
PROGRESS IN PALLETIZING
Several key developments have taken place when it comes to palletizing.
By Bobby Douglas
As suppliers are looking to be more efficient in their end-to-end solutions, a key area of focus has been finding innovative ways to improve the palletizing process.
- CMES Robotics recently announced a fully automated mixed-case palletizing system that is suitable for a variety of sectors like e-commerce, food and beverage, and manufacturing.
- Additionally, Schneider Packaging Equipment Company reached a licensing agreement with the ITW Hartness Division to enter the high speed palletizing market.
- British Sugar enlisted the help of Sidel to install a compact and flexible case packing and palletizing solution that is capable of handling multiple pallet and format types to accommodate single sugar bags to new shelf-ready secondary packaging.
- And finally, Piab introduced a lightweight bag gripper that can fit any roller conveyor on the market.
Read more about these solutions below.
ADVERTISEMENT
CMES Robotics Introduces Innovative Mixed-Case Palletizing Solutions
CMES Robotics, a leading provider of advanced AI vision software, has announced a fully automated mixed-case palletizing system using Yaskawa Motoman. Together, they are introducing a solution that can palletize complex random cases at a production rate without the need for training prior to deployment.
The new mixed-case palletizing solutions combine CMES Robotics' expertise in automation systems with state-of-the-art robotic technologies. This collaboration aims to address the growing demand for flexible and efficient palletizing solutions in industries such as e-commerce, logistics, food and beverage, manufacturing, and more.
With the rise of omnichannel retailing and customized order fulfillment, businesses face the challenge of efficiently palletizing a variety of products with different shapes, sizes, and weights. Traditional palletizing systems often struggle to handle mixed case configurations, leading to slower operations, increased labor costs, and potential product damage.
READ MORE
CMES Robotics’ mixed-case palletizing addresses these challenges. The innovative system utilizes advanced vision systems and intelligent software algorithms to accurately identify and handle diverse products while optimizing palletizing patterns for maximum stability and space utilization.
By integrating high-performance robots with CMES Robotics' code-free easy-to-use control systems, the mixed-case palletizing solutions deliver increased productivity, reduced labor requirements, improved order accuracy, and enhanced workplace safety. The collaborative efforts of these companies ensure seamless integration and streamlined operations within existing production lines.
"We are thrilled to bring these mixed-case palletizing solutions to the market," said Alex Choe, President of CMES Robotics. "Our combined expertise and commitment to innovation have resulted in a truly easy-to-use system that will help businesses optimize their palletizing processes, increase efficiency, and meet the demands of today's dynamic market.”
CMES Robotics is confident that the combined mixed-case palletizing solutions will transform the way businesses handle complex packaging requirements. With the ability to handle diverse product mixes, reduce costs, and improve overall operational efficiency, these solutions will empower businesses to stay competitive in an ever-evolving marketplace.
For more information, visit CMES Robotics’ product site at cmesrobotics.com.
CMES showcases new palletizing solutions at PACK EXPO Las Vegas.
Courtesy of CMES Robotics
The innovative system utilizes advanced vision systems and intelligent software.
