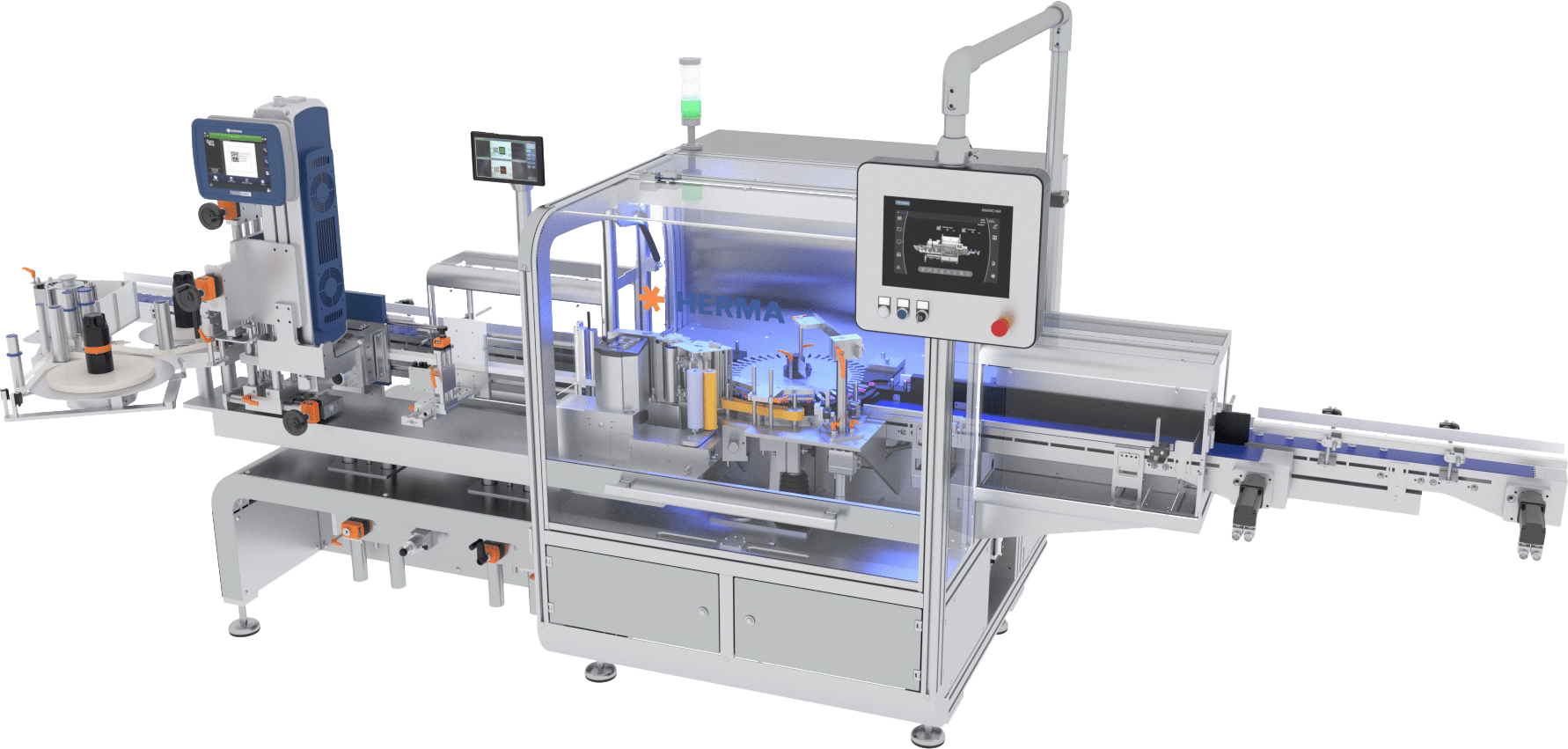

IMPROVEMENT AND INNOVATION
Labeling and blister packaging have made significant leaps when it comes to the pharma and medical sector.
With the pharma and medical sector continuing to be a robust market for the packaging industry, forward-thinking solutions have come in a variety of areas throughout the packaging process, with the most notable innovations coming in two key components: labeling and blister packaging.
