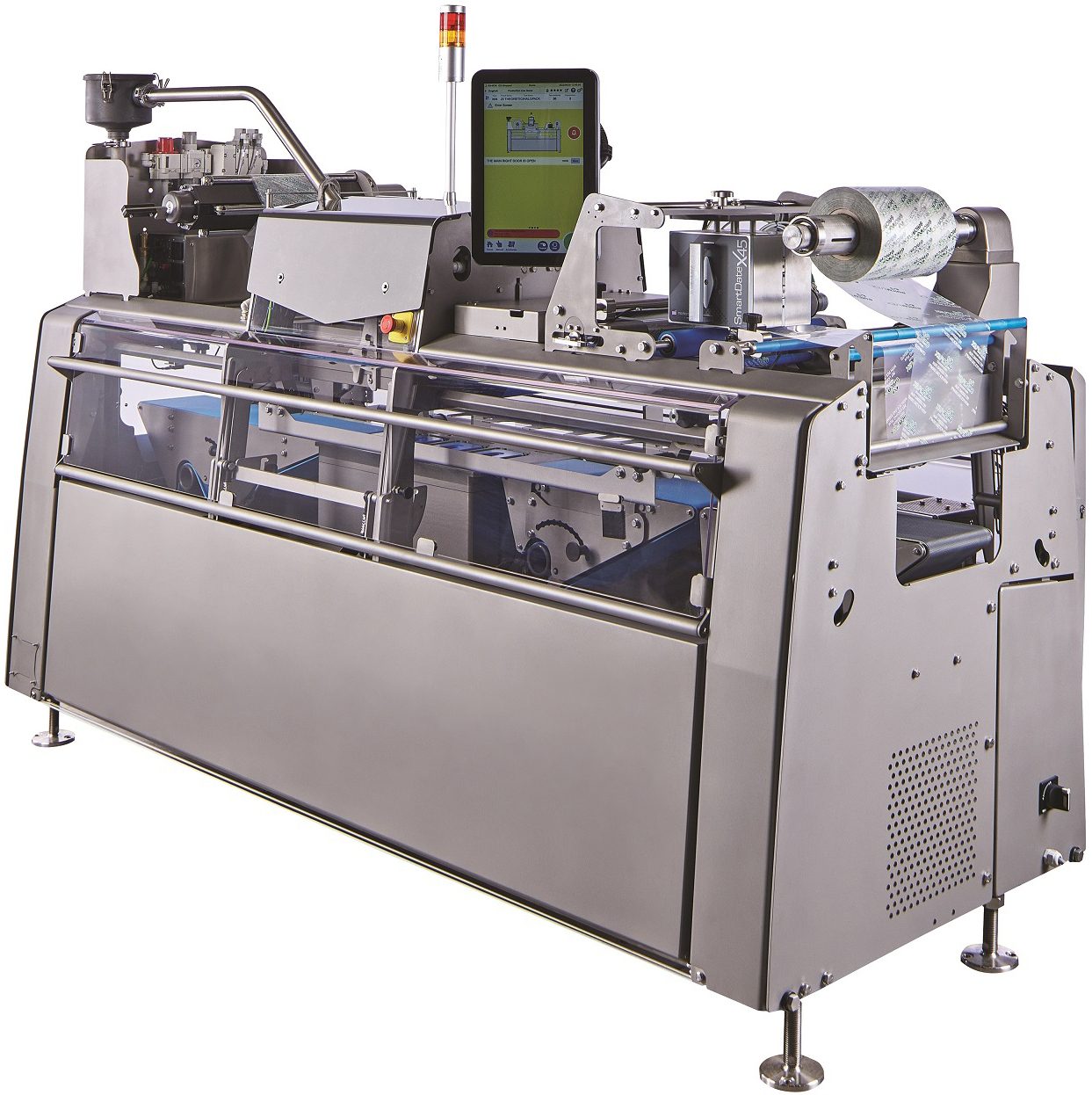

Top Stories of Fall 2023
In this article, we share some of our top picks for the most intriguing developments in sustainable packaging announced in September and October.