Courtesy of CMES Robotics
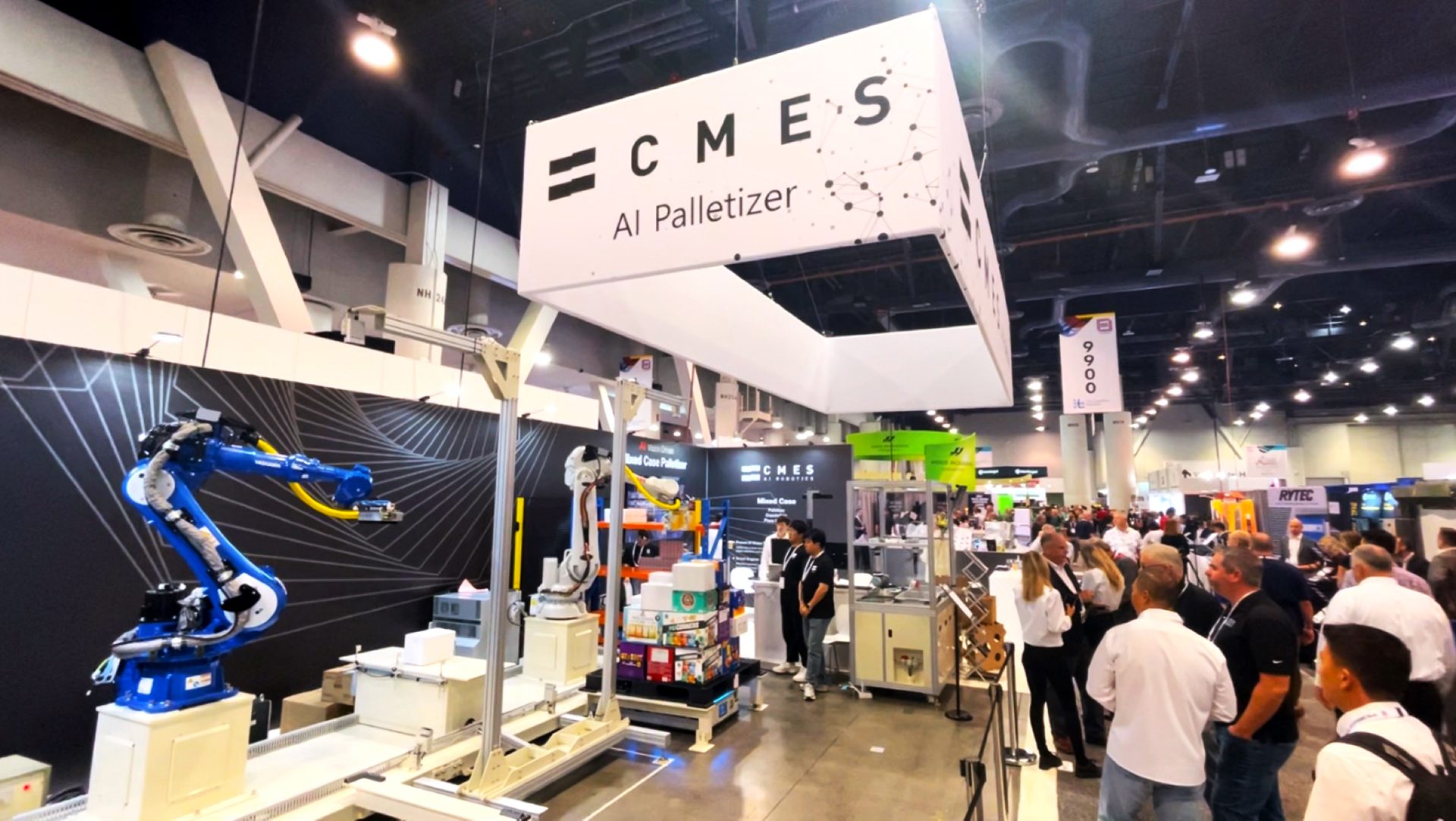
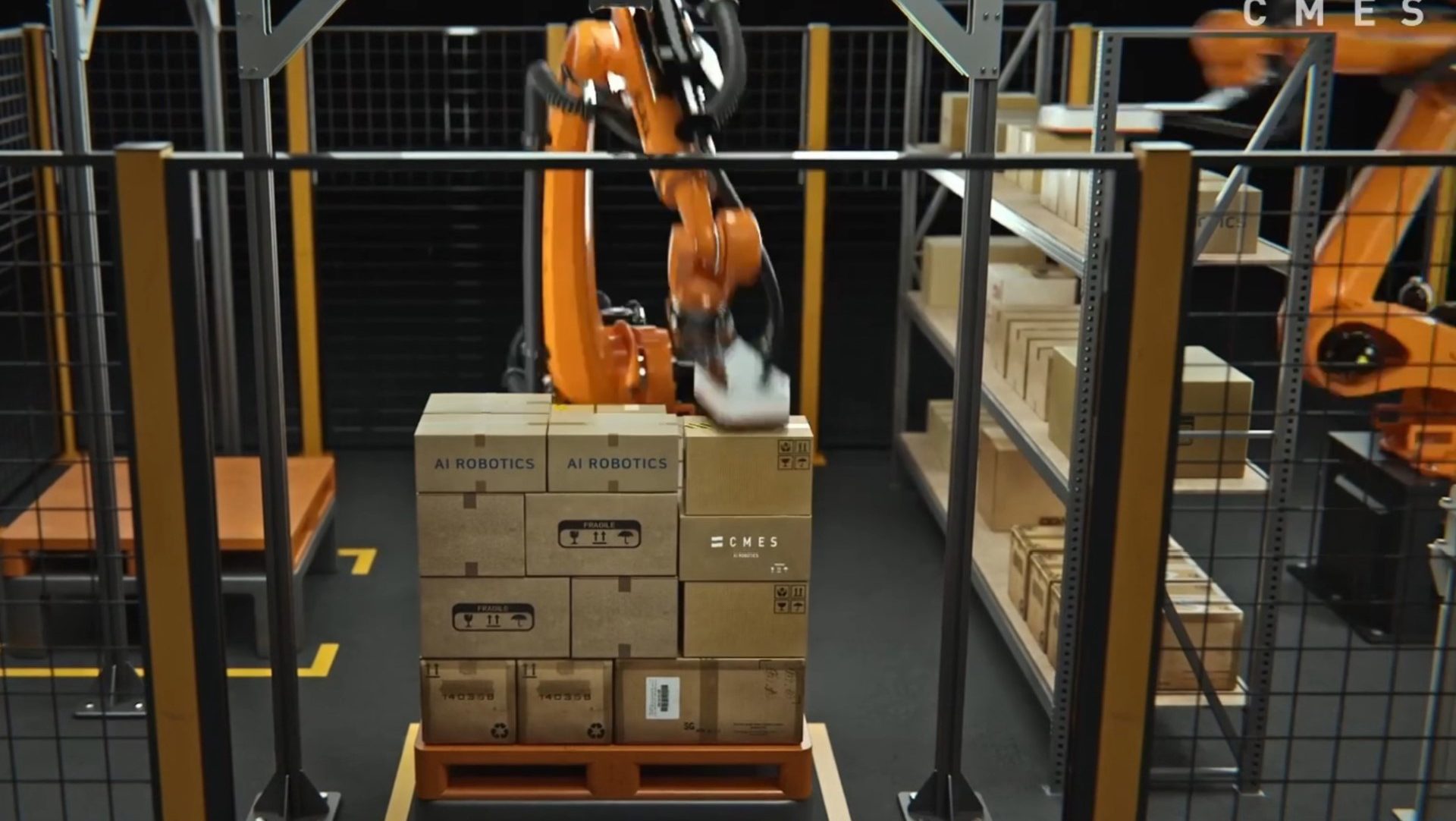
COLLAPSE ARTICLE ABOVE
Schneider Packaging Equipment Enters High-Speed Palletizing Market
Schneider Packaging Equipment Company Inc., a Pacteon Company, has entered the robotic high-speed palletizing market through a strategic licensing agreement with the ITW Hartness Division.
After the Hartness Division’s strategic decision to reposition its product portfolio, Schneider began key conversations around setting up a licensing agreement for the Hartness Division’s high-speed robotic palletizing offerings to ensure the ability for Schneider to offer on future projects. Also included in the agreement is the ability for Schneider to support already-commissioned systems by Hartness.
READ MORE
Specifically included in the agreement is The Hartness High-Speed Layer Palletizing Tool. In anticipation of this, Schneider spent the last few months completing training at Hartness and is now able to offer the solution to the market.
