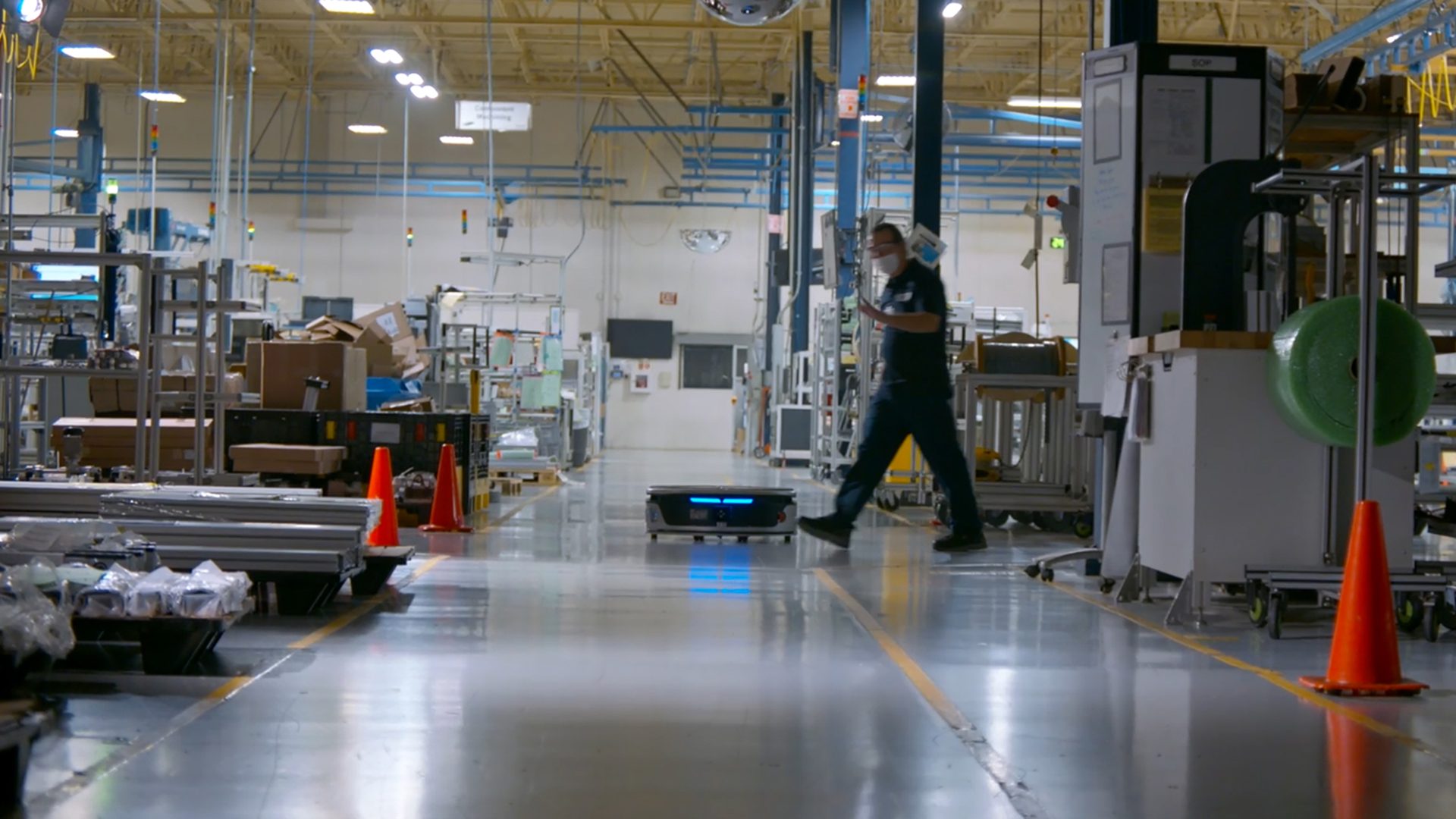
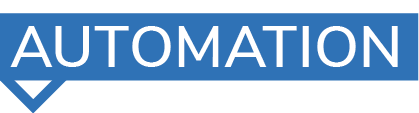
From Smart Valves to Smart Factories
Whether talking about a humble smart valve that can collect critical equipment data or a fully automated shop, the flexibility and scalability of automation make it possible for CPG firms of any size to benefit from the technology.