Companies throughout the packaging industry are adopting their own unique approaches to offering products that are more eco-friendly.
While companies are charting distinct paths to meeting their sustainability pledges, some initiatives fall under broader categories. Such strategies include: using novel materials (e.g., bioplastics); reducing the energy consumption of the packaging equipment itself; utilizing postconsumer recycled material and offering packaging that is 100% recyclable; moving from multi-material packaging to mono-material packaging; and addressing the challenges that can arise when new eco-friendly materials are used in traditional packaging equipment.
What the companies featured here have in common is that they are not adopting any single strategy but rather are taking a multi-pronged approach to achieving sustainability. Read more about these leaders in innovation and their contributions to circular infrastructure and — through various means — a generally more eco-friendly packaging landscape.
ADVERTISEMENT
Ishida’s game-changing tray sealer garners recognition with PPMA award
The high performance and sustainability benefits of Ishida’s recently introduced QX-500 tray sealer have been recognized by the winning of a prestigious award.
The Ishida QX-500 won the Innovative Packaging Machinery category at this year's PPMA Awards, which celebrate the very best in UK packaging equipment design and manufacturing. The Innovative Packaging Machinery award recognizes companies that have engineered or adopted a solution that has led to significant productivity improvement and/or cost reduction.
One of the most significant aspects of the Ishida QX-500’s development is that the tray sealer was created as a direct result of feedback from the company’s global customers and partners. This identified the need for a compact tray sealer that can fit easily into new and existing packing lines, offers excellent seal quality and high throughput and at the same time helps companies to meet their sustainability targets.
READ MORE
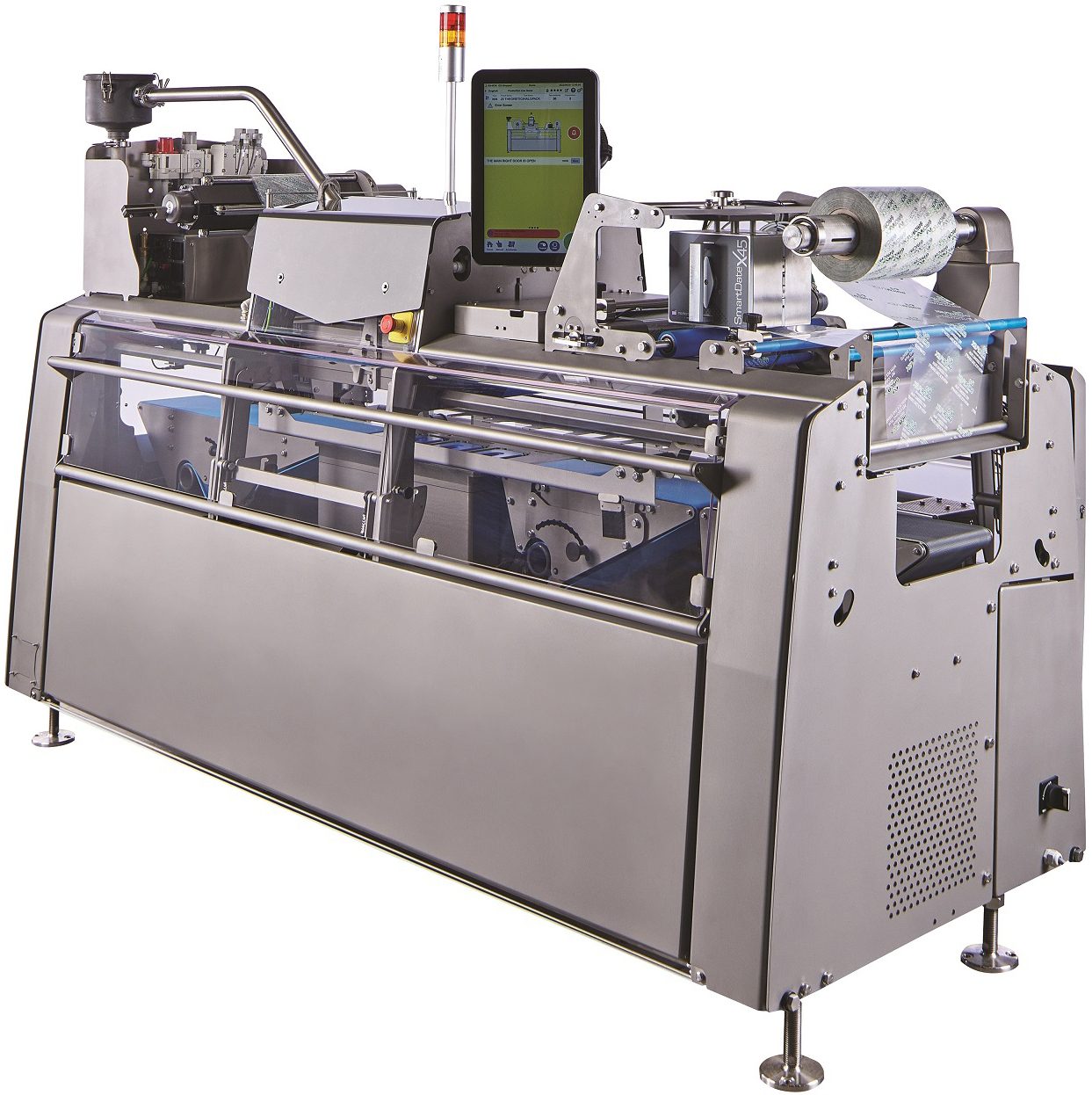
The Ishida QX-500 tray sealer delivers a 66% increase in cycle speed, a 44% reduction in weight, a 46% reduction in size and a 50% reduction in energy consumption.
Courtesy of Ishida
The QX-500 delivers a 66% increase in cycle speed, a 44% reduction in weight, a 46% reduction in size and a 50% reduction in energy consumption. This means the new tray sealer delivers consistently high-quality seals, significantly reduces waste and delivers a step change in productivity.