Schneider — an industry leader in end-of-line automation, a FANUC-Certified Servicing Integrator, and a PMMI-Certified Trainer — has been providing robotic palletizing solutions for over three decades. With the addition of the High-Speed Layer Palletizing Tool, they are now able to offer their world-class solutions to an even larger portion of the palletizing market.
Mike Odom, CEO of Pacteon Group, said, “When the opportunity arose for us to create this formal agreement to leverage Hartness IP in the high-speed palletizing segment, we reacted quickly to support the market with these additional high-quality tools. With the Hartness tools added to the ESS and Schneider Palletizing Solutions, we can support all conceivable palletizing applications.”
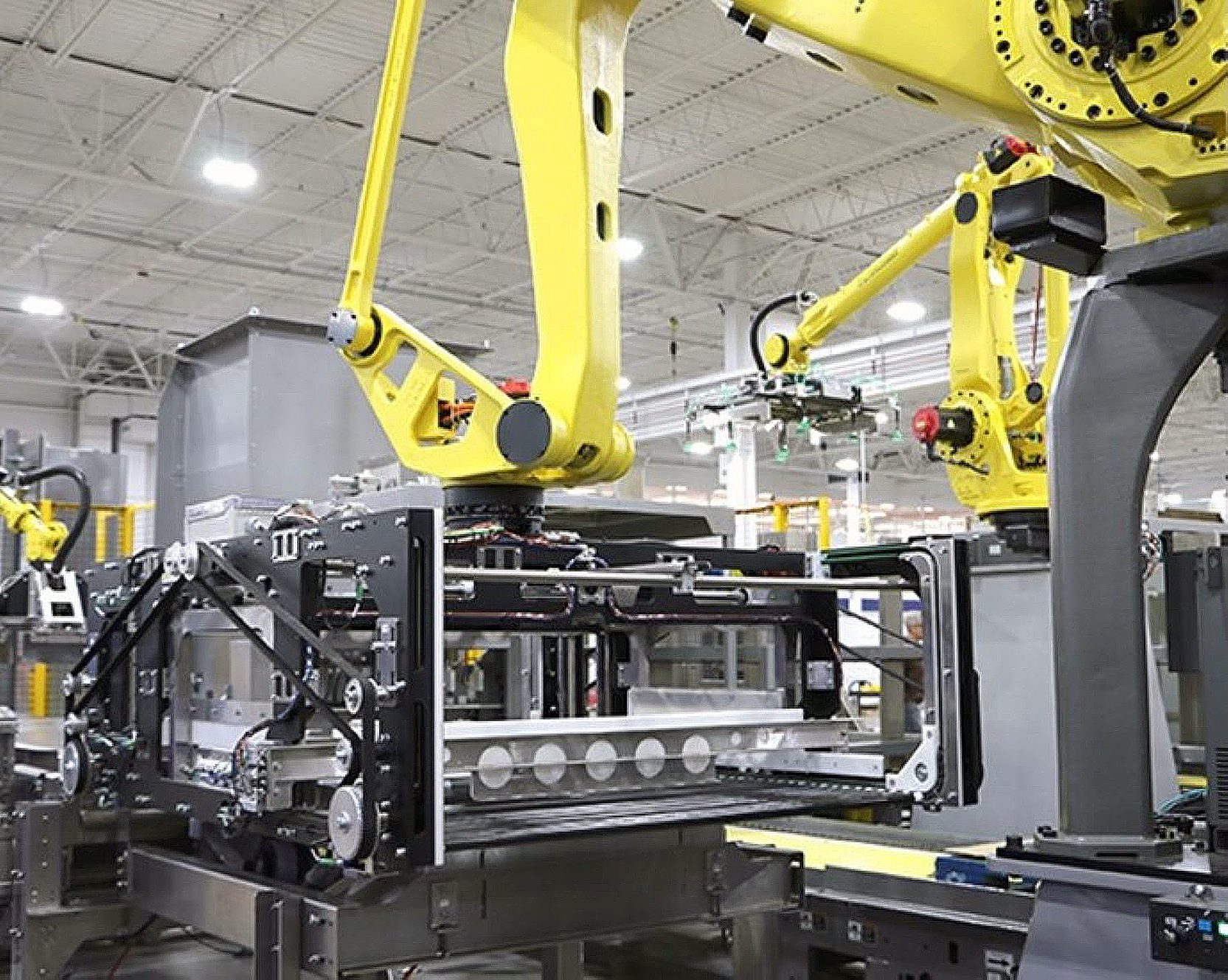
The Hartness High-Speed Layer Palletizing Tool was a key part of the licensing agreement.