By Brad Addington
Three experts recently shared with Packaging Strategies their perspectives on how automation can improve the efficiency of packaging operations.
In his cleverly titled contribution “Optimizing Packaging Operations from Floor to Cloud,” Emerson’s Mark Densley talks about how such an approach can help with monitoring energy and other resource use, which is especially important as companies set net-zero goals and develop sustainability metrics.
ADVERTISEMENT
Komari America’s Doug Schardt explores the concept of the “Smart Factory,” which can be described as machines talking to machines and moving job information automatically between them. He notes that implementation of a Smart Factory can range from fully automated to partially automated, with both routes offering significant benefits.
Bosch Rexroth’s Armando Gonzalez also talks about movement between machines, but in this case the technology of focus is autonomous mobile robots (AMRs), which can significantly reduce the amount of time workers spending running around the shop.
Read below to delve into the scenarios laid out by these industry experts. While the common thread is automation, each approaches the subject from a fresh and unique angle.
Armando Gonzalez
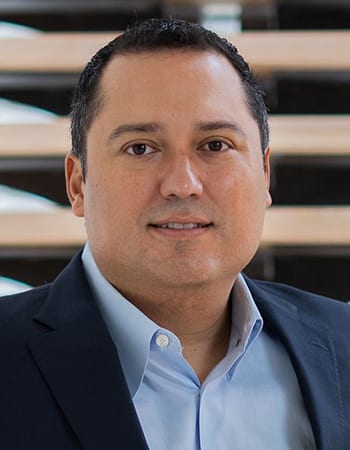
AMRs Move CPG Manufacturers into the Next Phase of Factory Automation
By Armando Gonzalez
Business Leader of AMR/Robotics for North America at Bosch Rexroth
Autonomous mobile robots (AMRs) are here to help revitalize the consumer-packaged goods (CPG) industry and help humans move their operations into the next phase of factory automation. As the industry enters this critical next stage of production efficiency, it’s critical to remember that humans remain the key to making mobile robots successful in manufacturing facilities, warehouses and distribution centers.
The adoption of mobile robotics is just starting — with the manufacturing industry at a 10% adoption rate. Especially in tightly margined industries like CPG, industry leaders are looking into mobile robotics technology to evaluate how it can benefit their current workforce, improve their production processes and help them expand their operations. Preparing production workflows for the introduction of robots is critical for advancing automated operations and helping ensure successful workflows. As mobile robotics shows its benefits and more manufacturing leaders start moving toward implementing fleets, the adoption rate for mobile robotics in CPG manufacturing workflows will likely start to increase.