To meet the different requirements of products and pack formats, the tray sealer offers a variety of sealing options — seal only, gas flushing, MAP, stretch film and skinpack — across a wide variety of tray designs and materials, including plastic, board and recyclable formats. The QX-500 is also available with integrated film coding, gas mixing and integrated vacuum system.
With customers identifying available factory space as a major challenge, the design of the QX-500 focused on driving down the size and weight of all major sub-systems of the tray sealer to deliver high performance using a minimum machine footprint. This allows companies to realize a high ROI on often limited floor space.
Alongside this, each component of the machine was individually assessed to calculate its carbon footprint and, where appropriate, alternative materials selected to reduce environmental impact. The use of highly efficient servo motor technology minimizes energy consumption and cost of operation, and the QX-500 monitors its power consumption during production to ensure it is running at the most energy-efficient setting.
The design of the QX-500 also focused on maximizing quality and convenience for consumers. Ishida’s new ‘IntelliSeal’ technology (patent pending) ensures excellent seal integrity for extended shelf life while providing ease of opening. The system constantly measures the sealing force of the tray sealer to optimize sealing pressure, temperature and time for each cycle. This enables the QX-500 to adapt itself to each packaging format.
In the factory, a unique tool change system allows tools to be changed within ten minutes, while a new tray delivery and transfer system offers smooth tray and product handling to ensure maximum seal accuracy and spillage-free product transfer.
“The winning of the PPMA Award is an outstanding achievement and a fitting tribute to everyone who worked on the development of this game-changing tray sealer,” said Ishida Europe’s Marketing Director Steve Jones.
Jones added: “Understanding and responding to customer needs and concerns has always been central to Ishida’s new product development programs. The positive response we have received to the launch of the QX-500 demonstrates the value of this approach, and the Innovative Packaging Machinery Award is the perfect conclusion to this hugely successful project.”
COLLAPSE ARTICLE ABOVE
Sidel unveils StarLITE®R, a 100% rPET bottle for carbonated soft drinks
To help carbonated soft drink (CSD) packaging producers embrace material circularity, Sidel has launched StarLITE®R – a 100% rPET bottle. Sidel’s signature StarLITE® family is evolving to address the challenges associated with working with recycled content.