Courtesy of Schneider Packaging Equipment Company
COLLAPSE ARTICLE ABOVE
Sidel, British Sugar Announce Partnership to Install End-of-Line Solution
Sidel has been appointed to install a highly flexible end-of-line turnkey solution for British Sugar, the leading producer of sugar for the British and Irish food and beverage markets.
The holistic and tailor-made solution will support the British company, a subsidiary of Associated British Foods plc that works with 2,300 growers, to meet market requirements as well as retailer expectations.
With increasing consumer demands and escalating sugar sales, British Sugar processes around 8 million tons of sugar beet to produce up to 1.2 million tons of sugar annually. The company required a large-scale operations replacement for its end-of-line system that was over 38 years old, including a brand-new solution with a high level of multiple SKU complexity management and automation.
READ MORE
To deliver a world-class product that is made to the highest standards, the company needed an extremely compact and flexible case packing and palletizing solution to be implemented within a tight plant area that would be capable of handling multiple pallet and format types to accommodate single sugar bags to new shelf-ready secondary packaging.
This strategic project represented a real technical challenge for British Sugar, which needed a reliable partner with the best technology. Following an extensive period of collaboration through discussion and design, British Sugar and Sidel shared a singular vision for the future end-of-line solution, with installation work commencing on what is the first partnership between both companies.
Case packer and palletizer flexibility, reliability and output speed were central to the desired end-of-line solution for British Sugar, with Sidel’s design and equipment focusing on achieving flexibility at a high-speed using advanced robotics. Sidel will deliver a full turnkey solution from sugar bagging outlet through to delivery at warehousing.
“We needed a partner with strong engineering and design expertise as the challenge was more complex due to the building constraints combined with our high level of technical specifications," explained James Warby, Project Integration Manager at British Sugar. “Sidel’s collaborative approach from the beginning was excellent. Their shared vision of a packaging line with our engineering team strengthened the trust we had in their capacity for delivering a turnkey solution and led us to decide to partner with them for this project.”
The breakthrough end-of-line solution will offer a highly efficient answer for future production management. Another phase of installation will be completed at the beginning of 2024.
Find out more about Sidel’s End of Line Solutions here.