READ MORE
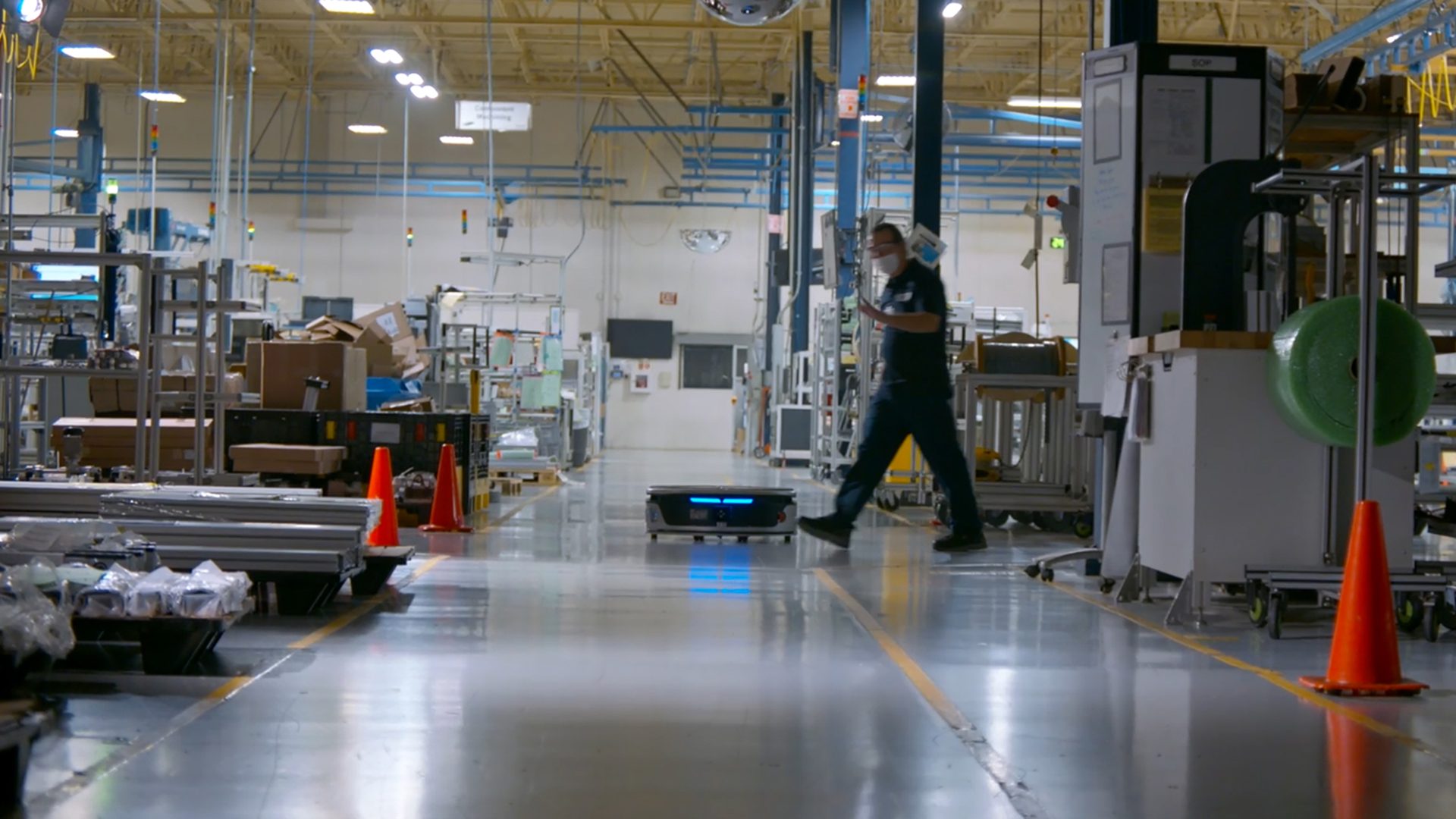
Helping lead the way to greater productivity, autonomous mobile robots (AMRs) play a critical role in not only reducing the strain on human workers and freeing up their time for value-added tasks, but also creating a safer work environment.
Section photos courtesy of Bosch Rexroth
How Autonomous Mobile Robots Benefit CPG Production
Safety is, and always will be, a major concern within manufacturers across industries, including CPG. Improving worker safety is the one of largest benefits AMRs provide for its user. For example, there were at least 80 fatalities associated with forklift usage in 2020. In just one year, it’s estimated there are approximately 7,000 accidents reported in a facility. Safety initiatives are paramount to not only keeping the workforce protected, but to keep production steady and competitive with the market. AMRs can eliminate historically dangerous equipment such as forklifts that simply need to carry large payloads, such as pallets of finished product, from one end of a facility to another, allowing the driver to work on higher-value tasks while keeping processes flowing smoothly.
