Collective,” said Tony Perrotta, PulPac Partnership Lead at PA Consulting. “Together with leading global consumer brand partners, we can fast-track the development of the world’s first Dry Molded Fiber bottle. This will make the most of our renewable resources while delivering significant positive impact to reduce today’s single-use plastic pollution. We have the technology. We have a functioning prototype and process. We are now ready to enter the next stage - demonstration that our Dry Molded Fiber bottles are capable of being produced at the speed, volume, and cost necessary to match the massive scale of this global industry challenge.”
To learn more about PA Consulting, please visit paconsulting.com. To learn more about PulPac, please visit pulpac.com.
The manufacturing process for PulPac’s patented Dry Molded Fiber uses less CO2 than plastic and conventional wet molding options, and the process uses almost no water as well.
Courtesy of PulPac
Multiple leading brand partners have already joined the Bottle Collective to continue developing and scaling fiber bottles by 2025.
Courtesy of PulPac
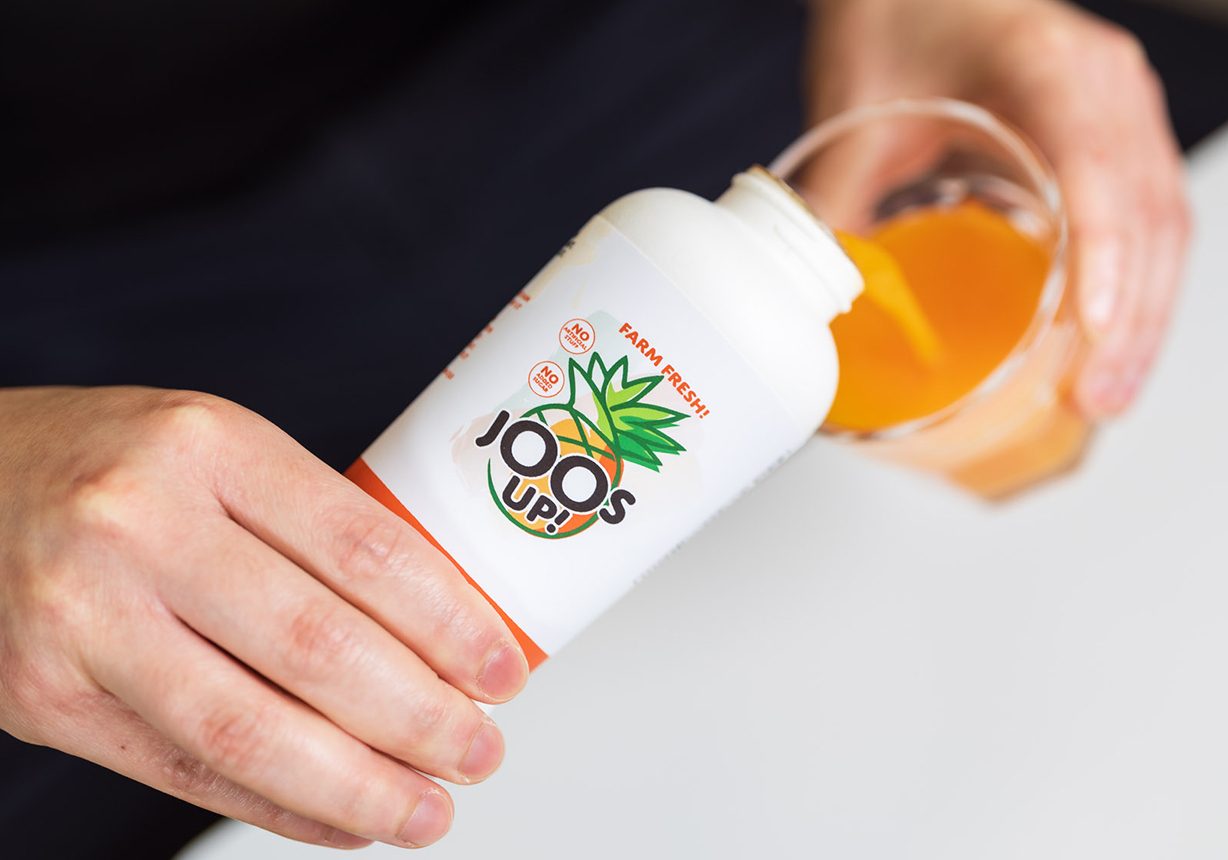
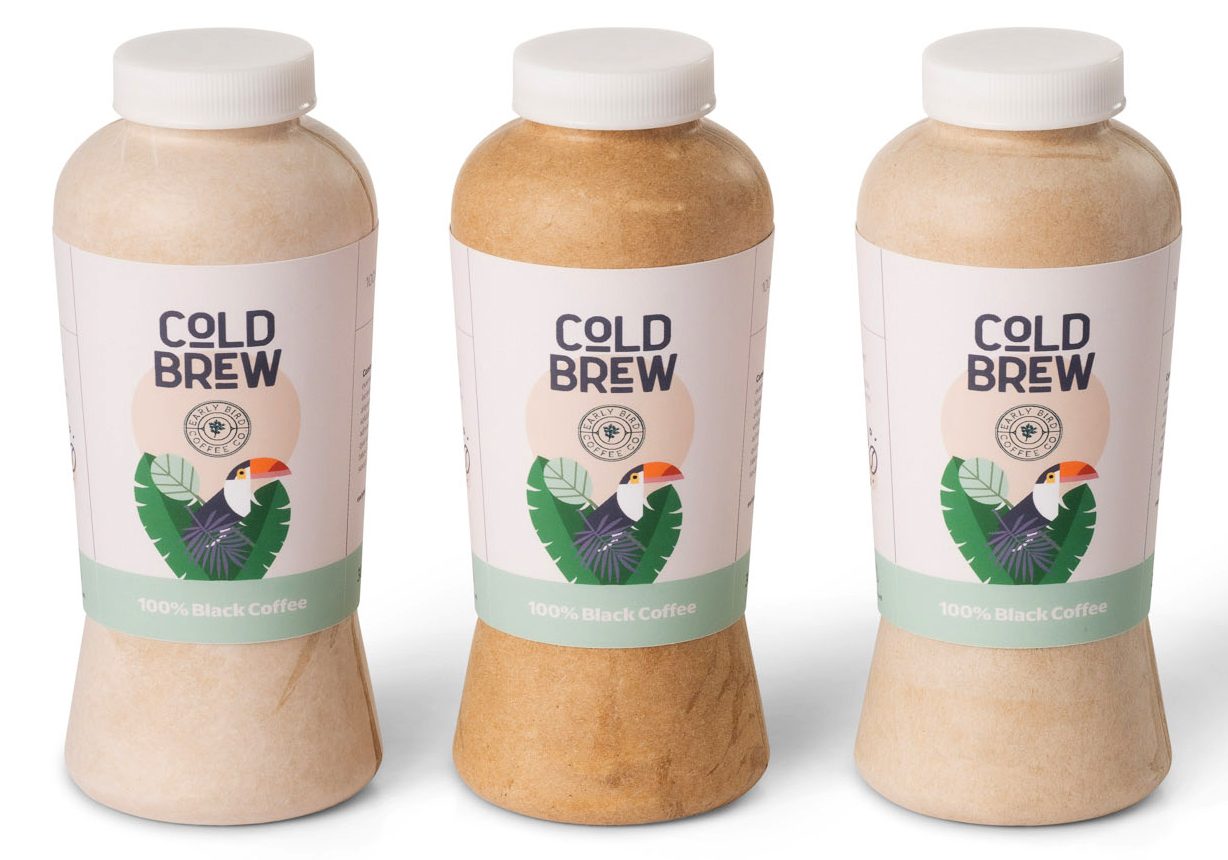
COLLAPSE ARTICLE ABOVE
CelluComp and RyPax Debuted All-Fiber Bottle at PACK EXPO Las Vegas
After years of perfecting its propriety microfibrillated cellulose product, Curran®, made from the waste stream of root vegetables, Scottish-based CelluComp, and Asia-based molded fiber packaging production firm, RyPax, are pushing the industry forward by combining precision plant-based packaging production with a highly renewable feed stock ingredient to crack the code on the all-fiber bottle.
The revolutionary step the two independent businesses took was developing a novel pulp fiber made with a mix of Curran®, bamboo and bagasse. This material is extremely strong with minimal porosity and allows the application of a thin, impermeable coating to the bottle’s interior, which allows manufacturers to take the next important step in environmental packaging by eliminating the need for a plastic liner.