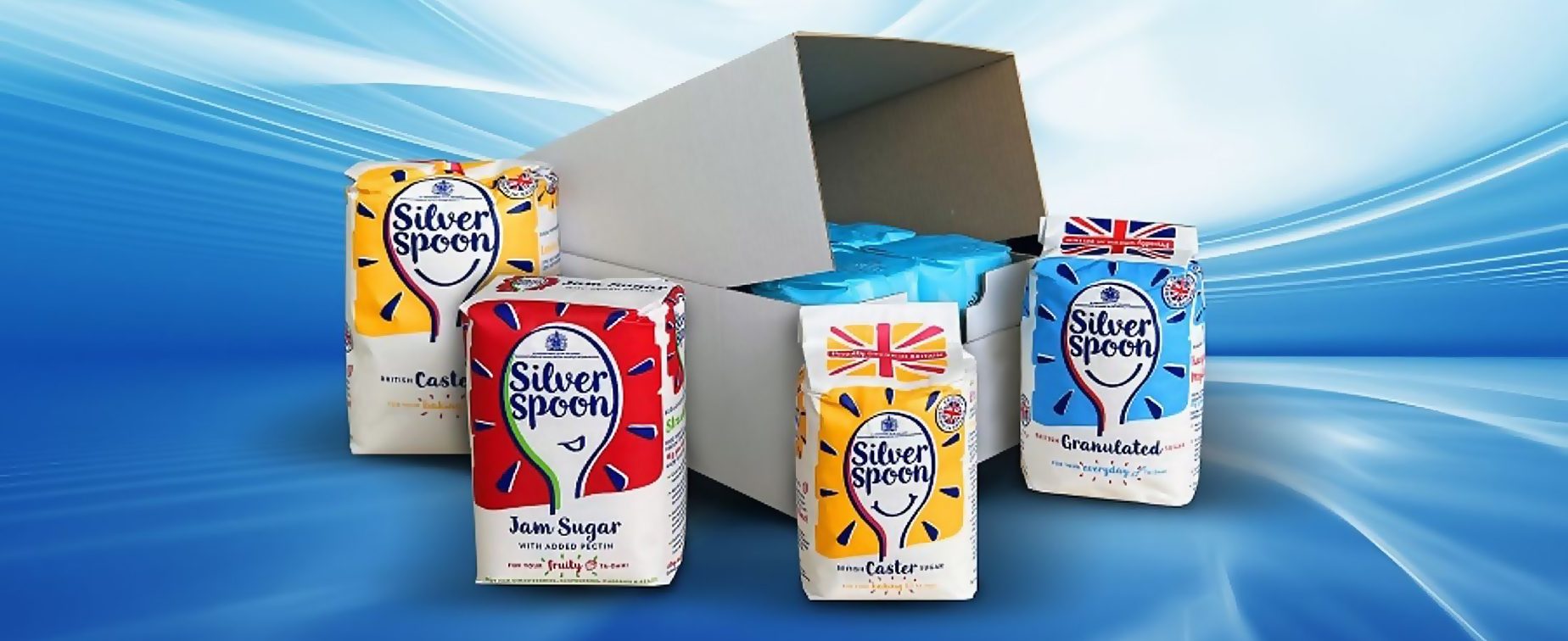
The solution will offer a highly efficient answer for future production management.
Courtesy of Sidel
COLLAPSE ARTICLE ABOVE
Piab Strengthens its Grip on Palletizing with the LBG-50
An unavoidable challenge when defining a new bag gripping system in a palletizing line is to get the exact measurements to align with the conveyor rollers for a smooth lifting and releasing process. This demands time-consuming analysis and design, and later, even more time for adaptation and adjustments.
Furthermore, additional solutions may have to be considered, e.g., for slip sheet handling, which prolongs the implementation process and may interfere with the original set-up and purpose of the gripper.
Piab's newborn in the palletizing tool family, lightweight bag gripper LBG-50, solves all that.
READ MORE
“LBG-50 is the result of our long experience from developing custom palletizing End-of-Arm-Tooling (EOAT)”, says Madeleine Sheikh, Product Manager at Piab Vacuum Automation Division. “What we have here is a complete pre-engineered bag gripper that is easy to install, adjust and maintain. It offers flexibility to fit any roller conveyor on the market, and slip sheets are handled just as easy by our vacuum-based upgrade option with Duraflex® suction cups and COAX® technology.”
Handling sacks normally poses a challenge as they are heavy and flexible, yet with a surface that is sensitive to pinching, puncture or rough treatment. LBG-50 avoids that by providing a gentle but firm lift while a built-in top clamp plate secures the bag from above during motion. This, in turn, allows higher cycle speed.
Both the arm and the framework of LBG-50 are made of aluminum, which makes it robust yet lightweight. Other positive features are flexible width and finger positioning and generous mounting options. Flexibility also goes for the valve package, which can be configured with either Discrete I/O, Ethernet/IP or Profinet.