AMRs also play a large role in reducing strenuous activities and repetitive tasks from human workers during material handling workflows. This is critical for helping CPG leaders to redirect their labor pool to spend their time on value-added tasks that robotics can’t complete. Especially in industries with tighter labor markets, if a worker needs to maximize their time during a shift, mobile robots can take on those repetitive mundane tasks. Even if it’s just a 5-minute session to walk across the warehouse, that time can add up quickly throughout a single shift. This is where AMRs can help eliminate wasted worker time, and when multiplied over shifts, CPG companies can experience some good productivity gains.
In summary, the impact of autonomous mobile robotics technology is augmenting what people do, rather than replacing people.
CPG Companies Gain Competitive Advantage with Autonomous Mobile Robots
CPG companies are always looking for more innovative ways to get more out of their production process to meet aggressive throughputs and keep up with industry demands. This challenge isn’t exclusive to Fortune 500 companies – even smaller family-owned operations are exploring new technology to help them fulfill contracts competitively. And, especially with a competitive labor market, they’re looking to advanced technology to help augment some of the worker tasks on a day-to-day basis.
Integrating AMRs into workflows is an excellent fit because they are designed to help improve material movement efficiency and worker safety in intralogistics applications, without additional infrastructure. A mobile robot with a compact design will be the ideal fit for CPG applications, allowing it to navigate the tight spaces that often challenge CPG warehouses.
Integrate Autonomous Mobile Robots into Cohesive CPG Factory Automation Workflows
Imagine this scenario — you’re a CPG company who wants to automate multiple stages of your production process. You’ve set up a workflow so that product travels down a pallet-based conveyor line built on an aluminum framing base, powered by automated drives and controls and outfitted with Cartesian robots for handling the product as it moves through the various stages of the line. Once the product has completed one automated workflow, it will need to be transferred to the next. Rather than having a worker run product back and forth throughout the day, an AMR can be integrated into the workflow to keep processes running smoothly.
Ultimately, it’s important to remember that an AMR is most effective for CPG companies when it integrates into a comprehensive factory automation system. Autonomous mobile robots, such as the MP1000R, compliment other key factory automation solutions including conveyors, aluminum framing, linear motion systems, and more. It’s not just an AMR. It’s one component of a complete automation ecosystem that is engineered for maximum productivity.
COLLAPSE ARTICLE ABOVE
Mark Densley
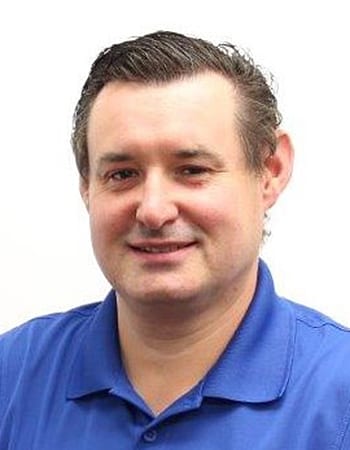
Optimizing Packaging Operations from Floor to Cloud
By Mark Densley
Director of Business Development for Factory Automation, Emerson
Consumer packaged goods (CPG) companies face competing pressures. While customer demand continues to grow, so do skills gaps and labor shortages. As companies focus on sustainability, they must maintain high productivity. To remain competitive in a global market, it’s critical that CPGs excel in all these areas at once.
Although it seems like these challenges require different solutions, there’s one solution that addresses them all — digital transformation. Smart valves and sensors collect critical asset data; smart protocol convertors release trapped machine data from existing controllers and across the packaging floor. Innovative software translates new and released data into valuable insights and machine health information that is scaled in the cloud. By integrating intelligent floor-to-cloud solutions that automate and optimize packaging processes, CPGs can simultaneously improve sustainability, efficiency and productivity.