- When it comes to labeling, HERMA US Inc. unveiled a new and improved machine at PACK EXPO Las Vegas designed for the streamlined labeling of vials and cylindrical containers.
- For the actual labels themselves, Schreiner MediPharm recently showcased a new protective syringe label suitable for deep freeze applications with protective capabilities for sub-zero temperatures.
- With blister packaging, Maruho Hatsujyo Innovations (MHI) introduced the Eagle-LP at PACK EXPO Las Vegas, a machine designed for small batch production and stability testing.
- And finally, Solvay introduced a finishing touch for blister packages by developing a new polyvinylidene chloride (PVDC) coating solution with an ultra-high water vapor barrier that allows for a significant carbon footprint reduction.
Read more about these solutions in the pharma and medical sector below.
ADVERTISEMENT
HERMA US Inc. Debuts Improved Labeling Machine at PACK EXPO Las Vegas
HERMA US Inc., the subsidiary of HERMA GmbH – a Germany-based provider of labeling machinery and self-adhesive labels and materials to the global packaging marketplace – debuted an updated, streamlined configuration for one of its flagship high-speed labeling machines at PACK EXPO Las Vegas in September. Faster and more aligned with the needs of evolving pharma production lines, the company’s reimagined 132M HC Wraparound Labeler includes a sophisticated yet simplified new touchscreen HMI to coincide with improved ergonomics and an output ceiling of 600 products per minute – a 50% uptick over the previous model.
READ MORE
The improved machine has an output ceiling of 600 products per minute.
Courtesy of HERMA US Inc.