StarLITE®R allows CSD producers to switch to rPET bottle production with ease and efficiency, while significantly reducing the impact on product quality or packaging integrity.
Embracing 100% rPET
With over 45 years of experience in the blowing and PET packaging sector, Sidel has developed a deep understanding of recycled PET resin characteristics and their impact on bottle production. Laurent Naveau, Packaging Innovator Leader at Sidel, comments on the challenge rPET resin can present the packaging industry:
“The characteristics of rPET are impacted by several factors. Firstly, by seasonality. Consumption habits fluctuate over the course of the year, impacting the product category mix. And secondly, by different PET collection models, which means that post-consumer PET material bales will vary from region-to-region and even country-to-country. The recycling process and equipment used will also influence PET resin. All these factors can pose new challenges for manufacturers looking to produce bottles with rPET content.”
READ MORE
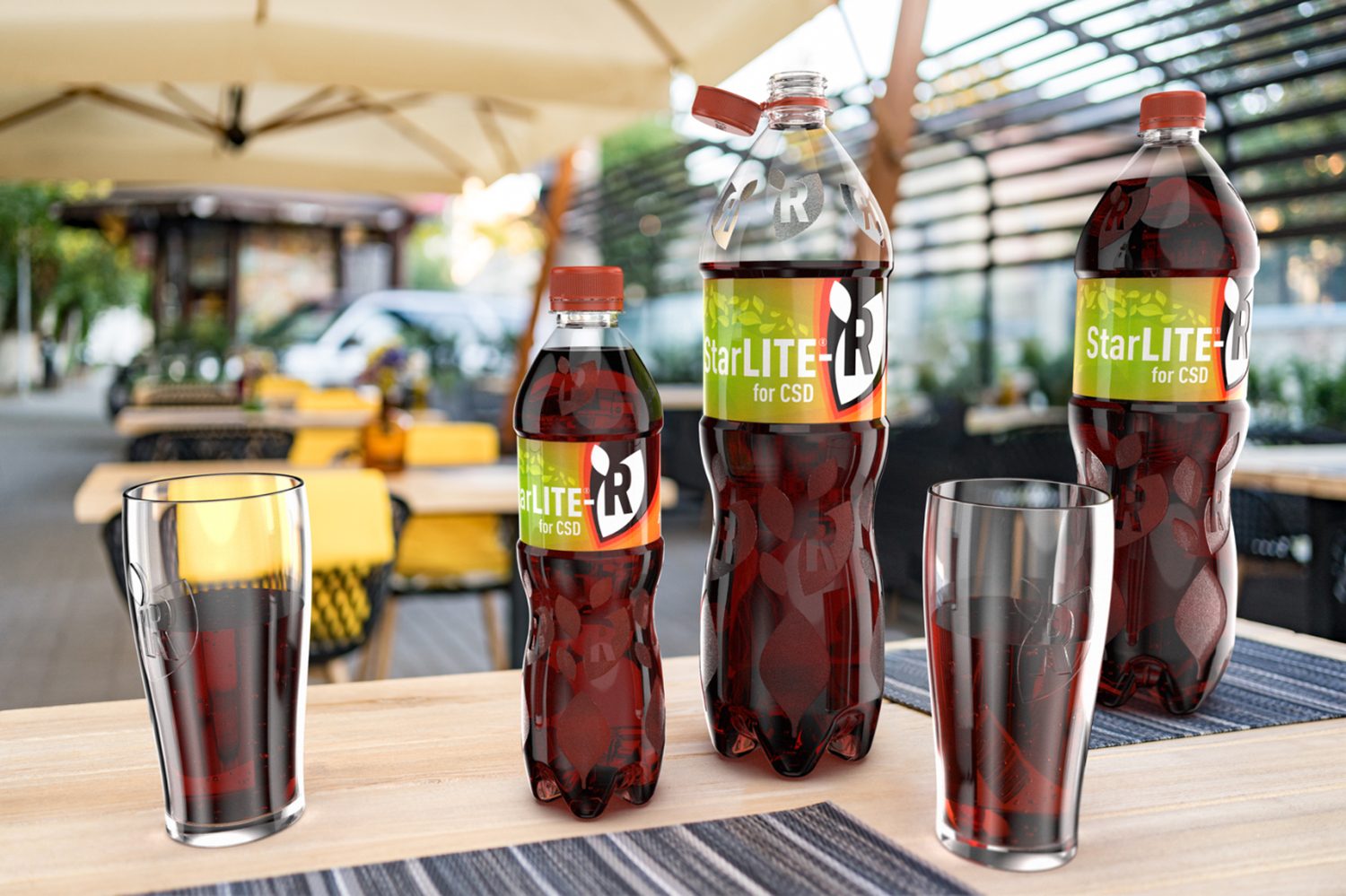
Sidel’s new 100% rPET bottle – StarLITE®R – benefits from the company’s deep understanding of recycled PET resin characteristics and their impact on bottle production.