READ MORE
Go Greener: Minimize Energy and Resource Consumption
Many companies have set net-zero goals and implemented sustainability strategies. Yet, they may have little information about how much energy and resources their processes use. By unlocking real-time energy and resource consumption, CPGs can reliably reach net-zero initiatives and reduce environmental impact.
A floor-to-cloud solution monitors energy and other resource use and visualizes consumption as well as machine health and process efficiency via equipment- or facility-level visualization. Operators can track usage over time and harness up-to-date information to make decisions that optimize use. The system can also send alerts to specified personnel when issues arise and generate automated environmental reports to satisfy regulations.
Companies can manage and optimize the consumption of utilities such as air, water, steam, gases, chemicals and electricity. Given the prevalence of pneumatic systems in packaging lines, compressed air monitoring is an effective starting point that provides quick return on investment (ROI). Typical facilities lose about 30% of their compressed air to leaks. Smart pneumatic sensors continuously monitor compressed air flow and make it possible to detect leaks in real time and address them in their early stages. This can reduce compressed air consumption and related emissions by 20-30%.
Go Leaner: Optimize Machines, Processes and Workforce
The skills gap and labor shortage stretch existing staff thin and can make it difficult for them to successfully complete their responsibilities. This includes ensuring machines operate effectively. Floor-to-cloud packaging solutions can automate time-consuming manual processes and equip teams with the knowledge they need to make smart, fast decisions that optimize equipment.
Many CPGs check for equipment issues by having staff travel from machine to machine, which takes considerable time and labor cost. Continuous monitoring and analytics allow operators to see machine health and diagnostics on a single dashboard in real time and receive alerts as issues start to manifest. By addressing issues in their early stages, CPGs can practice preventive maintenance that prevents failures, reduces unplanned downtime and improves overall equipment effectiveness (OEE).
Consider compressed air monitoring. Periodic, manual leak testing costs an average of $46,000 per machine per year, and only provide data the day they are completed. In comparison, smart pneumatic sensors continually monitor compressed air in pneumatic systems. When they detect a leak, specified personnel receive a detailed notification about what to check and do.
Go Greater: Maximize Packaging Productivity
When CPGs optimize their packaging equipment, they optimize their packaging processes. Running packaging machines to failure results in expensive, unplanned downtime and, depending on product lifespan, potential product loss or quality issues. By using real-time machine health and process data, CPGs can continuously improve OEE, keep machines running in peak condition and make informed decisions that make processes more efficient.
It’s important to note that the flexibility and scalability of floor-to-cloud solutions make it possible for CPGs of any size and stage of digital transformation to optimize packaging operations. CPGs can start with one machine, line or facility and prove ROI, starting small and scaling fast.
To identify key areas of opportunity, collaborate with an automation provider with a comprehensive portfolio of devices, hardware and analytics software. They can help develop and apply a complete solution that addresses a CPG’s specific goals and challenges.
Drive Continuous Improvement
A floor-to-cloud approach to packaging automation gives manufacturers real-time visibility and control that optimize packaging operations from multiple directions. By accessing trapped data and using those insights, manufacturers can increase machine availability, reduce energy and resource waste, improve OEE and reach their most ambitious goals.