Designed for vials from 2ml upwards and any cylindrical container up to 90 mm in diameter, HERMA’s 132M HC Wraparound Labeler offers 24/7 operation and the robustness demanded by the sector’s inherent high batch sizes. Featuring fast, tool-free changeover and electronic position indicators, the unit combines rapid labeling speeds with exacting precision via the company’s high-performance HERMA 500 label applicator.
For HERMA, the reconfiguration of one of the 132M is part of a series of improvements to its machinery range from both an operational and ergonomic perspective. Dubbed ‘Clean Design,’ the extensive use of stainless steel ensures compliance with the strict GMP hygiene requirements in the pharmaceutical industry.
To learn more about HERMA GmbH, please visit herma.us.
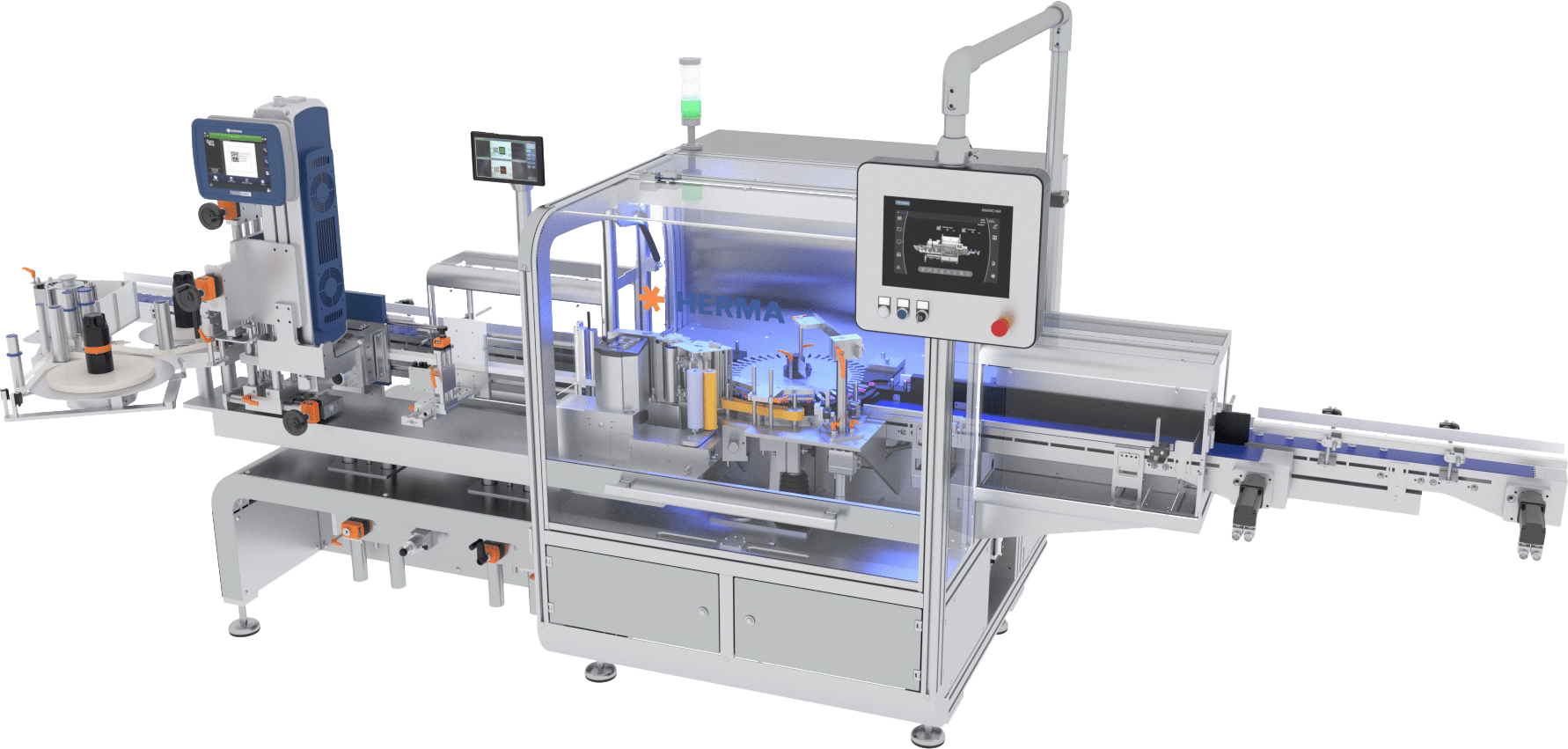
COLLAPSE ARTICLE ABOVE
Schreiner MediPharm Introduces Freeze-Light-Protect Label
Schreiner MediPharm, a Germany-based global provider of innovative functional label solutions for the healthcare industry, showcased a new protective syringe label suitable for deep-freeze applications at PDA Universe of Pre-Filled Syringes & Injection Devices last October. Schreiner MediPharm introduced its Freeze-Light-Protect syringe label, which combines light protection with viability at temperatures well below zero. The new solution is particularly relevant for sensitive mRNA-based substances as well as cell and gene therapies.
READ MORE
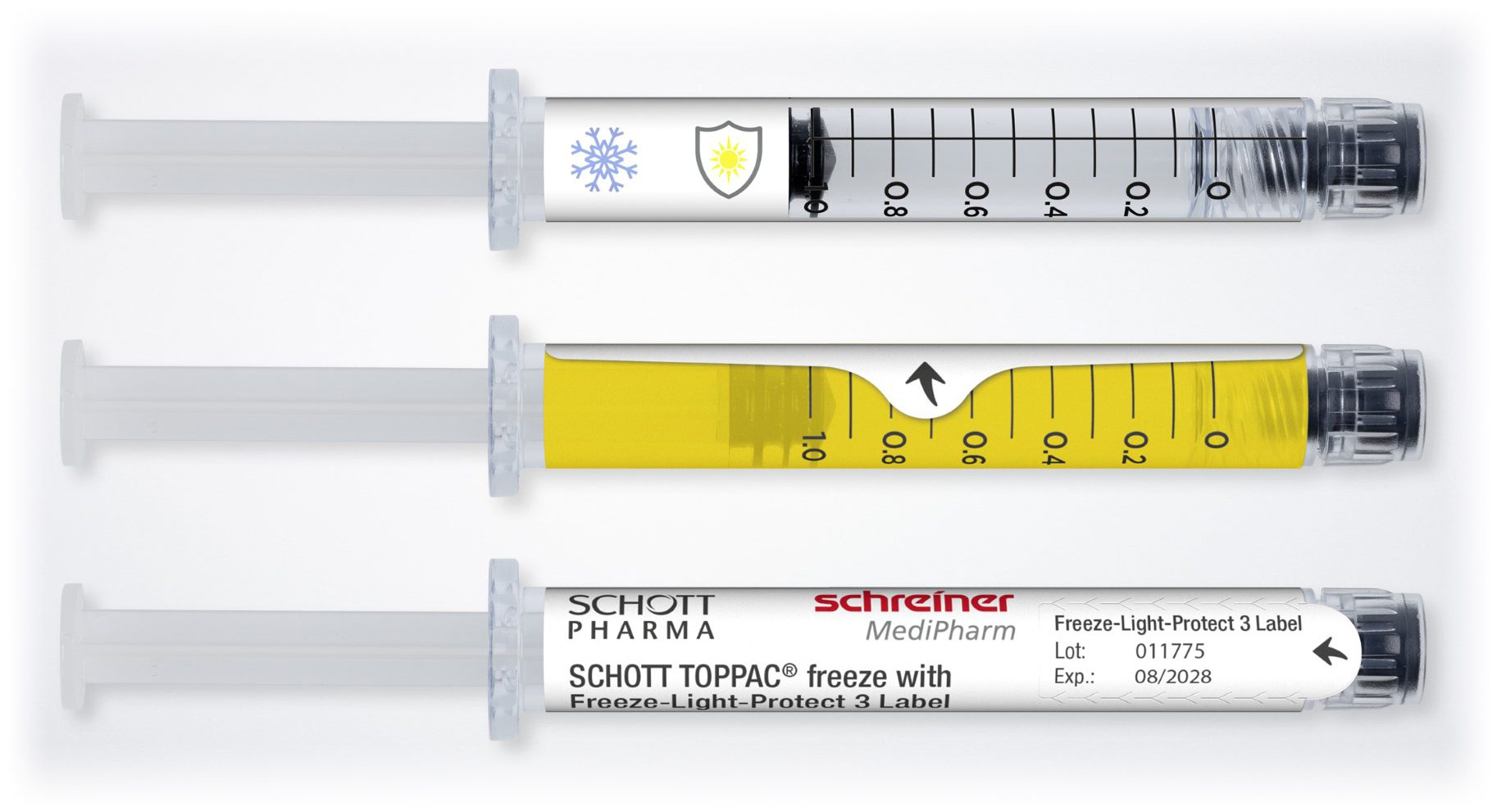
The labels can remain attached to syringes at temperatures as low as -100 °C.
Courtesy of Schreiner MediPharm