Courtesy of Sidel
In addition to common CSD bottle manufacturing challenges such as stress cracking, roll out and bursting during blowing, a higher temperature is also required to process rPET. Consequently, packaging manufacturers can experience reduced control over rPET material stretching and distribution of the substance in the bottle-making process.
Traditionally, greater variability in rPET resin leads to a narrower process window and lower bottle quality. However, Sidel’s innovative base, StarLITE®R, uses leading technologies to ensure efficient rPET bottle production by restoring a much wider process window. The StarLITE®R design is easier to blow as it can be done within a wider range of parameter settings on the blower achieving a much higher quality bottle.
High performance rPET bottle base
To achieve a high performing rPET bottle base, StarLITE®R features an optimized mold base profile and uses an advanced stretch rod end design.
The new mold base profile allows for perfect material distribution through advanced stretching and a high base clearance for optimum stability. The advanced stretch rod end design has improved the preform end-cap material stretching and ensures accurate injection gate centering on the bottle. Finally, the perfect combination of grooves and venting holes allows for high-precision base feet formation.
The new bottle solution also utilizes dual external and internal bottle base cooling to ensure a perfect shape. Externally, the process uses a mold base cooling circuit that focuses on the warmer bottle base zones and internally a hollow-stretch rod requiring no additional air supply is used.
Laurent Naveau adds: “StarLITE®R is designed to offer carbonated soft drink manufacturers the opportunity to embrace rPET. Sidel’s new design bottle base achieves greater protection against deformation, increased resistance to bursting and optimum stability, while guaranteeing product quality.”
Seamless transition
Utilizing Sidel’s expertise, the new bottle can be easily installed on existing production lines and adapted to fit current bottle designs. The solution is compatible with Sidel’s signature blow molders, EvoBLOW, Universal and Series 2 and suitable for high-speed productions.
Carbon footprint reduction
Lifecycle analysis shows that PET already has the best carbon footprint of all the packaging materials currently available and is the only food-grade, bottle-to-bottle plastic resin. Achieving full circularity at scale will make PET an even more sustainable choice since rPET reduces environmental impact up to four times more than virgin material.
Find out more about StarLITE®R for CSD on the Sidel website.
COLLAPSE ARTICLE ABOVE
Ranpak provides NeoPharm with eco-friendly protective packaging
NeoPharm aims to be the “Global No. 1 Beauty & Healthcare company that provides the best value of life,” and it has been growing and innovating for more than 20 years.
Satisfied customers worldwide use products such as “Atopharm” skin care for infants and toddlers with sensitive skin, and medical skincare products under the “Zeroid” brand. Alongside a commitment to ensuring healthy skin, the company is strongly focused on ESG management, with a commitment to discover new eco-friendly materials and green packaging.
Cutting down on plastic waste was a priority, and by pursuing a circular economy NeoPharm is thinking beyond the basics of skin health. They want to think big and play a part in creating a healthy environment for everyone.