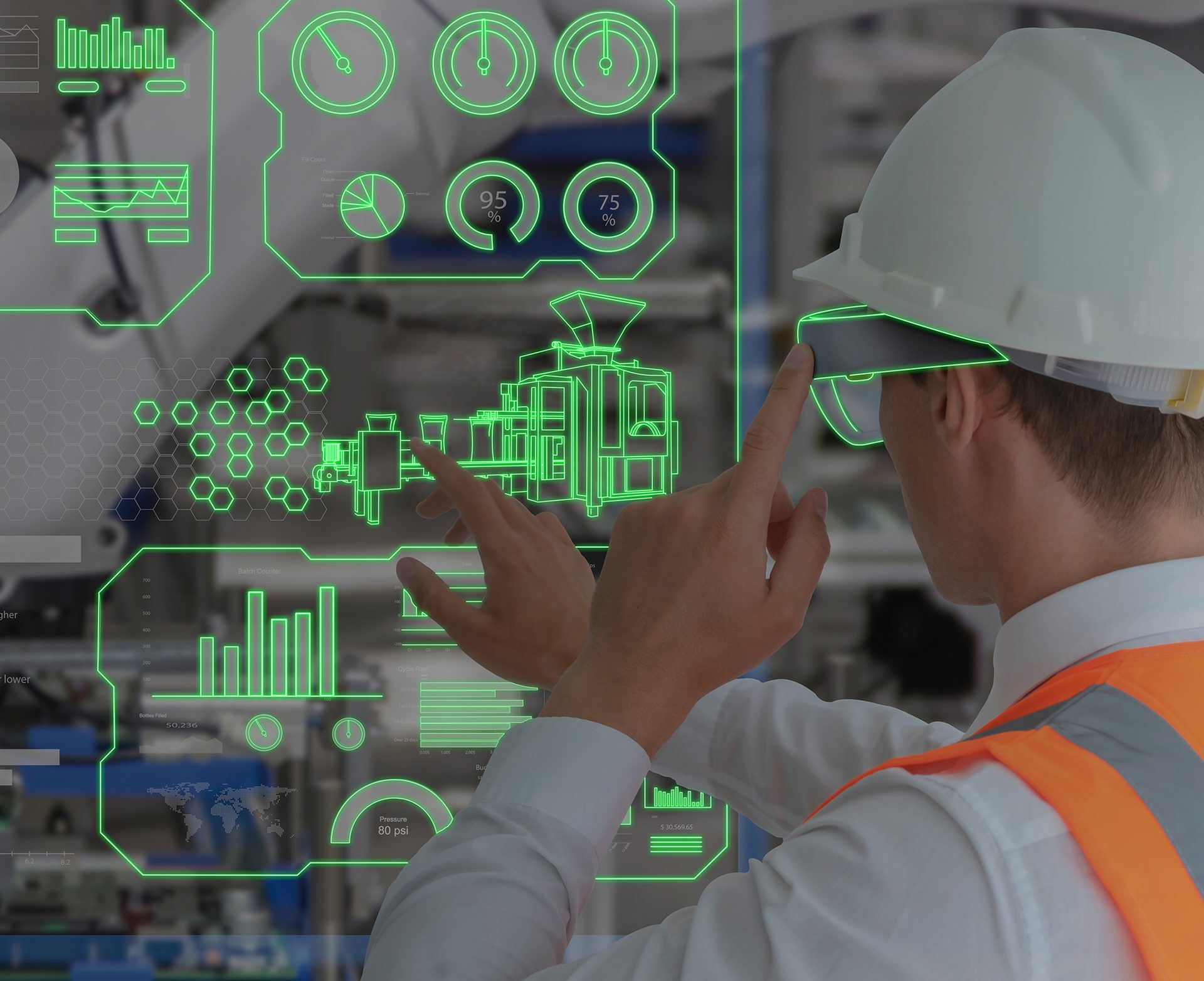
CPG firms can quickly solve complex packaging issues and improve overall packaging efficiency using industrial software such as Movicon.NExT™ HMI/SCADA.
Section photos courtesy of Emerson
COLLAPSE ARTICLE ABOVE
Doug Schardt
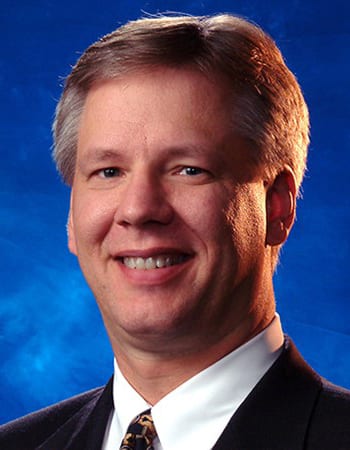
The ‘Smart Factory’ and Package Printing Automation
By Doug Schardt
Director of Product Management for Komori America
Packaging printers are continually in search of productive processes that use less labor to meet the needs of their customers. The hands-on methods required by package printing press operators in the past have become troublesome in this growing business environment. Removing the operator’s tweaking of the controls and allowing the machines to optimize process control and automation technology in the way they were intended improves efficiency.