Therapies and vaccines with mRNA substances, as well as cell and gene therapies, are becoming increasingly prevalent. These novel active ingredients entail special logistical challenges. For starters, they must be transported and stored on dry ice at freezing temperatures as low as -100 °C. In addition, special light protection is frequently required, depending on the type of substance. Precisely for these applications, Schreiner MediPharm has developed the Freeze-Light-Protect syringe label.
Freeze-Light-Protect securely adheres to the syringe despite extremely low temperatures, enabling reliable marking. The specialty label also can be enhanced with a variety of UV and light protection levels. The first level provides UV protection exclusively, while a second protects against UV rays and blue light. A third level delivers comprehensive light protection. Light protection levels can be exactly customized to suit the specific requirements of the active ingredient. Additional integrated functionalities also are available, including detachable documentation labels for vaccination cards or patients’ medical records; inspection windows for checking syringe contents in unadulterated color; and graduations for correct dosing of injections.
The novel label from Schreiner MediPharm was developed in coordination with its partner SCHOTT Pharma, which launched the SCHOTT TOPPAC® freeze syringe. The 1 ml long COC syringe was developed for medicines with temperatures down to 100 °C, with a view to retaining the syringe’s functionality and integrity of the syringe closure, thus securing drug stability. Schreiner MediPharm’s Freeze-Light-Protect was tested specifically for the SCHOTT TOPPAC® freeze syringe to prove the reliability of the label-integrated protective functions and other features.
To learn more about Schreiner MediPharm, please visit schreiner-group.com.