Reducing the amount of in-transit damage was another goal. Not only were plastic airbags increasing plastic waste and giving the wrong message to customers about sustainability, but they were also not as effective as needed during transit, making losses too high.
With pressure from both material and labor costs, NeoPharm wanted to achieve a more efficient and more cost-effective packaging line — and one that also imposed a smaller logistical burden.
READ MORE
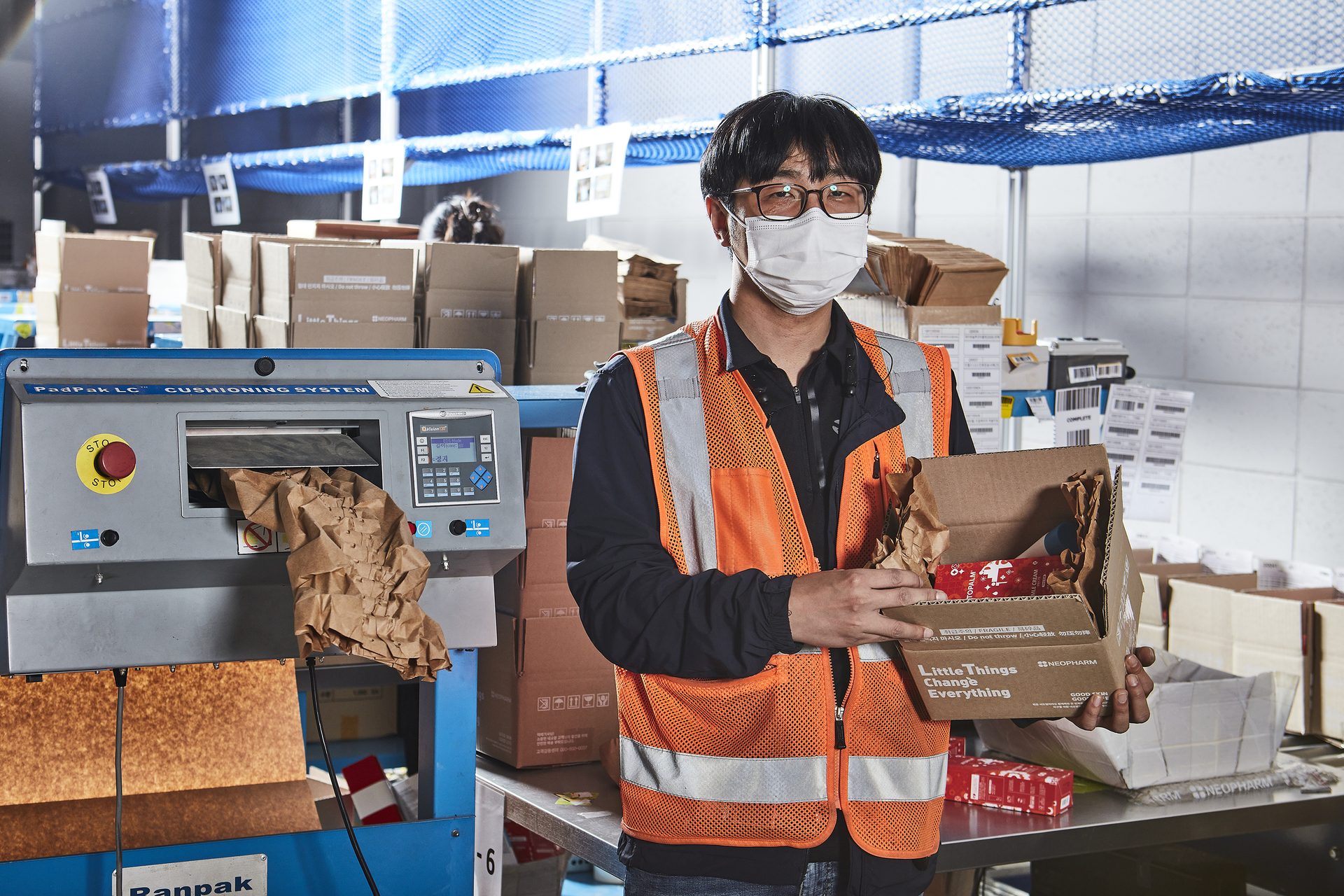
PadPak® LC (Light Cushioning) converters use kraft paper, fan-folding it into light cushioning pads that are well suited to cushioning, blocking-and-bracing, and void filling.