“Integrating RyPax’s and CelluComp’s proven technology, materials and production expertise to produce the industry’s first all-fiber bottle at scale is a major evolution for the industry,” said Christian Kemp-Griffin, CEO of CelluComp. “Our unique capabilities and entrepreneurial approach, including establishing a Minnesota-based Public Benefit Corp. to better serve U.S. operations, has finally produced a design most packaged goods companies, and their consumers, have been longing for.”
READ MORE
“Combining our global expertise in fiber packaging design and production, with CelluComp’s creative ingredient solution, we’re looking at a true barrier packaging breakthrough,” said Alvin Lim, CEO of RyPax. “This initiative will remove millions of tons of plastic waste from the environment.”
RyPax and CelluComp have been collaborating on a commercial all-fiber bottle format for more than three years and recently gained validation from the Danish Technological Institute (DTI), who has been an important partner in helping create viable proof of concepts.
“This collaboration and design is something the industry has been waiting to see for a very long time and we’re excited a solution is now available,” said Alexander Bardenstein, business development manager with DTI. “The RyPax/CelluComp bottle has been through all of our comprehensive testing to earn our endorsement and allows them to start tailoring this technology for the global marketplace.”
The partnership is poised to scale production for industry applications from beverage, beauty, health, medicine, food and other retail brands to help manufacturers deliver a more sustainable product to reduce waste and meet consumer, government and their own sustainability goals. Moving forward, RyPax and CelluComp will, in close collaboration with DTI, explore additional fiber packaging solutions including fiber screw threads, caps, even thinner coatings, and a more intricate means of branding on bottles for their customers.
RyPax and CelluComp presented demos of the bottle at PACK EXPO Las Vegas in September.
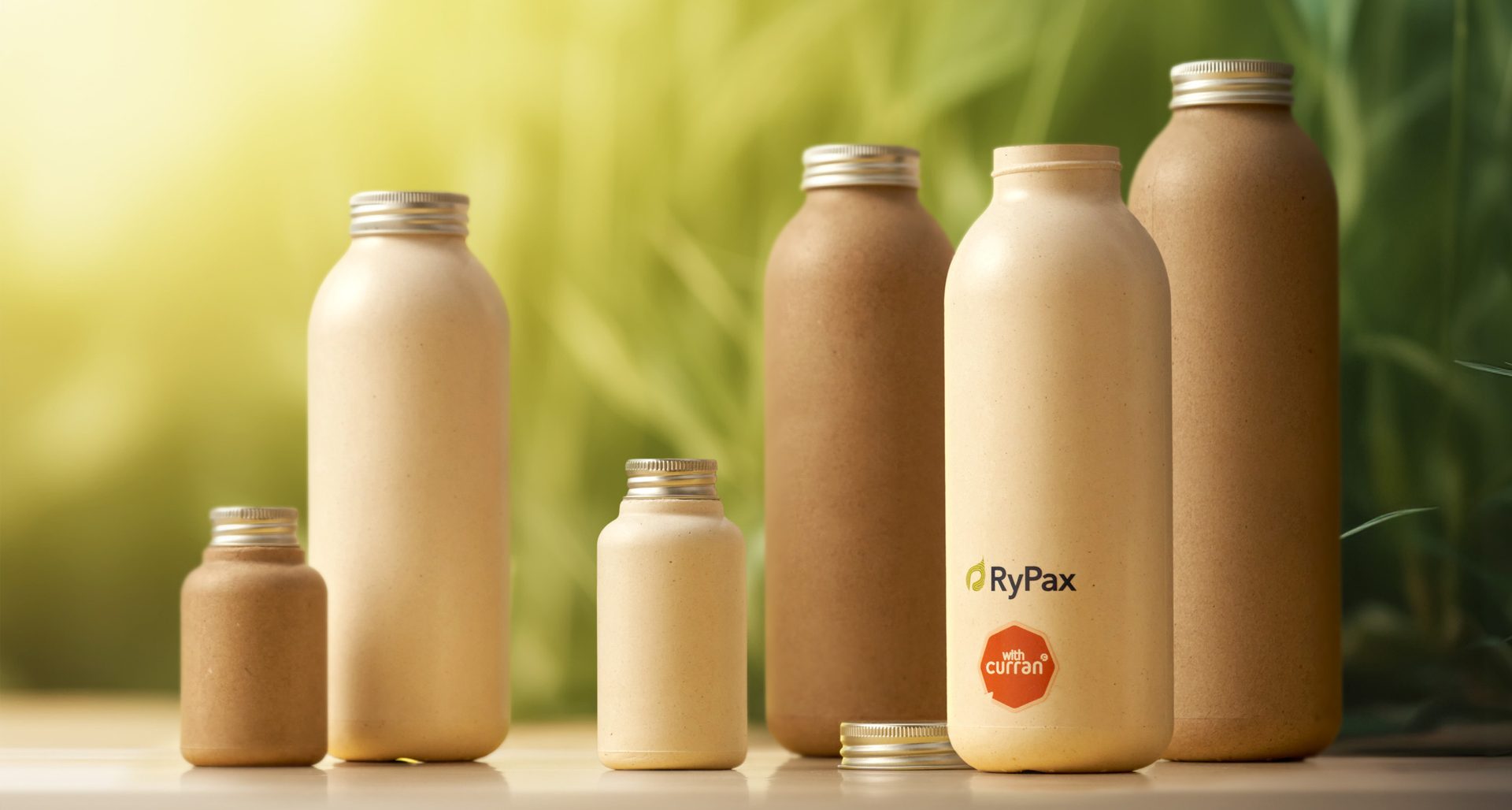
RyPax and CelluComp have been collaborating on a commercial all-fiber bottle format for more than three years and recently gained validation from the Danish Technological Institute (DTI).
Courtesy of CelluComp
COLLAPSE ARTICLE ABOVE
Denmark's Paboco to produce fully recyclable paper bottles at new facility in 2024
Paboco develops bio-based packaging solutions made from pulp. The Danish joint venture was founded in 2019 by ALPLA and pulp and paper manufacturer Billerud.