COLLAPSE ARTICLE ABOVE
MHI Showcases Small-Batch Blister Machine at PACK EXPO Las Vegas
Maruho Hatsujyo Innovations (MHI) — the U.S. subsidiary of Maruho Hatsujyo Kogyo Co. Ltd, a Japanese company with subsidiaries in Asia and the U.S., recently showcased a blister machine specifically intended for stability testing and similar small-run applications at PACK EXPO Las Vegas. The Eagle-LP — short for “Lab Pack” — joins the company’s extensive blister packaging equipment family as a reliable, cost-effective solution for development stages, stability testing and initial small-batch production.
READ MORE

MHI’s Eagle-LP for small batch blister packaging production.
Courtesy of Maruho Hatsujyo Innovations
The Eagle-LP addresses two longstanding challenges in early-stage blister packaging: affordability and floorspace. Many pharma manufacturers have faced challenges finding blister units for stability testing, clinical trials and small batch runs that aren’t onerously expensive and unnecessarily lengthy or bulky. The modestly priced Eagle-LP measures just 1.8 meters in both length and height, and just 0.9 meters in width.
Importantly, the Eagle-LP also is designed to accommodate a newer generation of more sustainable blister film substrates – ones that are typically more difficult to form and seal. The unit can easily accommodate PVC, PVDC, PET, ACLAR, ALU and PP.
The Eagle-LP can run up to 20 cycles per minute, with a blister format area of 110 X 60mm and a maximum blister depth of 20mm. It can handle forming materials up to 320mm in diameter, and lidding materials up to 220mm in diameter. The unit is capable of both thermoforming and cold foil forming.
“Researcher and product development professionals can benefit significantly from a blister machine designed specifically to suit their needs,” said Harry Yonenaga, President of the Medical Packaging Machinery Division for Maruho Hatsujyo Innovations, and a project leader for the Eagle-LP’s development. “Too often, early-stage teams are left choosing among inadequate options, including purchasing large, expensive equipment or interrupting mass production machinery, which limits output capacity elsewhere. The Eagle-LP gives R&D the special considerations it deserves.”
To learn more about MHI, please visit mhi-innovations.com.
COLLAPSE ARTICLE ABOVE
Solvay Introduces New PVDC Coating Solution for Pharmaceutical Blister Films