Courtesy of Ranpak
Ranpak’s Solution
After consulting closely with NeoPharm, Ranpak suggested replacing the existing plastic airbag packaging line with PadPak® LC (Light Cushioning) converters. These converters work entirely plastic-free. They use kraft paper, fan-folding it into light cushioning pads that are well suited to cushioning, blocking-and-bracing, and void filling. The pads are created using a patented folding and stitching process, and five different modes of operation enable both batches and individual pads to be made.
An answer to NeoPharm’s ESG commitments
NeoPharm has been able to make further progress on sustainability by switching to plastic-free packaging, in line with its ESG commitment to 100%-recyclable material. This has also had the additional benefits of improving customer experience and boosting brand reputation with curbside-recyclable packaging. By using paper packaging, the company is also better placed to comply with forthcoming changes in regulations.
Fewer packages damaged in transit
The PadPak cushioning pad is designed to offer excellent shock absorption, and NeoPharm now benefits from the protection in transit needed to reduce losses from damages. No more than one or two packages out of every 100 are now damaged, thanks to a protective pad formed directly around the products.
A cost-effective resource
Labor costs have dropped thanks to a quicker packaging cycle and an estimated reduction in working hours equivalent to around two staff members. Logistics and stockroom requirements are simpler because one material (kraft paper) now meets all packaging requirements, replacing the previous two types of pre-made airbags.
Yangsu Kim, CEO of NeoPharm, said, “Ranpak’s eco-friendly packaging was ideal for our ESG and social responsibility commitments. Their consultation was very helpful, and our packaging is now more protective and cost efficient. It’s good to have a partner who helps with solutions that meet both our environmental and business needs.”
COLLAPSE ARTICLE ABOVE
Baystar transforms PE production with North America's first Borstar technology unit
Baystar (Bayport Polymers LLC) has launched a new era in high-performance polyethylene (PE) production and enhanced sustainability with the start-up of its new Bay 3 polyethylene unit. The new unit is the first of its kind in North America, bringing proprietary Borstar technology from Borealis and more than doubling Baystar’s production capacity in Pasadena, Texas.