To learn more about Piab, please visit piab.com.
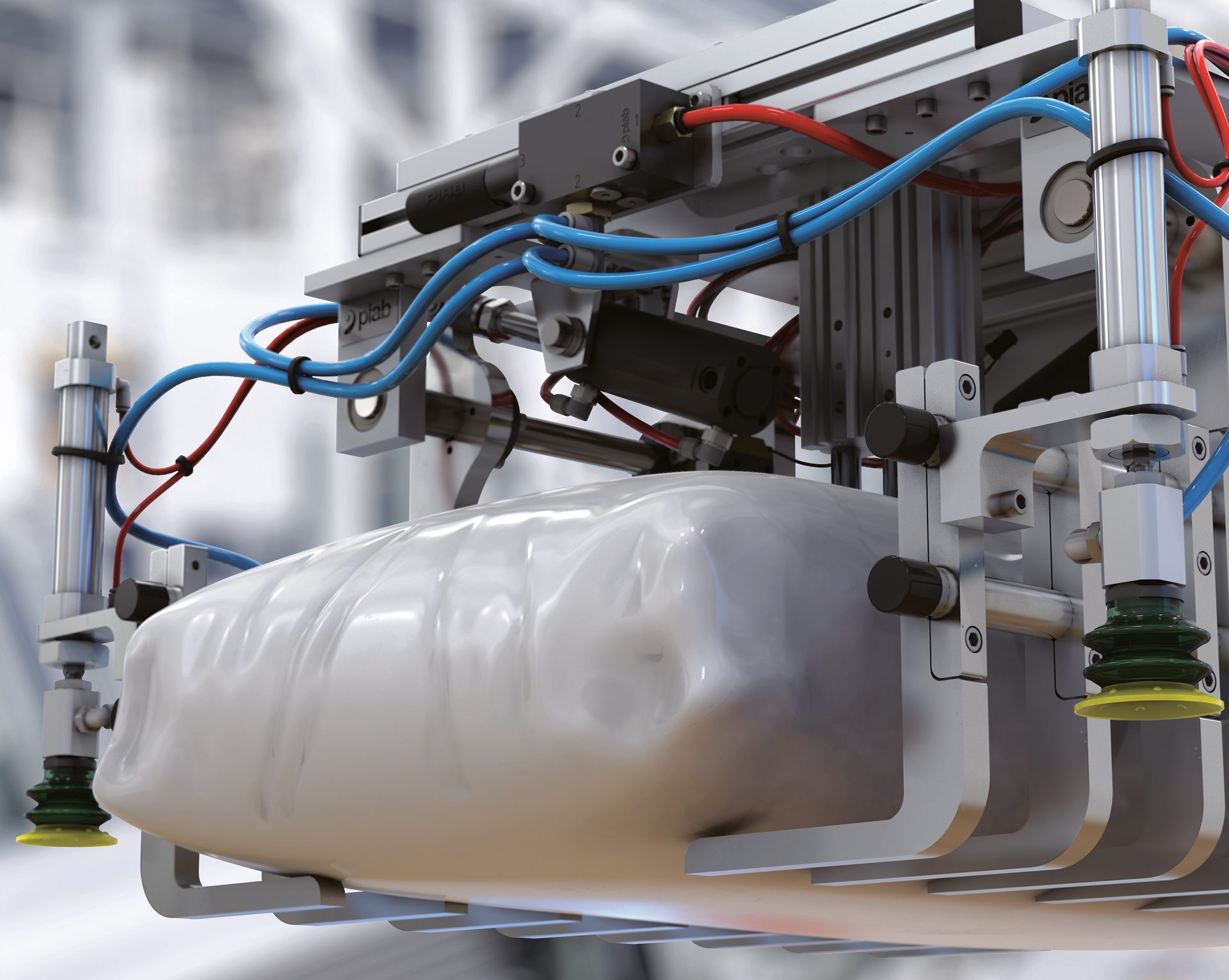