Press automation is comprehensive enough to allow the entire print process, from makeready to run to washup, to move automatically through all the scheduled jobs with limited human interaction. This has proven so beneficial that it is natural to imagine the benefits of automation extending to all machines in the package print production process. This is the concept of a “Smart Factory” — which can be described as machines talking to machines and moving job information automatically between them as the print job progresses through the shop.
READ MORE
The idea of a Smart Factory is still being refined, but it’s the natural direction of automation growth. The intent is to automate the entire production plant, rather than just the printing press or any other single machine working within the shop. This concept requires electronic tracking and communication between machines and management. As machines do their part in production, management can electronically monitor job performance compared to expectations.
Implementation of a Smart Factory can range from fully automated to partially automated with both scenarios offering significant benefits. Any time the number of touch points of a print job are reduced, the quality, productivity and efficiency tend to rise, which also cuts costs and allows package printers to meet increasingly aggressive delivery timelines.
A Smart Factory can also compensate for the decline in the number of skilled workers by reducing or eliminating the need for in-depth knowledge of machine operation, since information is communicated to the equipment electronically. This type of automation delivers complete transparency of a plant’s operation to management with real-time visibility into overall workflow, as well as individual jobs. If a problem does occur anywhere in the process, it can quickly be detected and remedial action can be taken to minimize the impact on further production.
How a Smart Factory Works
The idea of machines talking to machines is somewhat reminiscent of JDF (Job Definition Format) that was popular a few years ago; however, Smart Factory is a little different. JDF used very simple job specifications so that even primitive machines could communicate. As a result, more complex job specifications had to be manually entered into more sophisticated equipment. In contrast, Smart Factory will likely employ the same specific instructions, simple or complex, that would normally be used to set up a machine without Smart Factory.
Presently, machines are already communicating with each other, but on a limited basis. For example, prepress may receive information from a print management information system (MIS) and pass electronic information to the press, which in turn generates its own information about production and quality. On the other hand, in a true Smart Factory, the press would convey the necessary information to the equipment used for the next step of processing, as well as generating its own production/quality report. Any errors or delays could be viewed in real time by management with the use of automatic alerts.
To switch from the Smart Factory concept to a practical application, consider the following example. Let’s say a press completes a run and information flows, in this case, to a paper cutter. The paper cutter would then implement the correct cutting program and be ready for automated operation. Here is where a speed bump is likely to occur when older equipment is involved: The paper cutter must be able to receive and react to electronic data. There are a lot of existing paper cutters that don’t have that ability and, until they are replaced, a workaround must occur. This could take the form of a computer monitor mounted next to the cutter (or other equipment in the process) that will tell the cutter operator what is required for the cutting program. The operator will then program the cutter and begin the job. This would be considered a partially automated version of Smart Factory.
There is no doubt that the concept of Smart Factory has the potential to convert what is typically a customized workflow into a reliable manufacturing process driven by data. Combining Smart Factory with logistics to automatically move the physical product from machine to machine, along with the electronic data, promises to truly automate the entire plant. This will positively impact overall profitability while simultaneously reducing the impact of hard-to-find skilled labor. While the rewards of a Smart Factory can be great, a company must be willing either to replace older, non-compliant equipment when compliant equipment becomes available or to accept a suitable workaround in the interim. Smart Factory is a strong concept for the future of automation and is something for printers to consider and plan for as they look toward upcoming equipment purchases and upgrades.