Solvay, a global market leader in specialty materials, has introduced Diofan® Ultra736, a new polyvinylidene chloride (PVDC) coating solution with ultra-high water vapor barrier that allows carbon footprint reduction for pharmaceutical blister films. As an aqueous dispersion, Diofan® Ultra736 is fluorine-free, meets regulatory requirements for direct pharmaceutical contact and supports the design of sustainable films with thinner coating designs.
READ MORE
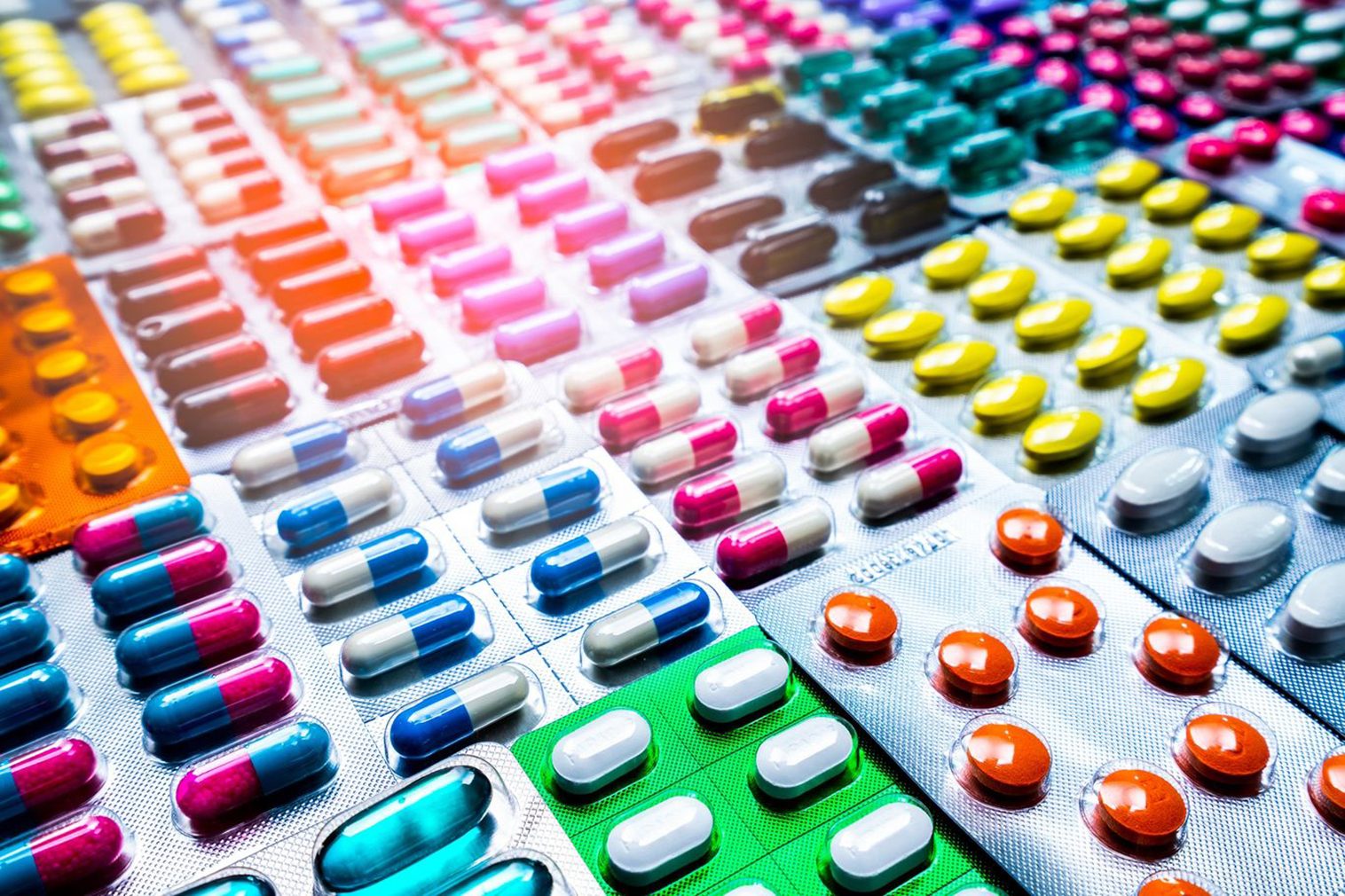
Diofan® Ultra736 can be used on both plastic and paper-based substrates.
Courtesy of Solvay
X“Consumers and legislators are requesting increased efforts related to carbon footprint reduction from the packaging industry, and one of the most effective means to this end is to reduce the size and weight of packaging products,” says Federico Baruffi, Global Marketing Manager, Packaging, Solvay Specialty Polymers. “Our new Diofan® Ultra736 coating solution can help packaging film manufacturers achieve superior barrier properties with thinner structures, leading to a significant carbon footprint reduction of the blister film.”
Diofan® PVDC coatings are widely used in pharmaceutical blister packaging to protect sensitive solid-dose drug preparations as well as in the packaging of delicate food and similar other consumer goods. They can be applied on both plastic and paper-based substrates and are often preferred for their unique combination of water vapor and oxygen barrier.
Diofan® Ultra736 PVDC coating was custom-engineered to maximize the water vapor barrier without sacrificing its high oxygen barrier, chemical resistance or transparency. The product also exhibits excellent thermoformability, enabling smaller pack sizes with higher pill density if compared with incumbent alternative coating solutions.
Thanks to its ultra-high barrier performance, Diofan® Ultra736 allows the reduction of the coating thickness compared to incumbent mid to high barrier PVDC coatings, without impacting the functionality. In particular, it has been shown that, for Duplex barrier structures, Diofan® Ultra736 enables halving the number of base coat layers while delivering the same water vapor barrier. This approach can contribute to decreasing the overall carbon footprint of final blister film structures by up to 13%.
To learn more about Solvay, please visit solvay.com.