The Borstar technology brings a transformative approach to production flexibility for manufacturers and converters seeking a broad range of highly customized products for lighter, more durable, more flexible, and more efficient plastics. Borstar products are PFAS-free and can enable more than 50% postconsumer recycled material in some end products. Thanks to a broad molecular weight distribution, Borstar PE offers superior physical properties with no need for process aids or additives.
READ MORE
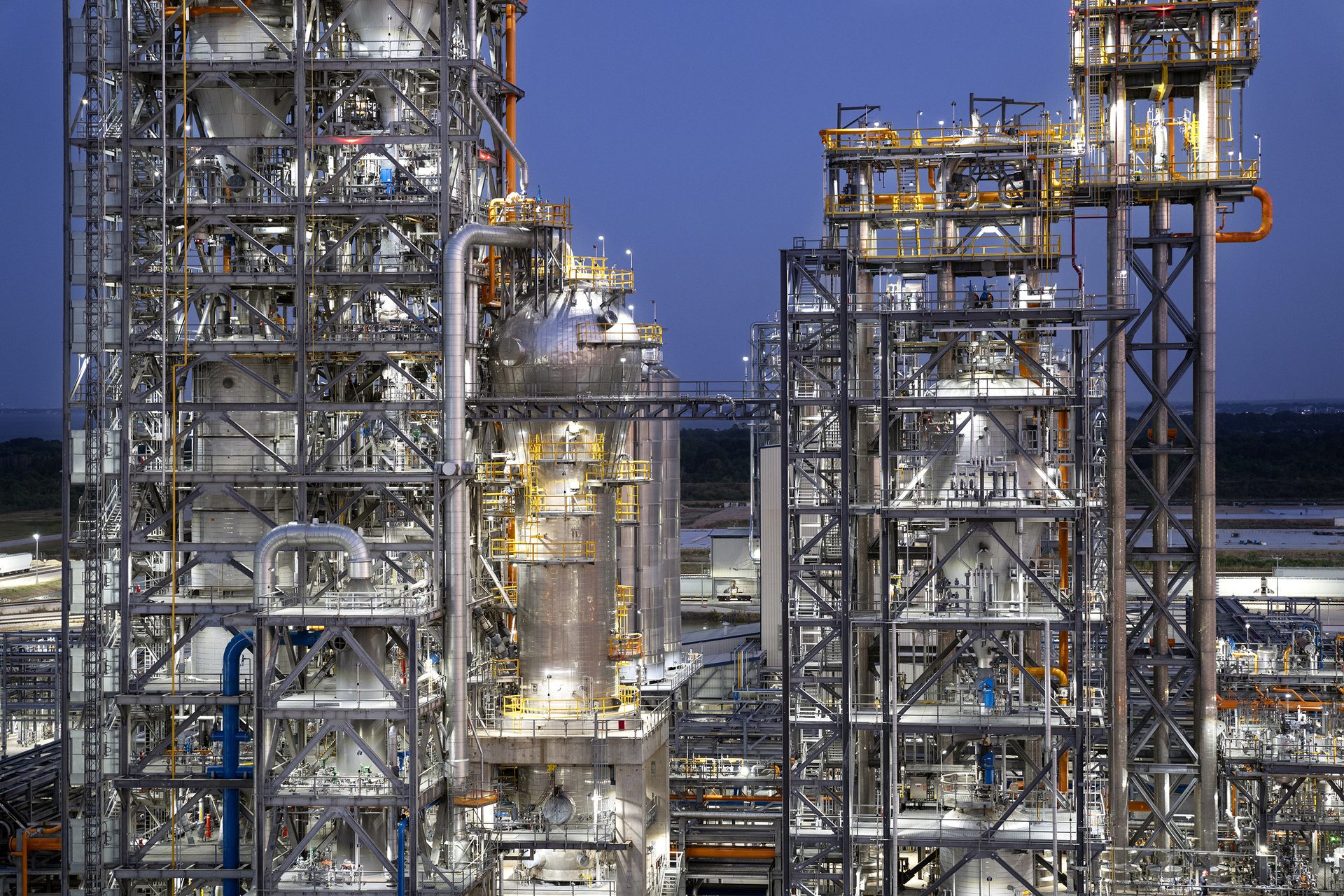
Baystar's new Bay 3 polyethylene unit.
Courtesy of Baystar
“Bringing our new unit online marks the beginning of an exciting evolution in PE production for the industry as Baystar reimagines what is possible,” said President Diane Chamberlain. “Borstar technology enables our technical, production, and sales teams to collaborate in the creation of the highly customized products our customers require to remain competitive and meet consumer demands. This project is the culmination of an enormous investment which began in 2019, and it stands as a testament to the incredible determination, innovation, and relentless focus on safety demonstrated by our team and our partners.”
Baystar became a fully integrated polyethylene manufacturer in 2022 with the start-up of its new 1 million ton-per-year ethane cracker unit in Port Arthur, Texas, which supplies ethylene feedstock to Baystar’s three PE production units. With a total investment exceeding $1.4 billion, construction of the Bay 3 unit employed over 1,900 on-site workers and will provide full-time employment for an additional 50 skilled workers in the Pasadena region.
“We have a product offering second to none, backed by a talented team of experts who came to Baystar to be part of something special,” said Commercial Director Brad Leesman. “We’re big enough to introduce leading technologies, but small enough to be nimble and highly responsive on behalf of our customers. We look forward to surprising the industry with our new approach.”
Baystar was formed in 2018 by Novealis and TotalEnergies and operates independently as an integrated producer. The state-of-the-art Borstar technology is licensed by Borealis.