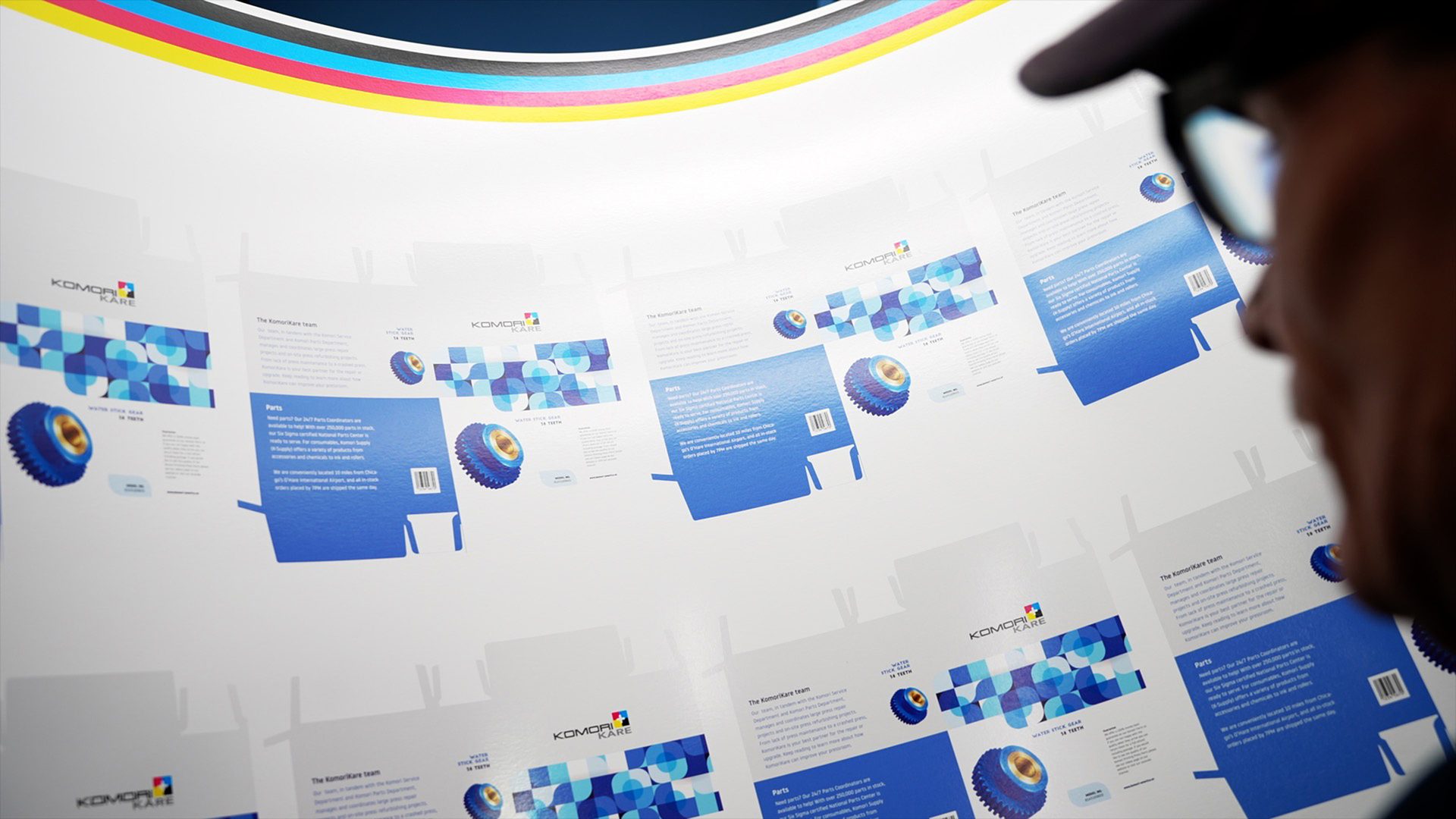