ALPLA is now taking over Billerud’s shares and, as majority shareholder, is investing in scaling up manufacturing capacity. From the end of 2024, Paboco plans to produce a fully recyclable paper bottle at a new state-of-the-art manufacturing site in Denmark.
Paboco (The Paper Bottle Company) develops and produces fiber-based packaging solutions using innovative pulp-forming technology. The company was founded in 2019 by ALPLA and Billerud as a joint venture. By taking over all of Billerud’s shares and investing in Paboco, ALPLA is pushing the rapid industrialization of the fully recyclable paper bottle made from FSC-certified fibers.
“Safety, affordability and sustainability are the central criteria of our packaging solutions. After several years of intensive development and groundbreaking innovations, the Paboco team is now ready to take its pioneering product to the market and establish the paper bottle as a sustainable alternative for a wide range of customers,” says ALPLA CEO Philipp Lehner.
READ MORE
Successful test phase
Since 2021, Paboco has been testing the first products on the market together with the Paboco Pioneer Community members: The Absolut Company, Carlsberg Group, The Coca-Cola Company, L’Oréal and Procter & Gamble. After the successful test phase, series production of the next generation of recyclable paper bottles is scheduled to start at the end of 2024.
Tim Silbermann, CEO of Paboco, said, “The vision of the fully bio-based and recyclable paper bottle has driven the team to create amazing results in just a short development period. With the bottle configuration now, we are targeting the beauty and fabric and home-care segment, but continuous development will also enable us to bring our next-generation bottle into further applications. We are happy that ALPLA is fully committed to supporting us on this journey.”
For the market launch, the company plans to set up a new state-of-the-art manufacturing site and development center in Denmark. There are currently 18 employees at Paboco. That number is expected to increase significantly by the time series production begins.
Innovations for the future
The long-term goal of Paboco is to develop and scale fully bio-based and recyclable paper bottles. In doing so, the company can count on the support of ALPLA.
“We at ALPLA work intensively on alternative materials, invest in promising projects and actively shape technological progress as a ‘Family of Pioneers,’” emphasizes Christian Zmölnig, Director, Corporate Research, Development and Innovation at ALPLA and Chairman of the Board of Directors at Paboco.
The share transaction took place at the beginning of October. The contracting parties agreed not to disclose the details.
